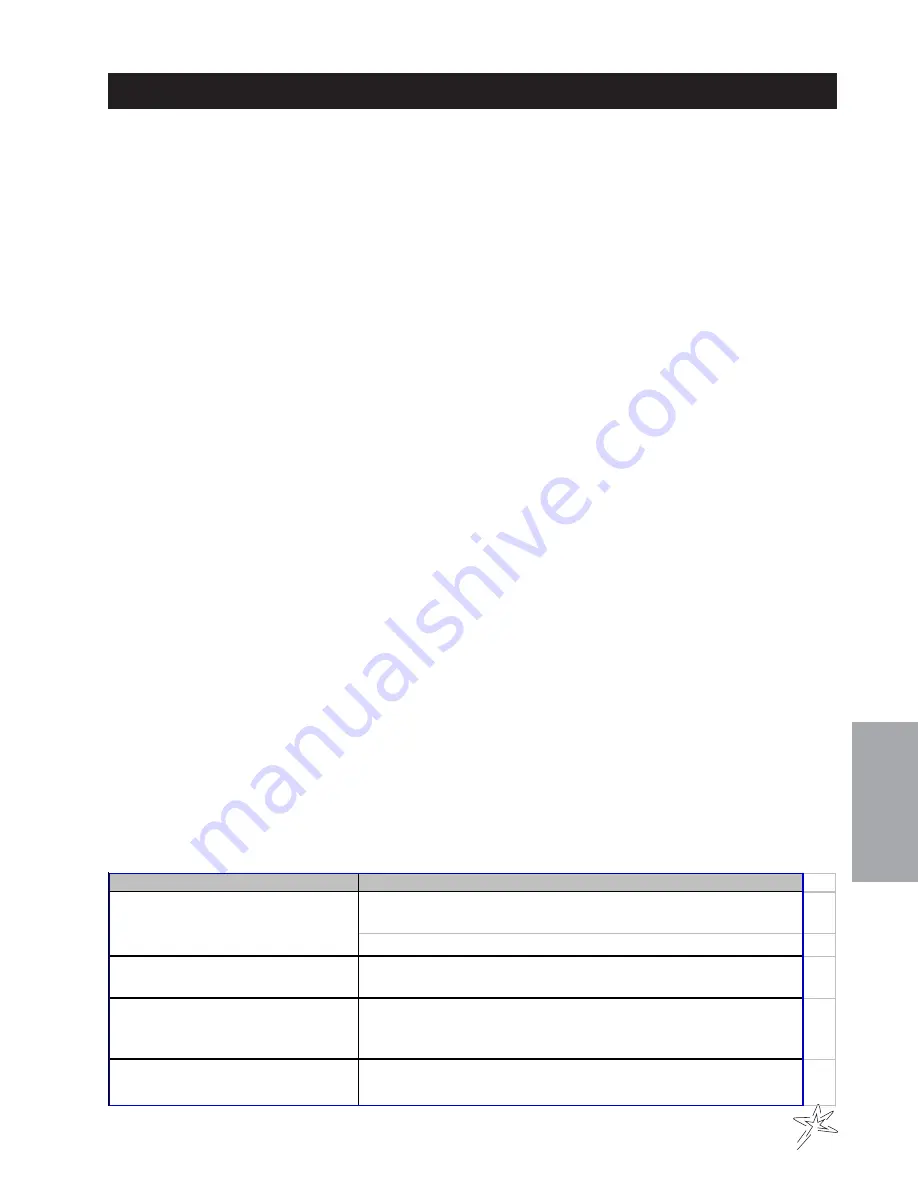
107
Accessories
OPERATING INSTRUCTION
START-UP
1.
All Cleanload valves must be closed prior to starting: inlet ball valve, knife valve and hopper rinse ball valve.
2.
Open lid to check for foreign objects which may hinder performance or contaminate the system.
3.
Close and lock lid by turning cover clockwise.
4.
Divert pump flow to Cleanload inlet line. A pressure of 30 PSI minimum and 150 PSI maximum must be used.
Highest pressures increase eduction rate and available wand suction.
5.
Turn inlet ball valve on (yellow handle).
6.
Open knife valve, located on the bottom of hopper, by pushing handle in (red handle).
7.
Unlock and open lid slowly by turning cover counterclockwise.
LOADING LIQUID OR POWDERED CHEMICAL INTO HOPPER
8.
Pour required amount of chemical into hopper. Avoid splashing liquids or powdered chemicals outside of hopper.
9.
Rinse empty chemical containers if applicable. Place container opening over container rinse valve and press
down. This will activate the rinse valve and rinse container.
10.
Rinse Cleanload hopper. Close and lock lid by turning cover clockwise. Release the safety locking band on the
hopper rinse ball valve and turn on for 20 seconds. Close ball valve and return locking band to locked position.
11.
Open lid and inspect for chemical residue. Repeat step 10 as necessary.
12.
Close knife valve by pulling red handle out towards you. Turn inlet (yellow handle) off.
LOADING LIQUID AND/OR POWDERED CHEMICAL WITH SUCTION LANCE
Note: Lance suction is dependent upon eductor pressure and flow. For best results, use highest pressure
available up to 150 PSI maximum.
8.
Insert lance body with o-ring into eductor until the o-ring is sealed.
9.
Use the free end of the lance to pierce bag or container to vacuum powdered or liquid chemical.
10.
Rinse lance. Place lance end into a clean container of water to rinse lance assembly.
11.
Remove lance body from eductor and drain any remaining fluid into hopper.
12.
Close knife valve (red handle). Turn inlet valve (yellow handle) off.
SHUTDOWN
1.
Ensure that:
• All valves are closed. Be sure to close knife valve first. (Close by pulling red handle out towards you.)
• Chemical residue has been cleaned.
• Hopper lid is closed and locked by turning cover clockwise.
2.
Divert pump flow back to normal operation.
Symptom
Corrective Action
Check pump pressure and flow. Cleanload Eductor performance is based on
flow and pressure to the system. Note requirements for high eduction rates.
Increase outlet hose size back to tank.
Plugged or clogged bottle rinse nozzle
Disassemble rotary portion of nozzle from lower valve assembly and back
flush until nozzle ports are clear of debris.
Plugged or clogged tank rinse nozzle
Disassemble rotary portion of nozzle from NPT hose barb and back flush until
nozzle ports are clear of debris. Remove screen and flush with water to clear
away foreign material.
Fitting leaks
Check for cracks in fitting. Replace fitting if necessary. Disassemble and add
more joint seal in compound if leak occurs on threads.
Low eduction rate
Summary of Contents for 30-000-C
Page 13: ...11 Service NOTES ...
Page 18: ...16 Parts BODY FRAMEDRAWING ...
Page 20: ...18 Parts NOSECONEDRAWING ...
Page 22: ...20 Parts NOSECONEDRAWING ...
Page 24: ...22 Parts LINKAGEDRAWING ...
Page 26: ...24 Parts FRONTAXLEDRAWING ...
Page 28: ...26 Parts OIL FUELTANKDRAWING ...
Page 30: ...28 Parts SEATPANELDRAWING ...
Page 32: ...30 Parts ENGINEANDPUMPS DRAWING ...
Page 34: ...32 Parts ENGINEANDPUMPS DRAWING ...
Page 36: ...34 Parts COOLERANDEXHAUSTDRAWING ...
Page 38: ...36 Parts REARWHEELDRIVEDRAWING ...
Page 40: ...38 Parts TANKDRAWING ...
Page 42: ...40 Parts TURBO QUADAGITATORDRAWING ...
Page 44: ...42 Parts 15 301ORBITROLDRAWING ...
Page 48: ...46 Parts 30 102EATONPUMPDRAWING ...
Page 50: ...48 Parts 30 102EATONPUMPDRAWING ...
Page 52: ...50 Parts 30 101EATONMOTORDRAWING ...
Page 54: ...52 Parts 30 099 AUBURN POWERWHEEL DRAWING ...
Page 56: ...54 Accessories 3182PLUMBINGDRAWING RAVEN440 15 818 75 Fitting O ring 15 817 50 Fitting O ring ...
Page 58: ...56 Accessories 3184PLUMBINGDRAWING RAVEN203 15 818 75 Fitting O ring 15 817 50 Fitting O ring ...
Page 66: ...64 Accessories CONTROLS3182SYSTEMDRAWING RAVEN 440 ...
Page 68: ...66 Accessories CONTROLS3184SYSTEMDRAWING RAVEN 203 ...
Page 70: ...68 Accessories WIRING 3185 3186 SYSTEM ENVIZIO PRO II SHARP SHOOTER W RATE SYNC ...
Page 72: ...70 Accessories WIRING3187 3188SYSTEM RAVEN440 SHARPSHOOTER ...
Page 76: ...74 Accessories 15 743MANIFOLDVALVEDRAWING ...
Page 78: ...76 Accessories 17 58020 HEAVYBOOM ...
Page 80: ...78 Accessories 17 58020 BOOMDRAWING ...
Page 84: ...82 Accessories 17 585 18 HEAVYBOOM ...
Page 86: ...84 Accessories 17 585 18 HEAVYBOOM ...
Page 90: ...88 Accessories 30 010ELECTRICHOSEREELDRAWING ...
Page 94: ...92 Accessories HOSEREELMOUNT DRAWING ...
Page 96: ...94 Accessories 30 004FOAMMARKERDRAWING WIRINGDRAWING ...
Page 98: ...96 Accessories 30 004FOAMMARKERDRAWING ...
Page 100: ...98 Accessories FOAMER NOZZLEMOUNT HOSEGUARDMOUNTDRAWING ...
Page 103: ...101 Accessories NOTES ...
Page 106: ...104 Accessories 30 006FRESHWATERTANKDRAWING ...
Page 110: ...108 Accessories 15 620CHEMICALCLEANLOAD PARTSDRAWING ...