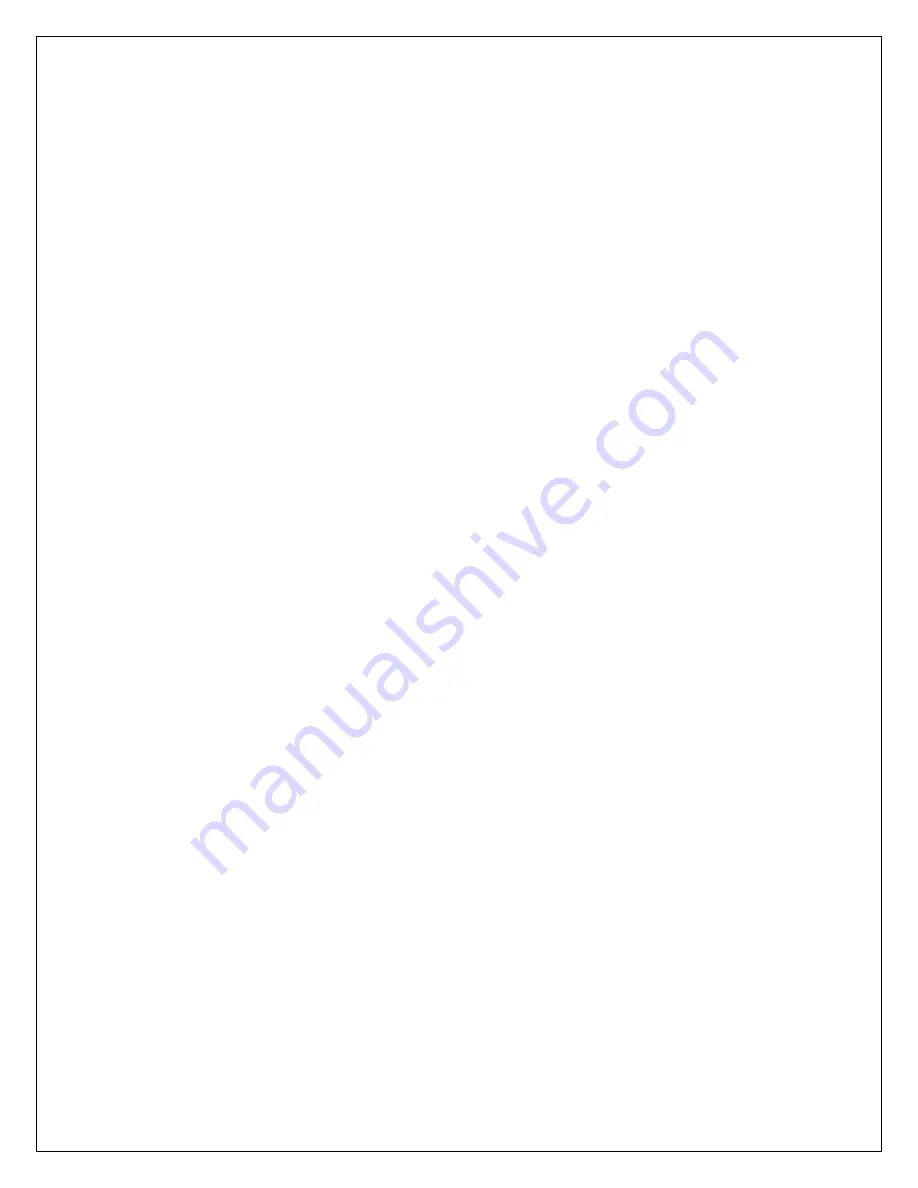
DF3/FF3 MANUAL
20
118018-001
Rev E
4.5
HIGH VOLTAGE
ASSEMBLY
The High Voltage Assembly will vary depending
upon the model ordered. The circuitry typically
consists of a series arrangement of full wave
voltage doublers.
Voltage feedback for regulation and monitoring is
provided by a high band width resistive/capacitive
divider. Current feedback for regulation and
monitoring is provided by a sense resistor
connected at the low end of the High Voltage
Rectifier.
4.6
SYSTEM CONTROL PWB
The majority of control circuits for power supply
controls are located on the SYSTEM CONTROL
PWB. For trouble shooting and testing purposes,
this board can be easily accessed by removing the
four #10 screws on the side near the front panel.
The front panel will hinge down allowing for easy
access to the SYSTEM CONTROL PWB.
+5V dc, +15V dc, -15V dc, and +24V dc, is sent
to the system control PWB from the low voltage
power supply via JB7. X-RAY On/Off control is
accomplished by K2, and its associated circuitry.
Interlock control is also provided by auxiliary
contact of K2. System shutdown is accomplished
by U2. K1 provides control power On/Off
switching. U1 provides a precision 10V dc
reference programming kV, mA and other
references.
Voltage feedback from the high voltage divider is
sent to U3. Gain adjustment is provided by R55
(KVFDBK CAL). The KV feedback signal is
sent to the front panel DVM and to the REAR
PANEL INTERFACE PWB for remote
monitoring. K3 provides switching between
feedback and program signal for the front panel
DVM’s. This allows the user to preset the desired
output before energizing high voltage.
Program voltages are typically ramped up to set
level by the slow start circuits of U8.
Arc sense circuits T1 and U6 provide sensing,
quench and indication of arc conditions.
Current feedback from the high voltage rectifier is
sent to sense resistors R56, R24, and R57. U10
provides gain adjustment (MAFDBK CAL).
An over voltage protection divider located in the
HIGH VOLTAGE ASSEMBLY provides
protection in the unlikely event of a main control
loop failure. U14 provides gain adjustments for
the over voltage protection (OVP) control.
U9, U18 and U12 circuits provide sensing of mA,
kV, fil and power status. These signals are sent to
the PLD, U27 for processing.
The series resonant control circuitry consists of a
voltage frequency and a voltage to phase
converter. U17 generates all frequency and phase
controls. PLD, U27, provides specific phase
control functions for the VCO1 and VCO2
signals.
Signals from the AC PWR/CONTROL PWB, the
INVERTER DRIVE PWB, and the REAR
PANEL INTERFACE PWB are used for control
of the power supply and are processed by PLD,
U27.
System Fault Control and Indication is provided
by U26, U27, U29, U30 and associated circuitry.
Diagnostic signals are latched and then sent to the
FRONT PANEL ASSEMBLY for status
indication. U28 provides power up and remote
reset functions.
U25 provides RMS to DC conversion for the AC
filament current sense transformer. U22 and U23
provide the regulation control and frequency
modulation drive pulses for the filament inverter.
4.7
FRONT PANEL
ASSEMBLY
Front Panel controls, meters, and status
indications are connected to the FRONT PANEL
PWB. The FRONT PANEL PWB interfaces
directly to the SYSTEM CONTROL PWB.
LCL/RMT relay switch control is provided by K2
and K3.
4.8
REAR PANEL
INTERFACE PWB
Signals going to and from the remote interface are
sent to the REAR PANEL INTERFACE PWB.
The REAR PANEL INTERFACE PWB connects
directly to the SYSTEM CONTROL PWB. The
rear panel interface provides isolated relay coils,