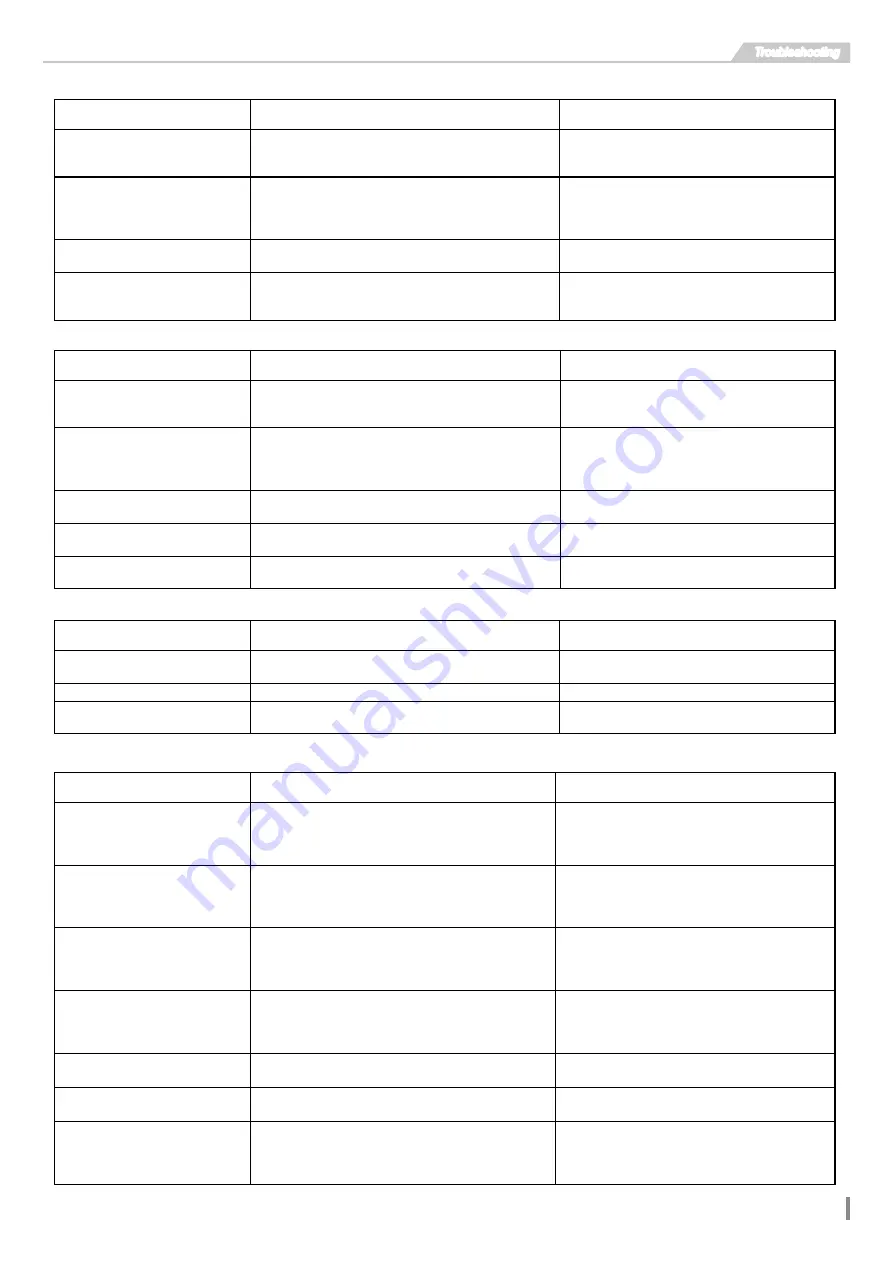
77
Troubleshooting
4. ODU Fan Motor Can't Operate
Possible Causes
Discriminating Method (Air conditioner Status)
Troubleshooting
Wrong wire connection, or poor
connection
Check the wiring status according to circuit
diagram
Connect wires according to wiring diagram to
make sure all wiring terminals are connected
firml
Capacity of the ODU fan motor
is damaged
Measure the capacity of fan capacitor with an
universal meter and fnd that the capacity is out of
the deviation range indicated on the nameplate of
fan capacitor.
Replace the capacity of fan
Power voltage is a little low or
high
Use universal meter to measure the power supply
voltage. The voltage is a little high or low
Suggest to equip with voltage regulator
Motor of outdoor unit is
damaged
When unit is on, cooling/heating performance is
bad and ODU compressor generates a lot of noise
and heat.
Change compressor oil and refrigerant. If no
better, replace the compressor with a new
one
5. Compressor Can't Operate
Possible Causes
Discriminating Method (Air conditioner Status)
Troubleshooting
Wrong wire connection, or poor
connection
Check the wiring status according to circuit
diagram
Connect wires according to wiring diagram to
make sure all wiring terminals are connected
firml
Capacity of compressor is
damaged
Measure the capacity of fan capacitor with an
universal meter and fnd that the capacity is out of
the deviation range indicated on the nameplate of
fan capacitor.
Replace the compressor capacitor
Power voltage is a little low or
high
Use universal meter to measure the power supply
voltage. The voltage is a little high or low
Suggest to equip with voltage regulator
Coil of compressor is burnt out Use universal meter to measure the resistance
between compressor terminals and it's 0
Repair or replace compressor
Cylinder of compressor is
blocked
Compressor can't operate
Repair or replace compressor
6. Air Conditioner is Leaking
Possible Causes
Discriminating Method (Air conditioner Status)
Troubleshooting
Drain pipe is blocked
Water leaking from indoor unit
Eliminate the foreign objects inside the drain
pipe
Drain pipe is broken
Water leaking from drain pipe
Replace drain pipe
Wrapping is not tight
Water leaking from the pipe connection place of
indoor unit
Wrap it again and bundle it tightly
7. Abnormal Sound and Vibration
Possible Causes
Discriminating Method (Air conditioner Status)
Troubleshooting
When turn on or turn off the unit,
the panel and other parts will
expand and there's abnormal
sound
There's the sound of "PAPA"
Normal phenomenon. Abnormal sound will
disappear after a few minutes.
When turn on or turn off the
unit, there's abnormal sound
due to flow of refrigerant inside
airconditioner
Water-running sound can be heard
Normal phenomenon. Abnormal sound will
disappear after a few minutes.
Foreign objects inside the
indoor unit or there're parts
touching together inside the
indoor unit
There's abnormal sound fro indoor unit
Remove foreign objects. Adjust all parts'
position of indoor unit, tighten screws and
stick damping plaster between connected
parts
Foreign objects inside the
outdoor unit or there're parts
touching together inside the
outdoor unit
There's abnormal sound fro outdoor unit
Remove foreign objects. Adjust all parts'
position of outdoor unit, tighten screws and
stick damping plaster between connected
parts
Short circuit inside the magnetic
coil
During heating, the way valve has abnormal
electromagnetic sound
Replace magnetic coil
Abnormal shake of compressor Outdoor unit gives out abnormal sound
Adjust the support foot mat of compressor,
tighten the bolts
Abnormal sound inside the
compressor
Abnormal sound inside the compressor
If add too much refrigerant during
maintenance, please reduce refrigerant
properly. Replace compressor for other
circumstances.