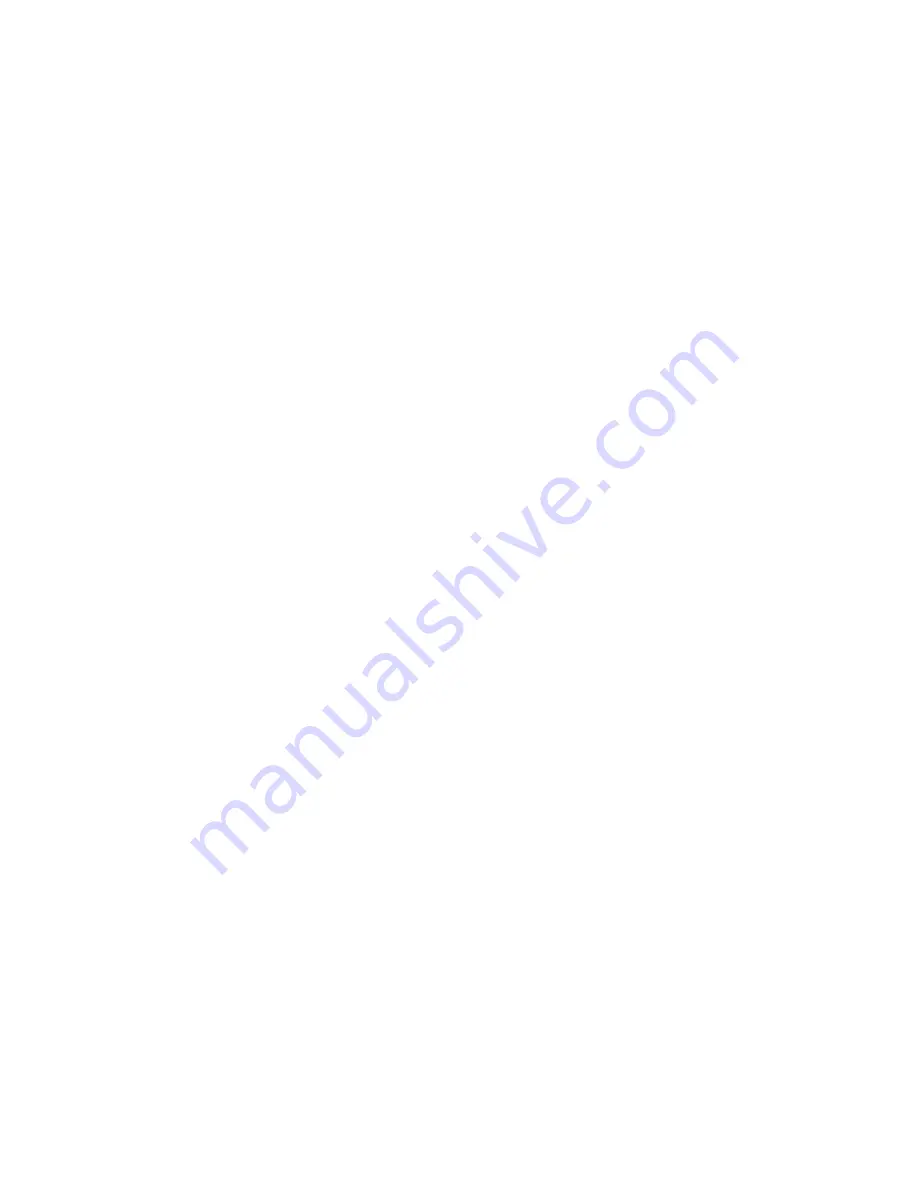
4
Hydraulic Power Unit
The hydraulic power unit consists of:
12VDC Motor
Hydraulic pump rated at 1.54 GPM @ 1500 PSI
1.35 quart capacity reservoir
Fine mesh intake filter
Filter screens on all outlet ports
The fluid supply line for the pump is submerged in the
hydraulic fluid reservoir and is equipped with a fine mesh
intake filter screen.
The 12VDC motor is protected electrically by a 150 Amp
circuit breaker located between the battery and the motor
solenoid.
The hydraulic pump is protected by a 2100 PSI system
relief valve.
This unit may be equipped with a Down Pressure Option
which will allow the operator to selectively switch the
system to provide additional hydraulic force to the cutting
edge of the plow.
IMPORTANT:
The electric coils, which operate the
solenoid valves, require a minimum of 9-1/2 volts DC
for proper operation. Lower voltage will cause erratic
operation, or failure to operate.
Hydraulic Controls
The hydraulic controls consist of:
System pressure relief valve, set to 2100 PSI.
Two crossover relief valves, set to 1750 PSI.
Two wing relief valves, set to 2150 PSI.
Four three-way two position hydraulic valves and four
pilot operated check valves for wing angling functions.
Two double acting hydraulic cylinders for wing angling
functions.
One three-way two position, three two-way two position
valves and two check valves for raise, lower and down
pressure functions.
One down pressure relief valve.
Electro-Hydraulic Controls
All hydraulic functions are controlled by the 12VDC
electrical system which actuates coils on the hydraulic
valves and the solenoid for the electric motor of the power
unit. 12VDC power is fed from the battery post of the
motor start solenoid to a control circuit board on the plow
and from the circuit board to each coil. Each valve is
actuated by completing a circuit to ground through the
coil, and through the circuit board by means of a wire
transmitted signal to the circuit board from the hand-held
controller in the vehicle.
Raise Mode of Operation
Actuating the ’Raise’ switch on the hand-held controller
sends a signal to the control circuit board on the plow
which then actuates the motor solenoid and the coils for
the ’C’ valve and ’F’ valve. Actuating the start solenoid
sends current to the power unit motor to cause the power
unit to pump hydraulic fluid. Hydraulic fluid, under
pressure, is directed through the ’C’ valve to the lift
cylinder causing it to extend and raise the plow. The ’F’
valve is also actuated to allow fluid in the rod end of the
double acting raise cylinder to return to the reservoir.
When the ’Raise’ switch on the hand-held controller is
released the start solenoid circuit is broken and the motor
stops, the circuit to the coil for the ’C’ valve and the ’F’
valve is broken and these valves got to their normally
closed positions.
Lower Mode of Operation - Gravity Down
and Float
Actuating the ’Lower’ switch on the hand-held controller
sends a signal to the control circuit board on the plow
which then actuates the coil for the ’B’ valve and the ’F’
valve allowing hydraulic fluid to flow from the lift cylinder
to the reservoir. Once the ’Lower’ switch has been
actuated, the system will stay in this mode until the raise
function is actuated, allowing hydraulic fluid to flow
between the reservoir and the lift cylinder and let the lift
cylinder extend and retract as necessary to follow ground
contours while plowing.
Lower Mode of Operation - Down Pres-
sure (DP) System
This system operates only when the ’DP’ switch and the
’Lower’ switch on the hand-held controller is actuated.
Actuating the ’DP’ switch (a red LED will be lit) actuates
the pressure switch, the ’B’ valve coil, the ’E’ valve coil
and, through the pressure switch, the start solenoid as
required. When the ’E’ valve is actuated and the hydraulic
pump operates, hydraulic fluid is directed to the rod end of
the lift cylinder compressing the cylinder and forcing the
plow down. The pressure switch in this system senses the
pressure of the fluid in the lift cylinder and closes when the
pressure becomes low, allowing the motor and the pump
to pump fluid into the rod end of the cylinder. When the
pressure reaches the proper level, the switch opens,
shutting off the motor and pump. The system is protected
by a relief valve which relieves excess pressure if the plow
is forced up, such as by a bump or obstacle in the
roadway. Once any obstacle is cleared, the plow can
return to a lower position lowering the pressure in the
system. If the pressure is lowered sufficiently, the
pressure switch will then sense the lowered pressure and
cause the pump to pump fluid into the system and return
it to the proper pressure.
THEORY OF OPERATION
Summary of Contents for 28V Series
Page 26: ...25 NOTES...
Page 28: ...27 HYDRAULIC SCHEMATIC GRAVITY...
Page 29: ...28 HYDRAULIC SCHEMATIC DOWN PRESSURE...
Page 30: ...29 WIRING SCHEMATIC GRAVITY...