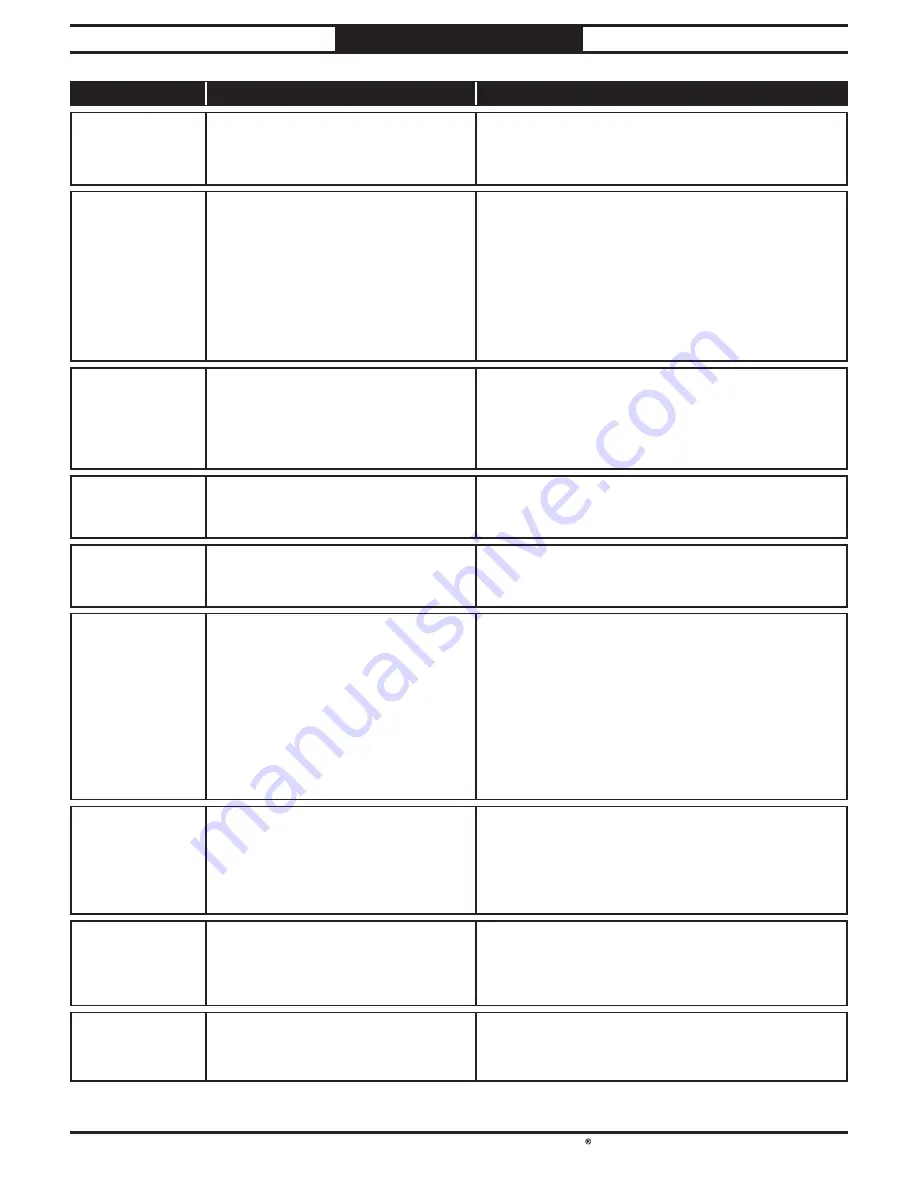
-42-
For Machines Mfd. Since 11/21
South Bend Tools
Model SB1125
TROUBLESHOOTING
Spindle turns
opposite way of
spindle rotation
switch setting.
1.
Motor connections wired out of
phase.
1.
Swap two incoming motor wires (Page 20).
Breaking tools or
bits/cutters.
1.
Spindle speed/feed rate too fast.
1.
Reduce spindle speed (Page 25)/feed rate.
2.
Taking too big of a cut at one time.
2.
Decrease feed pressure and allow chips to clear.
3.
Improper cutting technique or type
of cut for tool/machine.
3.
Use right technique, tool, or machine for job.
4.
Cutting tool too small.
4.
Use larger cutting tool and slower feed rate.
5.
Cutting tool getting too hot.
5.
Use cutting fluid for appropriate application; reduce
spindle speed (Page 25).
6.
Spindle extended too far down
during or at beginning of operation.
6.
Fully retract spindle and raise table to increase
rigidity.
Symptom
Possible Cause
Possible Solution
Worklight does not
illuminate.
1.
Lens covered with dust.
1.
Clean lens.
2.
Master power switch in OFF (0)
position.
2.
Turn master power switch to ON (1) position.
3.
Bulb burnt out.
3.
Replace bulb (Page 40).
4.
Wiring broken, disconnected, or
corroded.
4.
Fix broken wires or disconnected/corroded
connections.
5.
Worklight switch at fault.
5.
Replace switch.
6.
Worklight at fault.
6.
Replace worklight assembly.
RPM digital
readout does not
work/display is
incorrect.
1.
RPM sensor catching on pulley.
1.
Adjust position/replace if at fault.
2.
Wiring broken, disconnected, or
corroded.
2.
Fix broken wires or disconnected/corroded
connections.
3.
Digital readout circuit board at
fault.
3.
Replace.
Tool/arbor falls out
or loose in spindle.
1.
Debris on tool/arbor or in spindle
taper.
1.
Clean tool/arbor and spindle taper; then re-install
(Page 23).
2.
Excessive feed pressure.
2.
Decrease feed pressure and allow chips to clear.
Workpiece or tool
vibrates or chatters
during operation.
1.
Spindle extended too far down
during or at beginning of operation.
1.
Fully retract spindle and raise table to increase
rigidity.
2.
Table locks not tight.
2.
Tighten table locks.
3.
Workpiece not secure.
3.
Properly clamp workpiece on table.
4.
Spindle speed/feed rate too fast.
4.
Reduce spindle speed (Page 25)/feed rate.
Table hard to
move.
1.
Table locked.
1.
Disengage table locks.
2.
Column dirty/needs lubrication.
2.
Clean/lubricate (Page 33).
3.
Dirty or dry column rack and
pinion.
3.
Clean away chips/debris. Lubricate rack and ball
oilers (Page 34).
Spindle does not
fully retract.
1.
Poorly adjusted return spring.
1.
Increase return spring tension (Page 36).
2.
Debris on spindle/quill rack.
2.
Clean and lubricate spindle/quill rack (Page 34).
3.
Worn return spring.
3.
Replace return spring.
Lack of power at
spindle.
1.
Wrong voltage.
1.
Ensure correct voltage (Page 11).
2.
V-belt(s) worn or loose.
2.
Check belt tension/replace belts with a new
matched set (Page 37).