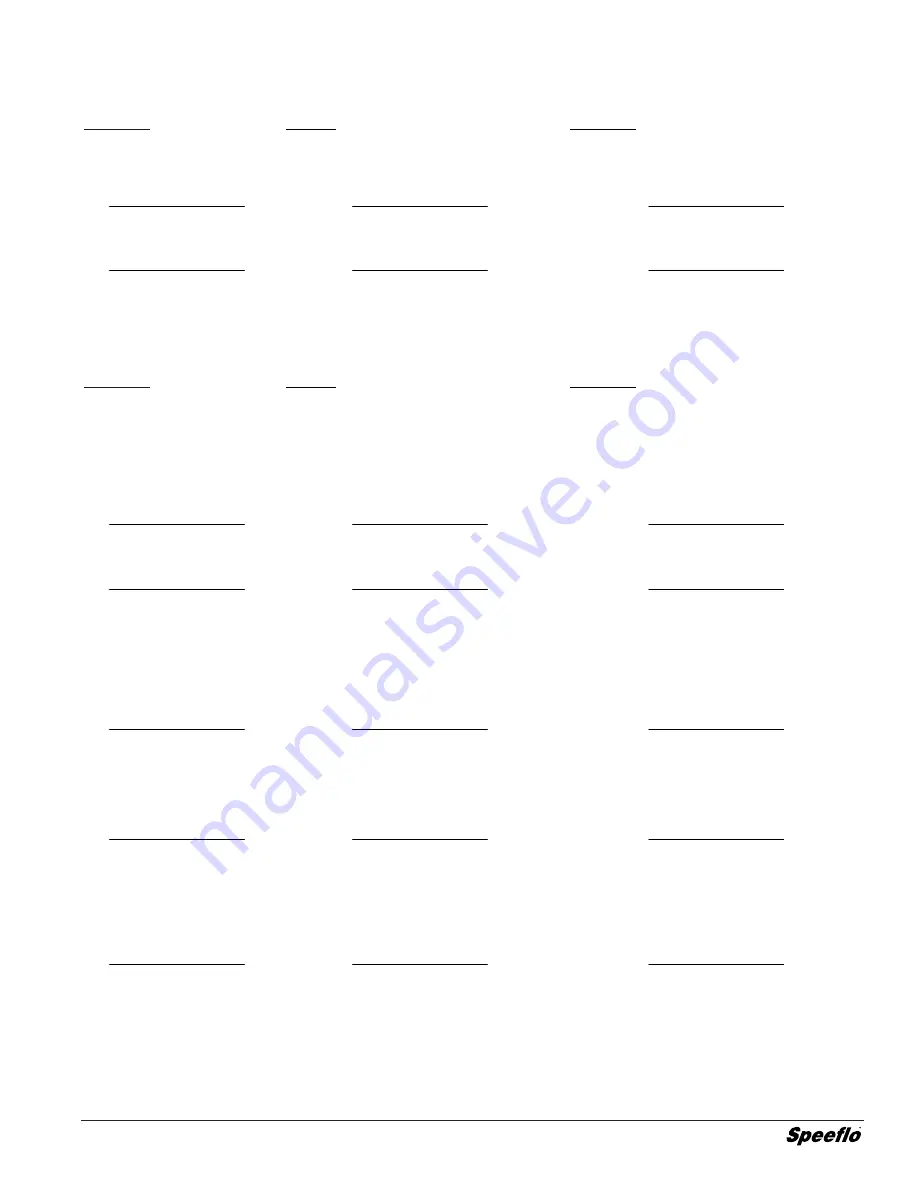
© Titan Tool Inc. All rights reserved.
11
Troubleshooting
Airless Gun
Problem
Spitting gun
Gun will not shut off
Gun does not spray
Fluid Section
Problem
Pump delivers on upstroke
only or goes up slowly and
down fast (commonly called
downstroke dive)
Pump delivers on down stroke
only or goes up fast and down
slowly
Pump moves up and down
fast, delivering material
Pump moves up and down
slowly when spray gun is shut
off
Not enough fluid pressure at
gun
Pump chatters on up or down
stroke
Cause
1. Air in system
2. Dirty gun
3. Needle assembly out of adjustment
4. Broken or chipped seat
1. Worn or broken needle & seat
2. Needle assembly out of adjustment
3. Dirty gun
1. No paint
2. Plugged filter or tip
3. Broken needle in gun
Cause
1. Lower foot valve ball is not seating due
to trash or wear
2. Material too viscous to siphon.
3. Air leaking in on siphon side or
damaged siphon hose. Siphon may be
too small for heavy material.
1. Upper ball is not seating due to trash or
wear
2. Lower packing set is worn
1. Material container is empty or material
is too thick to flow through siphon hose
2. Bottom ball stuck to foot valve seat
3. Siphon hose is kinked or loose
1. Loose connections. Bleed valve is open
partially or bleed valve is worn. Lower
packing seat is worn.
2. Upper and/or lower ball not seating
1. Spray tip is worn
2. Outlet filter or gun filter is clogged
3. Low voltage and/or inadequate
amperage
4. Hose size or length is too small or too
long
1. Solvent has caused upper packing to
swell
Solution
1. Inspect connections for air leaks.
2. Disassemble and clean.
3. Inspect and adjust.
4. Inspect and replace.
1. Replace.
2. Adjust.
3. Clean.
1. Check fluid supply.
2. Clean.
3. Replace.
Solution
1. Remove foot valve assembly. Clean and
inspect. Test foot valve by filling with water;
if ball fails to seal the seat, replace ball.
2. Thin material — contact manufacturer for
proper thinning procedures.
3. Tighten all connections between pump and
paint container. If damaged, replace. Switch
to larger diameter siphon set.
1. Check upper seat and ball with water. If ball
fails to seal, replace seat.
2. Replace packing set if worn.
1. Refill with new material. If too thick, remove
siphon hose, immerse fluid section in
material, and start pump to prime. Add
thinner to material. Change to bigger
siphon set. Open bleed valve to remove
air and restart pump.
2. Remove foot valve. Clean ball and seat.
3. Straighten.
1. Check all connections between pump and
gun. Tighten as necessary. If material is
flowing from bleed hose, close bleed valve
or replace, if necessary. Should none of the
above be evident, replace lower packing.
2. Reseat balls by cleaning.
1. Replace.
2. Clean or replace filter.
3. Check electrical service. Correct as
required.
4. Increase hose size to minimize pressure
drop through hose and/or reduce hose
length.
1. Replace packing.