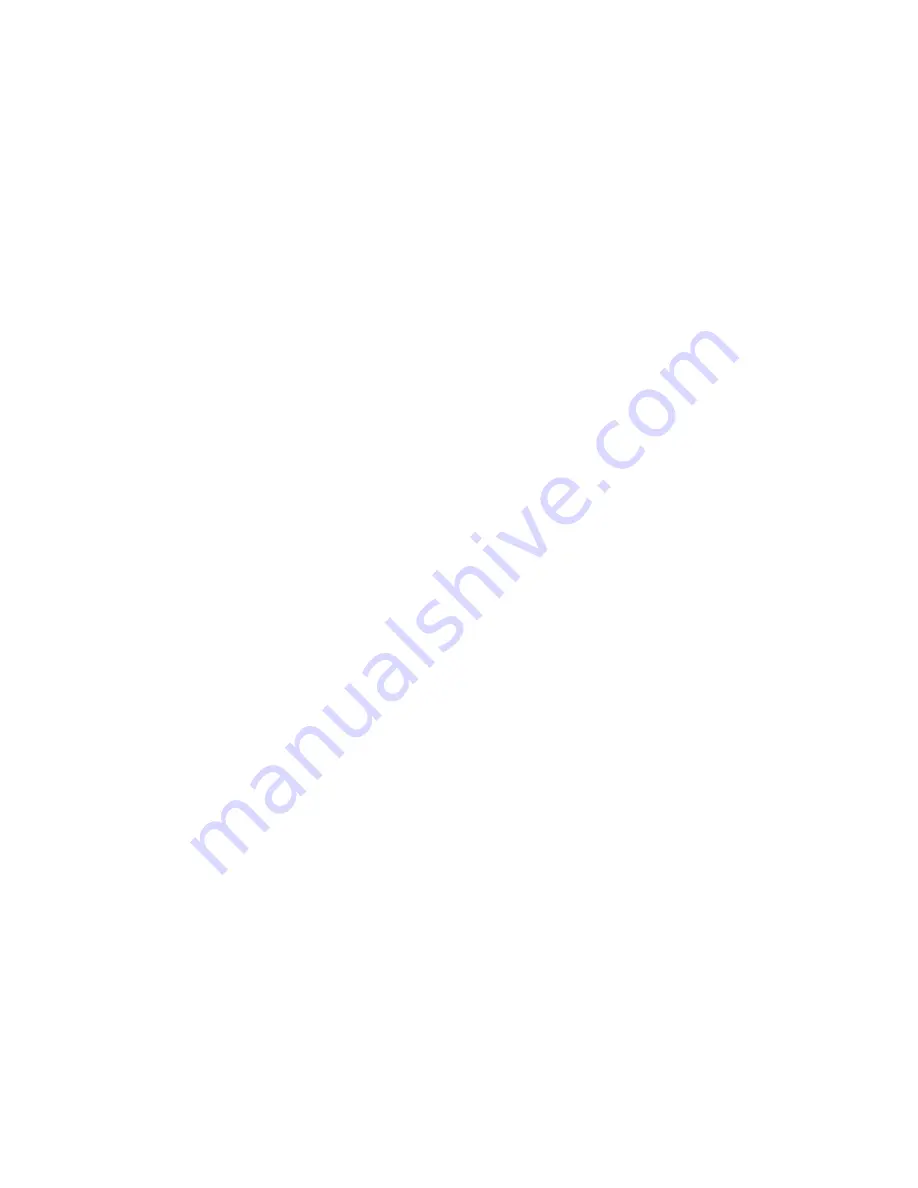
SMAC
LAC-26 Technical Reference Manual
4/29/2013 65
drive interpolates between command points, defining the rate by dividing the change in command by the
interpolation time period. This allows the drive to respond smoothly to each step in command.
Cyclic Synchronous Current In Cyclic Synchronous Current Mode, the drive closes the current loop. The
host is allowed more control by having the ability to instantly add current feedforward values. This allows
for gain compensation in applications with varying loads.
Cyclic Synchronous Velocity In Cyclic Synchronous Velocity Mode, the drive closes two control loops:
velocity and current. The host is allowed more control by having the ability to instantly add velocity and
current feedforward values. This allows for gain compensation in applications with varying loads.
Cyclic Synchronous Position In Cyclic Synchronous Position Mode, the drive closes three control loops:
position, velocity, and current. The host can send target position, velocity feedforward, and current
feedforward values to the drive. This allows for gain compensation in applications with varying loads.
5.2.5 Feedback Supported
There are a number of different feedback options available in the DZ family of digital drives. The feedback
element must be capable of generating a voltage signal proportional to current, velocity, position, or any
parameter of interest. Such signals can be provided directly by a potentiometer or indirectly by other
feedback devices such as Hall Sensors or Encoders. These latter devices must have their signals
converted to a DC voltage, a task performed by the DZ drive circuitry and configuration software.
5.2.6 Feedback Polarity
The feedback element must be connected for negative feedback. This will cause a difference between the
command signal and the feedback signal, called the error signal. The drive compares the feedback signal
to the command signal to produce the required output to the load by continually reducing the error signal to
zero. For DZ drives, this becomes important when using “Encoder Feedback” and “Hall Sensors”, as
connecting these feedback elements for positive feedback will lead to a motor "run- away" condition. In a
case where the feedback lines are connected to the drive with the wrong polarity, the drive will attempt to
correct the "error signal" by applying more command to the motor. With the wrong feedback polarity, this
will result in a positive feedback run- away condition. To correct this, either change the order that the
feedback lines are connected to the drive, or use DriveWare to reverse the internal velocity feedback
polarity setting. The AutoCommutation routine in DriveWare will typically determine the proper feedback
polarity setting.
5.2.7 Hall Sensors
DZ drives can use single-ended Hall Sensors for commutation and/or velocity control. The Hall Sensors
(typically three) are built into the motor to detect the position of the rotor magnetic field. With Hall Sensors
being used as the feedback element, the input command voltage controls the motor velocity, with the Hall
Sensor frequency closing the velocity loop. The Hall Sensor frequency is converted into velocity feedback
that the drive uses to control the motor speed and direction. The actual motor speed can be monitored in
DriveWare through the digital oscilloscope function.
Due to the inherent low resolution of motor mounted Hall Sensors, using Hall Sensors for velocity feedback
is not recommended for low-speed applications below 300 rpm for a 6-pole motor, 600 rpm for a 4-pole
motor, or 900 rpm for a 2-pole motor. Hall Velocity Mode is better suited
Note for velocity control applications where the motor will be spinning at higher speeds.