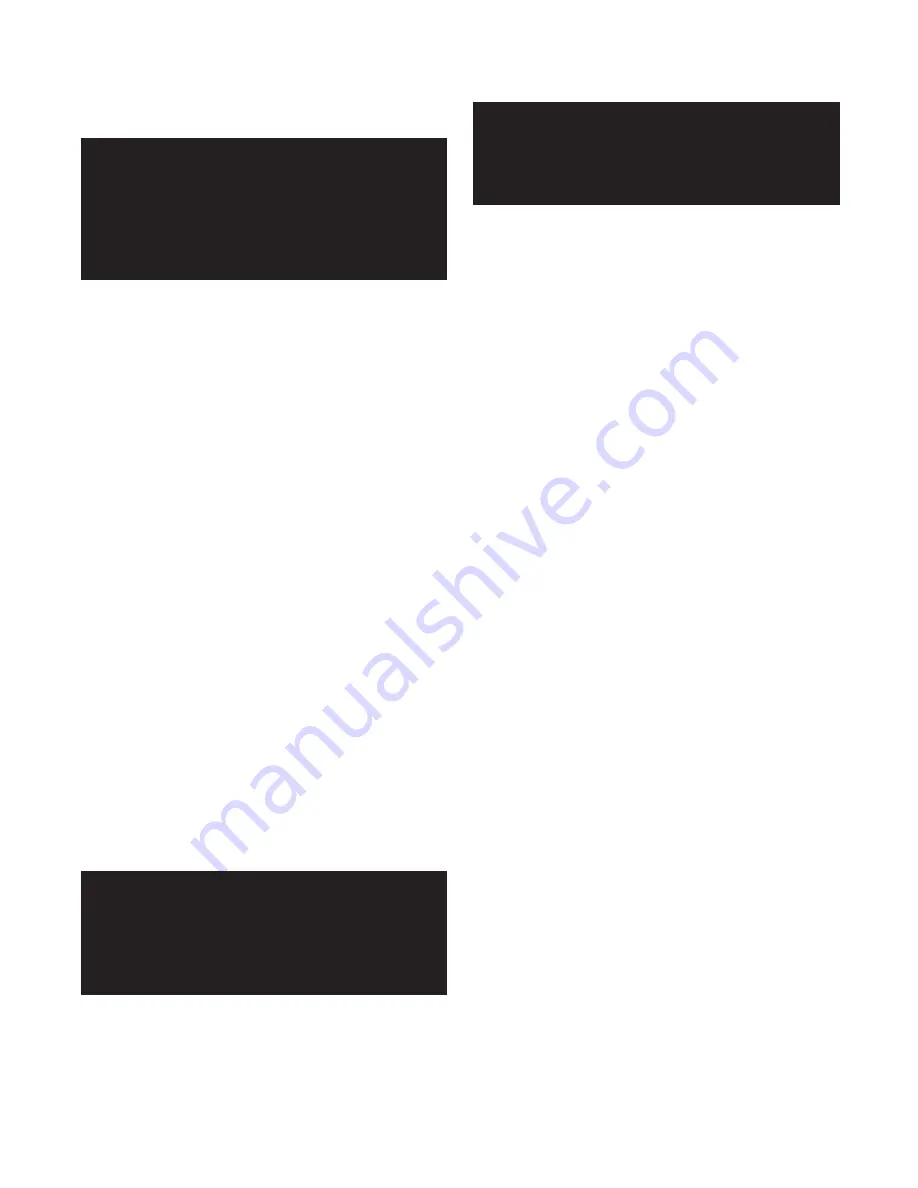
Page 6
SERIES 28HE STEAM BOILER INSTALLATION AND OPERATION INSTRUCTIONS
WARNING: Failure to maintain minimum
clearances between vent connectors and any
combustible material can result in a fi re causing
extensive property damage, severe personal
injury or death!
COMMON VENT SYSTEMS
If an existing boiler is removed from a common venting
system, the common venting system may then be too
large for the proper venting of the remaining appliances
connected to it. At the time of removal of an existing
boiler, the following steps shall be followed with each
appliance remaining connected to the common venting
system placed in operation, while the other appliances
remaining connected to the common venting system are
not in operation.
Au moment du retrait d'une chaudière existante, les
mesures suivantes doivent être prises pour chaque
appareil toujours raccordé au système d'évacuation
commun et qui fonctionne alors que d'autres appareils
toujours raccordés au système d'évacuation ne
fonctionnent pas: système d'évacuation
a) Seal any unused openings in the common venting
system.
Sceller toutes les ouvertures non utilisées du
système d'évacuation.
b) Visually inspect the venting system for proper size
and horizontal pitch and determine there is no
blockage or restriction, leakage, corrosion and other
defi ciencies which could cause an unsafe condition.
Inspecter de façon visuelle le système d'évacuation
pour déter miner la grosser et l'inclinaison
horizontale qui conviennent et s'assurer que le
système est exempt d'obstruction, d'étranglement
de fruite, de corrosion et autres défaillances qui
pourraient présenter des risques.
VENT CONNECTIONS
WARNING: Never modify or alter any part of the
boiler’s smoke hood. This includes the removal
or alteration of any baffl es. Never install a vent
pipe of a diameter different than that of the
boiler smoke hood outlet. Failure to comply with
this warning can result in severe personal injury
or death.
Locate the boiler as close to the chimney as possible.
Use the shortest, straightest vent connector possible
for the installation. If horizontal runs exceed
5 ft
,
1.5 m
they must be supported at
3 ft
,
0.9 m
intervals with
overhead hangers. Use a single wall stainless or single
wall galvanized steel vent pipe the same diameter as
the flue collar to connect the boiler to a masonry
chimney. When using an approved metal chimney
system use the appropriate vent connector. The vent
connector should be sloped up toward the chimney at a
minimum rate of
1/4 in/ft
,
2 cm/m
. On masonr y
chimneys the connector must terminate fl ush with the
inside of the chimney fl ue. Fasten each single wall vent
connection with at least 3 corrosion resistant sheet
metal screws.
The vent materials used in positive pressure vent
systems must be certifi ed to UL 1738 for installations in
the United States, ULS636 for installations in Canada.
The following manufactures have systems that meet
these requirements:
Heat-Fab, Inc.
38 Hayward Street
Greenfi eld, MA 01301, (800) 772-0739.
Z-Flex U.S., Inc.
20 Commerce Park
North, Bedford, NH 03110-6911, (800) 654-5600.
Protech Systems Inc.
26 Gansevoort Street
Albany, NY 12202 (518) 463-7284
WARNING: Breeching under positive pressure
must be certifi ed to UL 1738 for installations
in the United States, ULS636 for installations
in Canada. Type B1 vent SHALL NOT be used.
Failure to comply with this warning can result
in severe personal injury or death.
Always provide a minimum clearance of 6 in. between
single wall metal vent pipe and all combustible materials.