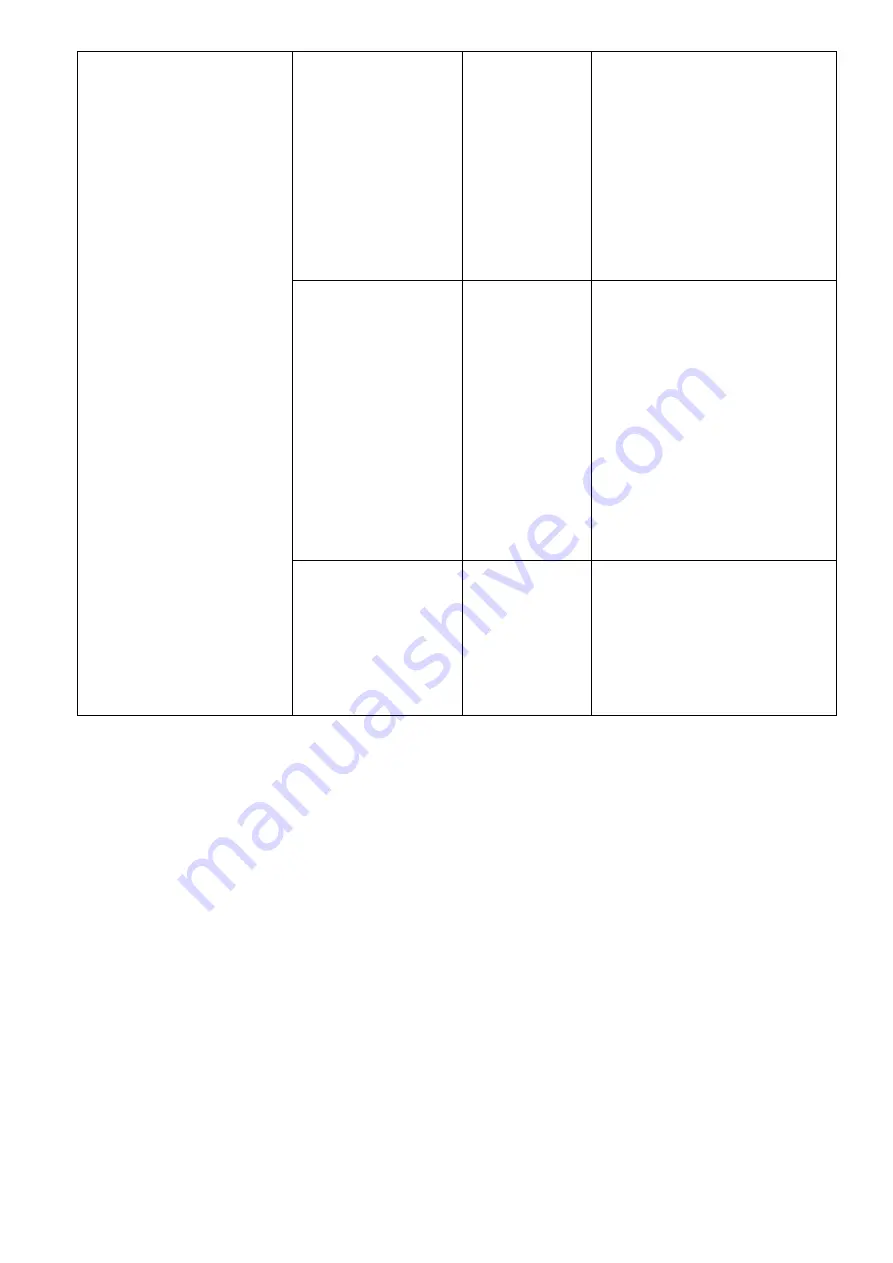
- 23 -
Large overrun. (Stopping
accuracy is low)
Sudden extension of the
rod when the lock is
released.
a. The circuit is not
balanced.
b. Regulator for
balancing pressure
is not adjusted.
c. Line pressure
fluctuates.
d. After stopping
by locking, it is too
fast to unlock.
Change to recommended balanced
circuit. (Refer to Page 13 to 14)
b. Adjust the regulator valve. Check
if the locked status is balanced.
c. Install an air tank so that pressure
fluctuation does not occur when
supplying air to the lock unit and
cylinder.
d. After stopping by locking, release
the lock after waiting for 0.5sec or
longer.
Cylinder speed changed
a. Misalignment of
the piston rod and
guide.
b. High load rate of
the cylinder.
c. Stopping interval
(pitch) is short.
d. Stopping in the
middle of
cushioning
process or
immediately after
the cushioning
process. (When
air cushion type is
used)
e. Line pressure
fluctuates.
a. Adjust the alignment of the piston
rod and guide or use the floating joint.
b. Use a larger cylinder.
c. Set the stop interval to 40mm or
wider.
d. Change the cylinder to rubber
cushion type.
c. Install an air tank so that pressure
fluctuation does not occur when
supplying air to the lock unit and
cylinder.
Changes in the load.
a. Load varies
continuously due
to rotating
movement.
b. Load varies due
to vertical load.
(Step change)
a. Cylinder with lock is not suitable.
Use the cylinder which use
incompressible fluid such as air-hydro
cylinder.
b. When there is a step like change of
the load, use a multi-stage pressure
regulating valve for balancing
pressure.
Summary of Contents for MWB 100 Series
Page 7: ... 7 Selection graph ...