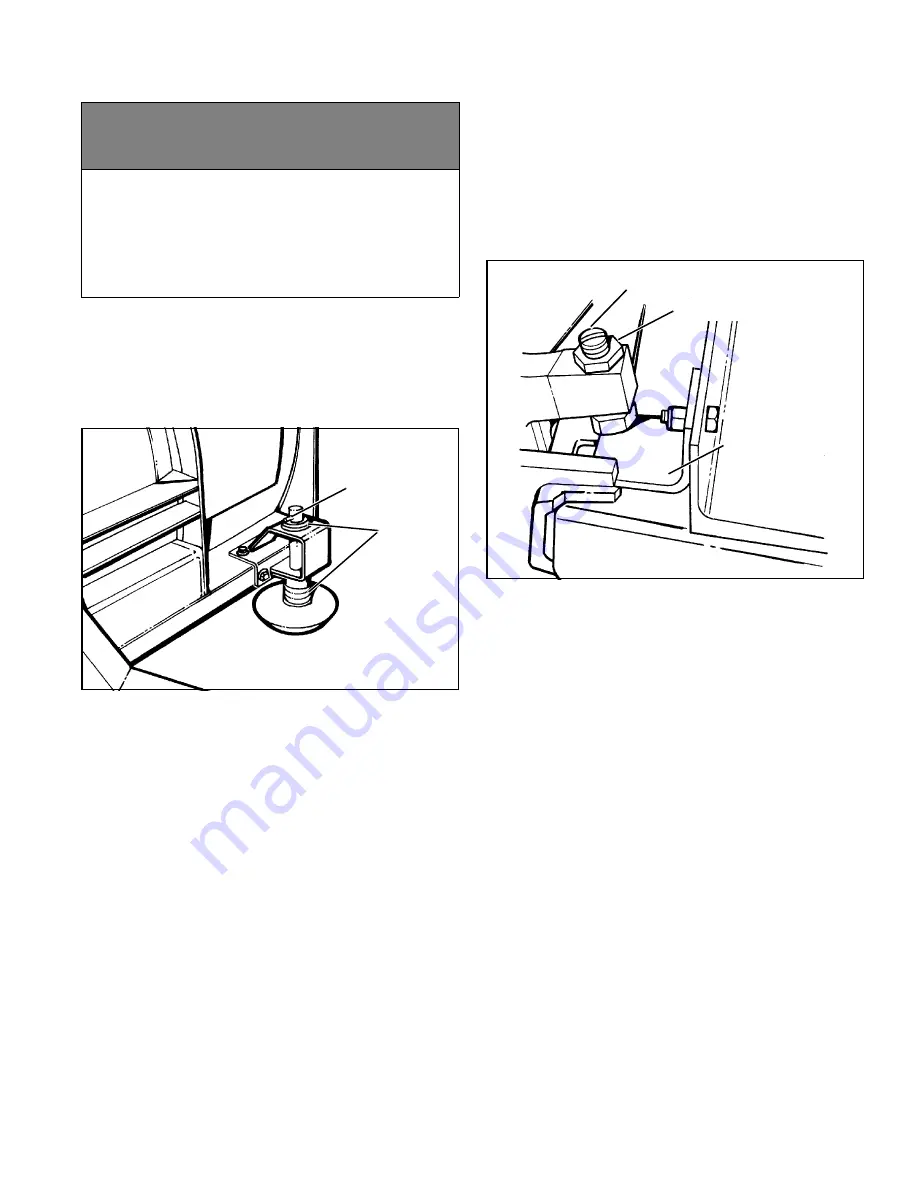
22
13. Lower plow onto blocking.
14. Adjust each disk shoe assembly by removing disk
shoe mounting pin and adding or subtracting washers on
the top or bottom of the disk shoe mounting bracket as
required according to measurements taken in step #11
(See Figure 2-17).
Figure 2-17
15. After the disk shoe position is properly adjusted,
place washers on the disk shoe stem - above the disk
shoe mounting bracket, and below the retaining pin - to
remove all up and down movement of the disk shoe in the
bracket. Failure to do this will result in excessive wear of
the holes in the disk shoe mounting bracket and will also
result in bending the stem of the disk shoe.
16. After the wing disk shoe adjustment is complete,
lower the plow to the ground. If this disk shoe adjustment
is correct, the shoes and the wearstrips will all be on the
ground at the same time, if not, repeat steps #11 to #15.
17. Move the wings forward and rearward. If the wing
wearstrips and the center wearstrips are not on the
ground at all times recheck the position of the wing pivot
tubes. The tubes must be vertical, if they are not vertical,
the center disk shoe will need to be adjusted.
Float Limiter Adjustment
IMPORTANT:
The disk shoes must be properly
adjusted prior to adjusting the float limiter. If the
shoes are not properly adjusted, the float limiter
adjustment cannot be properly made.
1. With the vehicle and snow plow on a smooth, level
surface move the wings forward into the “scoop” position
and lower the plow to the ground.
Figure 2-18
2. Loosen the 5/8" jam nut on the top of the float limiter
adjusting screw.
3. Using the screwdriver slot in the top of the float limiter
adjusting screw, turn the adjusting screw down until the
hex head of the adjusting screw touches the surface of
the replaceable wear plate.
4. Turn the adjusting screw up two turns to provide a
gap between the wear plate and the head of the adjusting
screw for proper float allowance.
5. While holding the adjusting screw driver slot, to
prevent turning of the adjusting screw, tighten the 5/8”
jam nut to lock the adjusting screw and prevent turning of
the adjusting screw during operation.
6. Repeat on other side.
c
WARNING
Keep hands and feet clear of wings and center
section when setting blocking and lowering
plow. Moving or falling assemblies could result
in serious injury.
FAILURE TO HEED CAN RESULT IN INJURY
OR DEATH.
WASHERS
PIN
JAM NUT
ADJUSTING SCREW
REPLACEABLE
WEAR PLATE
Summary of Contents for 28V Series
Page 26: ...25 NOTES...
Page 28: ...27 HYDRAULIC SCHEMATIC GRAVITY...
Page 29: ...28 HYDRAULIC SCHEMATIC DOWN PRESSURE...
Page 30: ...29 WIRING SCHEMATIC GRAVITY...