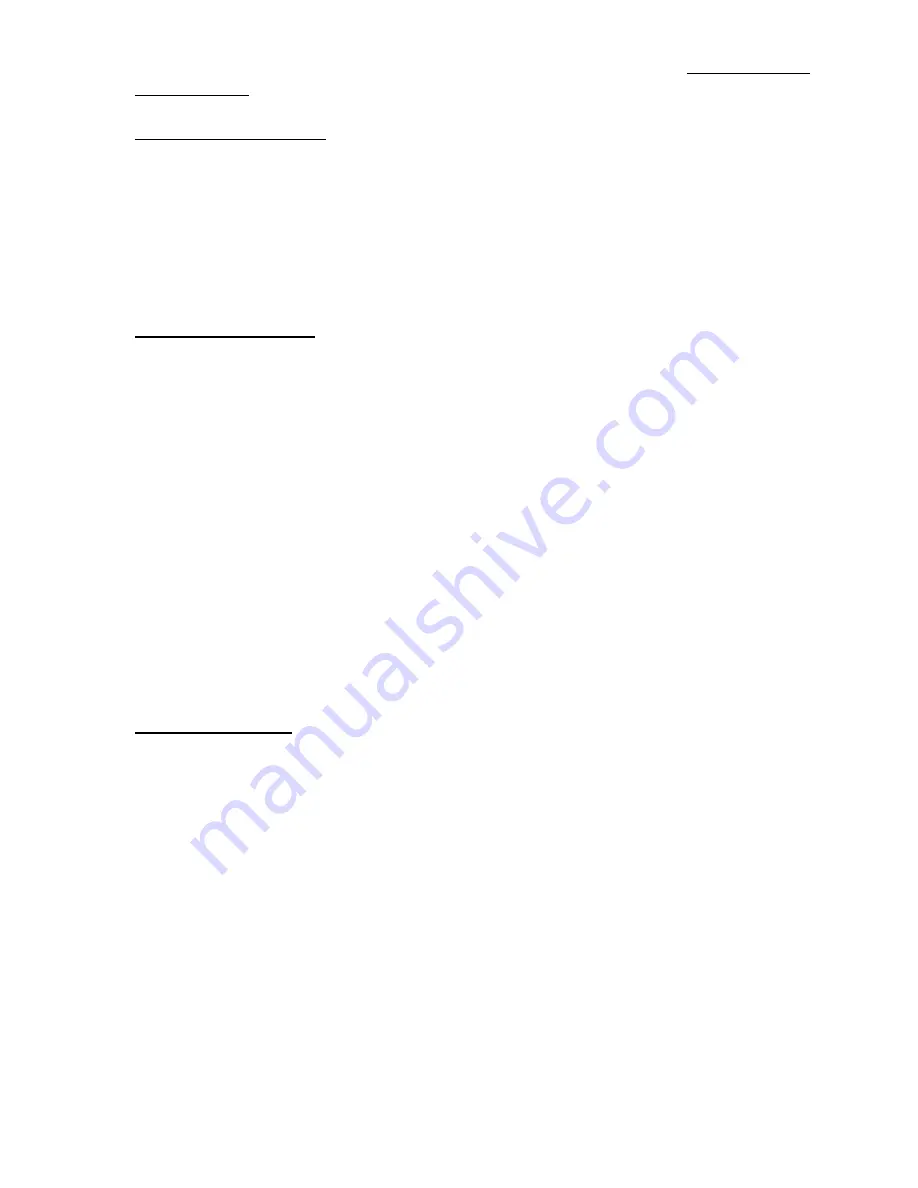
8530 Shatterbox
Page 17 of 28
SPEX SamplePrep LLC January 2010
6.0 MAINTENANCE
6.1 Shatterbox Part Numbers
Following these written instructions are a parts list and diagrams (pages 22-24) of the
Shatterbox mechanism and cabinet. Note that all SPEX parts have 5-digit inventory numbers
that must be used to order them. However, most of these parts also have 1-digit or 2-digit
numbers that correspond to the part's position in an engineering drawing. Example: the
screws, which hold the columns in place, are part no. 26 in Diagram A, but must be ordered as
SPEX Part No
.
50619.
6.2 Cleaning the Shatterbox
Depending on how dusty the working environment is it may be necessary to clean the
Shatterbox regularly. The clamp and capsule retainer should be vacuumed or wiped off. Any
spilled powders or liquids should be wiped up immediately with a slightly damp cotton cloth after
every use. This should minimize the buildup of any powders, mold/mildew, or unsightly gunk over
the life of the unit. To clean the Shatterbox mechanism, remove the access panel on the back of
the cabinet (after unplugging the mill) and vacuum the exposed surfaces.
For a properly functioning Cam-Action Clamp, it is
absolutely necessary
that the lever assembly
roller rotates smoothly (Diagram A, Item 13). Clean off any excess dust or dirt from the outer
segments of the clamp, with special attention being placed on the hinge sections and on the roller.
It may be necessary to oil the hinge and the roller from time to time. If the roller locks up, the
clamp can be easily damaged.
NOTE: It is important to unplug the unit from its power source before beginning any cleanup
or maintenance work that is to be performed on the mill.
6.3 Replacing Drive Belts
Special compound O-rings are used as drive belts (Diagram B, Item 34). When a drive belt fails,
all four drive belts should be replaced by SPEX part no. 51793. (Neoprene O-rings will not
work.) Before installing new drive belts, check the clearance between the hubs of the coupling
arm and eccentric arm (Diagram B, Items 28 and 35, respectively); the gap should be between
1/16 inch and 1/8 inch (1.5 mm to 3 mm). If it is more or less than that, loosen the lock screws
on the collar of the coupling arm with a 1/8-inch Allen wrench, adjust the clearance by moving
the coupling arm up or down on the motor shaft, then tighten the lock screws.
Visually inspect the coupling arm and eccentric arm to make sure they are parallel, and not
bent; if they are damaged, they should be replaced.
Install the new drive belts in a diamond pattern, two up and two down as in Diagram B. Spin
the funnel (Diagram A, item 23) by hand to make sure the two arms spin together freely, and
the drive belts are parallel.