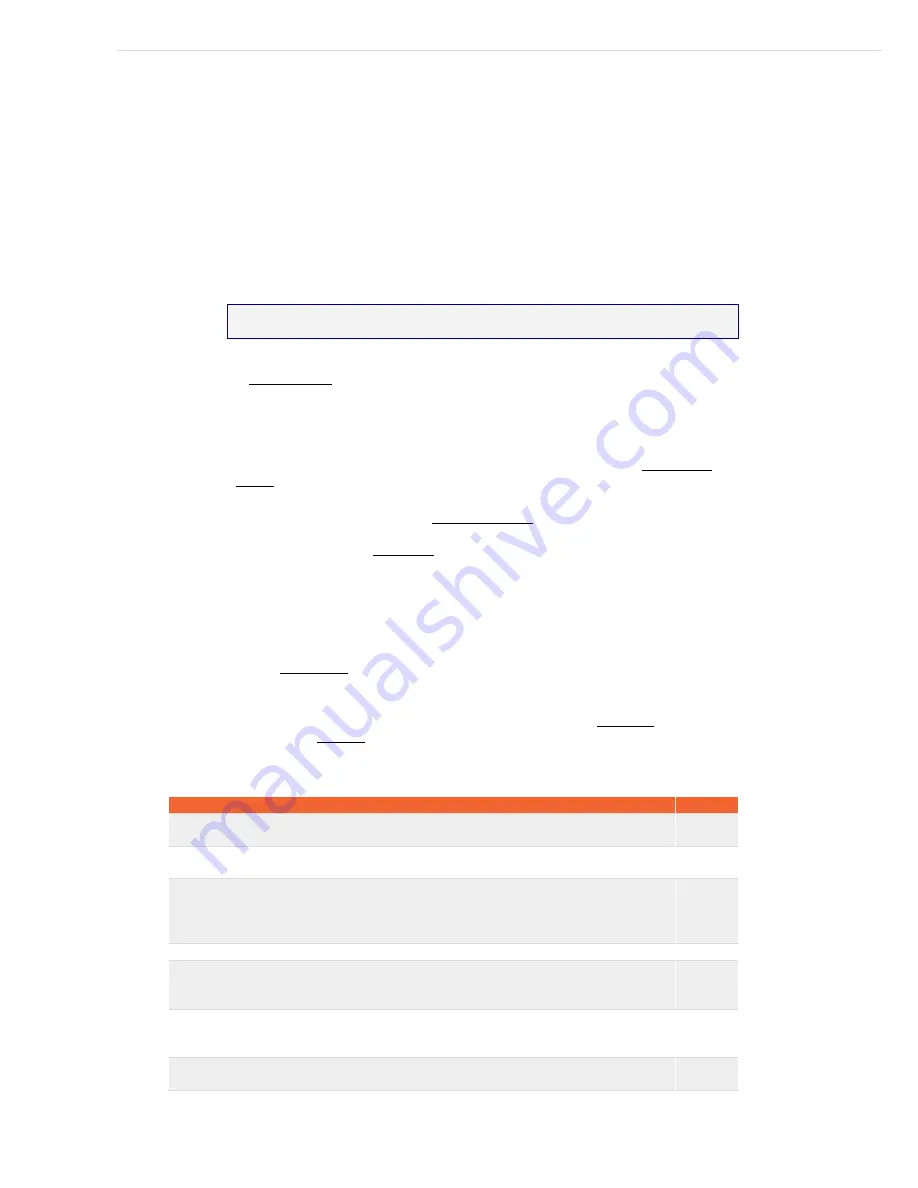
4-262
Flow-X─ Function Reference
Flow-X General functions - fxPID
fxPID
PID control is a generic method to control a process variable by means of a feedback control loop and is
widely used in the industry.
A PID controller adjusts its control output by applying a Proportional, Integral and Derivative algorithm
based on the error between the measured process variable and the desired setpoint.
The Proportional part of the algorithm determines the reaction to the current error. The Integral part
reacts to the recent errors accumulated over a sliding time window, while the Derivative part reacts to
the change rate of the error. The 3 actions are added up by applying individual weigh factors and the
sum is used to adjust a control device, e.g. the position of a control valve.
Note: In flow measurement systems typically only PI control is applied, so the
derivative action is disabled.
The Flow-X PID function provides several features for enhanced PID control such as:
In cascade control there are two PID control loops arranged with one loop controlling the
set point of the other loop. Within the outer loop the primary physical parameter is
controlled, such as fluid level or velocity. The inner loop reads the output of the outer loop
as its set point and usually controls a more rapid changing parameter such as flow rate or
acceleration.
For systems with a slow responsiveness to disturbances or setpoint changes feed forward
control may be beneficial. Besides of the closed PID loop an open feed-forward loop is
added that reacts immediately to a change in process or setpoint value.
The function provides the option for bumpless transfers between auto and manual mode
and vice versa. The actual process value is copied into the required setpoint value while
manual mode is enabled (PV tracking). When reverting to auto mode the process will stay
on the current process value. For the same reason the actual output % is copied to the
manual output % while Auto mode is enabled.
When the control output reaches its limit (e.g. control valve is fully opened) there is the risk
for wind-up of the integral part, because the error will continue to be integrated. This results
in the integral part to become very large, so the error must have the opposite value for a
long time before the control loop returns to normal. In order to avoid this windup (i.e.
achieve anti-windup) the function compensates the integral part when the control output
has reached its limit.
To avoid that a change in setpoint value will result in an impulse in the control signal the
function provides the feature to define a maximum for the setpoint clamp rate and the
control output slew rate. The setpoint clamp rate causes the setpoint to change gradually
until it has caught up with the required value. The slew rate directly limits the rate of
change of the control output.
Function inputs
Remark
EU
SW tag
Range
Default
Name
Optional tag name, tag description
and tag group
Process value
This represents the actual process
value that is being controlled
EU
Setpoint value
The control loop will try to achieve
this input value provided that both
the 'Manual mode' and 'Cascade
mode' are disabled.
EU
Proportional gain
Proportional gain factor
-
Integral gain
Integral gain factor
The value 0 disables the integral part
of the PID algorithm
s
Derivative gain
Derivative gain factor
The value 0 disables the derivative
part of the PID algorithm
s
Low scale value
Process / setpoint value that
corresponds to 0% of the control
EU
Summary of Contents for flow-x
Page 1: ...Function Reference Certified flow calculations Flow and batch calculations Worksheet functions...
Page 331: ...Flow X Function Reference 5 331 Flow X IO Functions fxPT100Table...
Page 349: ...Flow X Function Reference 6 349 This page is intentionally left blank for user notes...
Page 350: ...6 350 Flow X Function Reference This page is intentionally left blank for user notes...