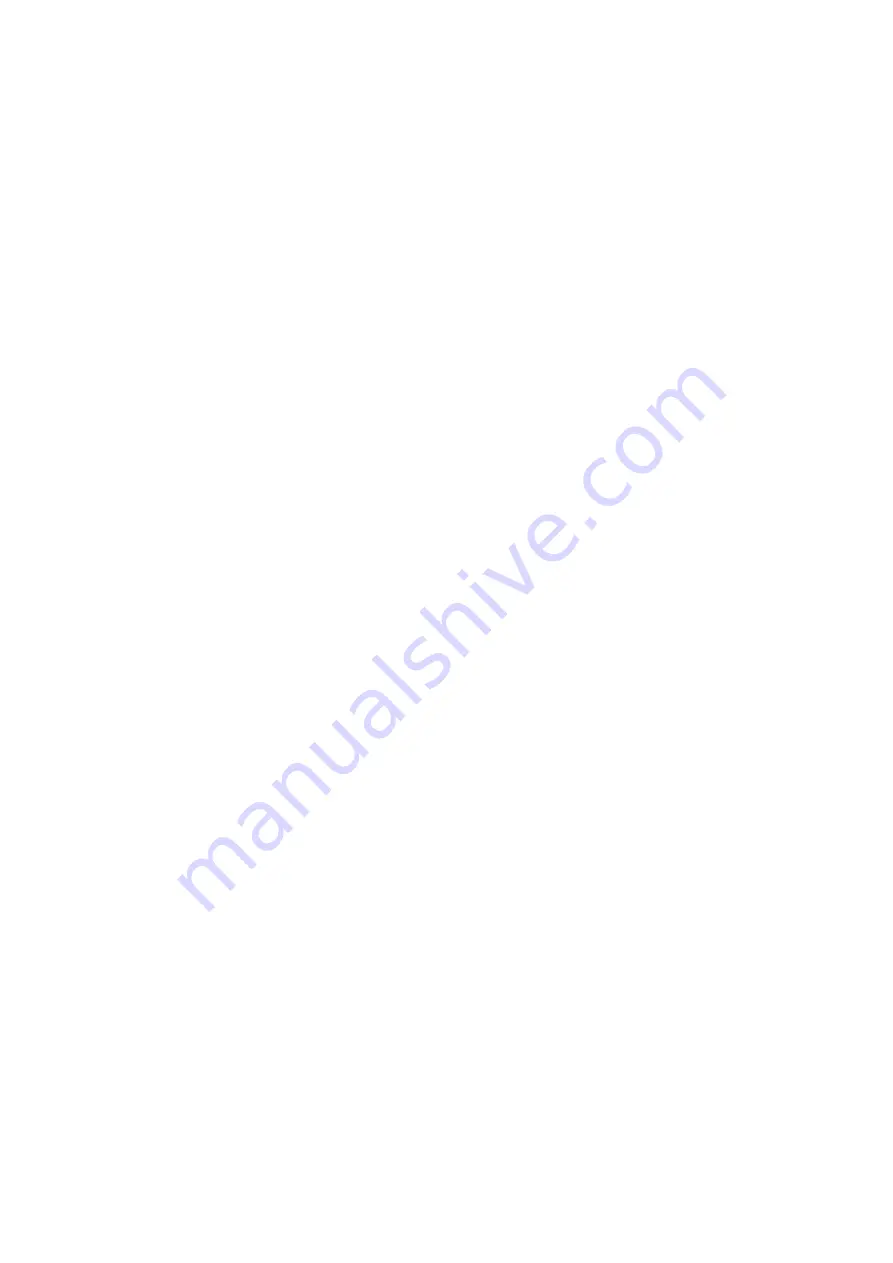
- 15 -
INSTALLATION
1. For full and perfect performance the drum will require at least 6 horizontal flights and
diameter of at least 0.750 mtr.
2. The cone needs to be positioned just below the screw feeder and the spray heads
needs to be positioned inside the drum facing the tumbling product at a 45º angle.
3. Attach the powder hose from the injectors under the cone to the inserts on the spray
head, then pull up the locking ring to hold the tube in place (page 13 item 5). The
powder tube must always go from the injector down hill to the spray head taking the
shortest rout.
4. The product to be coated must be able to fully tumble and roll in front of the spray
pattern. If it does not do so the electostatic effect will not activate properly and will give
a poor quality finish to the product.
5. The appropriate distance between the spray head air cap and the product to be coated
to be of about 20 - 45 cm / 8" - 18" (minimum distance is 15 cm / 6").
6. The control unit must be located outside the flavouring drum.
7. All metal parts, pumps, containers, conveyors (feeding in and out of the drum)
and any other conductive article within 2mtrs/ 6ft - must be grounded.
8. The cone must be attached to earth.
9. Keep the spraying area clean. Remove all unnecessary metal components.
10. After fixing the the electrostatic generating head in place inside the drum. Fix the black
cable with plug attached to the back of the control attachment, to electrical plug maked
“1” and lock into place. (Locking mechanism already attached to control) If using a twin
head system attach both black cables, first to “1” and the second to “2” . [see control
drawings under page 7 Item 16]
11. After fixing the electrostatic generating head in place inside the drum. Fix the 8mm air
line to the bottom air fittings on the back of the control to fitting “1” Push in firmly. If
using a twin head system attach both 8mm air lines, first to bottom air fitting “1” and the
second to bottom air fitting “2” . [see control drawings under page 7 Item 10] The other
end of the air lines attached to the air fittings on the injectors.
12. The two upper air fittings on the control are for blowing down the line for cleaning
during spice change. The control is delivered with blank off plugs fitted. Remove a
blank off plug and insert the 8mm air line (Push in firmly) which is attached to the blow
down gun.
13. Plug into rear of control (Item.12) a10mm air line from the main air supply.(The air
always has to be clean and dry. Fit a filter if necessary)