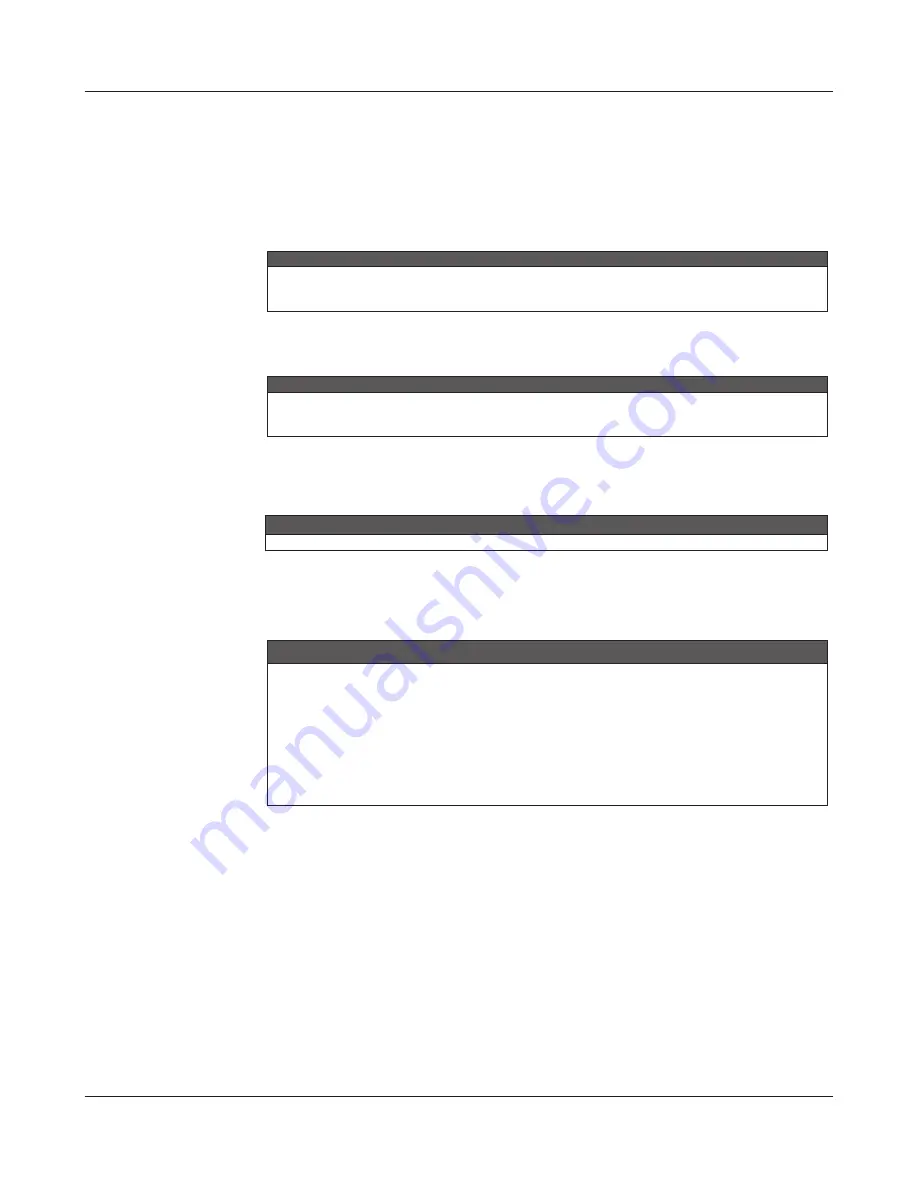
Maintenance Procedures
4.3
Cleaning should be done carefully in order to avoid damaging the delicate isolating diaphragms. Use
of a soft cloth and a non-acid solution is recommended. The oscillating circuit is a part of the sensor
and the replacement of one implies replacing the other.
To remove the sensor from the electronic housing, the electrical connections (in the field terminal
side) and the main board connector must be disconnected.
Loosen the hex screw (
20
) and carefully unscrew the electronic housing from the sensor, observing
that the flat cable is not excessively twisted.
WARNING
To avoid damage do not rotate the electronic housing more than 270º starting from the fully
threaded without disconnecting the electronic circuit from the sensor and from the power supply.
See Figure 4.1.
Electronic Circuit
To remove the circuit board (
5
), loosen the two screws (
3
) that anchor the board.
WARNING
The board has CMOS components, which may be damaged by electrostatic discharges. Observe
correct procedures for handling CMOS components. It is also recommended to store the circuit
boards in electrostatic-proof cases.
Pull the main board out of the housing and disconnect the power supply and the sensor connectors.
Reassemble Procedure
WARNING
Do not assemble the main board with power on.
Sensor Mounting
When mounting the sensor (
19
), it is recommended to make use of a new set of gaskets (
18
&
24
)
compatible with the process fluid. The bolts, nuts, flanges and other parts should be inspected for
corrosion or other eventual damage. Damaged parts should be replaced.
NOTE
Backup Rings
High pressure transmitters A5, M5, M6 and High static pressure transmitters H2, H3, H4, H5 and
the sensors with tantalum diaphragm that use Buna-N or Viton O’Ring must use a metallic
backup Ring (17) to prevent extrusion of O’Ring. Do not use the backup O'Ring when the flange
has an insert of Kynar (PVDF).
Avoid bending the backup ring and inspect it for knots, cuts etc. Be careful when mounting it.
The flat side, which shines more than the bevelled side should be mounted against the O’Ring.
(See Figure 4.2 - Backup Ring Mounting).
Gaskets should be lightly lubricated with silicone oil before they are fitted into their recesses. Use
halogen grease for inert fill applications. The flanges should then be positioned in order to press
them in place. With the flanges holding the O-Rings in place, insert the four bolts (
16
) and tighten
the nuts (
23
) finger tight, making sure the flanges remain parallel all the time.
x
Tighten one nut till the flange seats.
x
Tighten the nut diagonally across with a torque of 2.75 ±0.25 kgf.m.
x
Tighten the first nut with the same torque.
x
Verify the flange alignment.
x
Check torque on the four bolts.
If adapters (
25
) have been removed, it is recommended to replace gaskets (
24
) and to connect the
adapters to the process flanges before coupling them to the sensor. Optimum torque is 2.75 ±0.25
Kgf.m.
The fitting of the sensor must be done with the main board out of the electronic housing. Mount the
sensor to the housing turning clockwise until it stops. Then turn it counterclockwise until it faces the
protective cover (
1
) parallel to the process flange. Tighten the hex screw (
20
) to lock the housing to
the sensor.
Summary of Contents for LD303
Page 1: ...Profibus PA Pressure Transmitter L D 3 0 3 M E...
Page 8: ...LD303 Operation and Maintenance Instruction Manual VIII...
Page 22: ...LD303 Operation and Maintenance Instruction Manual 1 14...
Page 26: ...LD303 Operation and Maintenance Instruction Manual 2 4...
Page 74: ...LD303 Operation and Maintenance Instruction Manual 4 6 Figure 4 4 Exploded View...
Page 83: ...Maintenance Procedures 4 15 Figure 4 8 TPE Software Screen...
Page 102: ...LD303 Certifications Information A 4 CSA NEMKO and EXAM CEPEL NEPSI...
Page 104: ...LD303 Certifications Information A 6 CEPEL...
Page 105: ...Appendix A A 7 Control Drawing Factory Mutual FM...
Page 106: ...LD303 Certifications Information A 8...
Page 108: ...LD303 Operation and Maintenance Instruction Manual B 2...