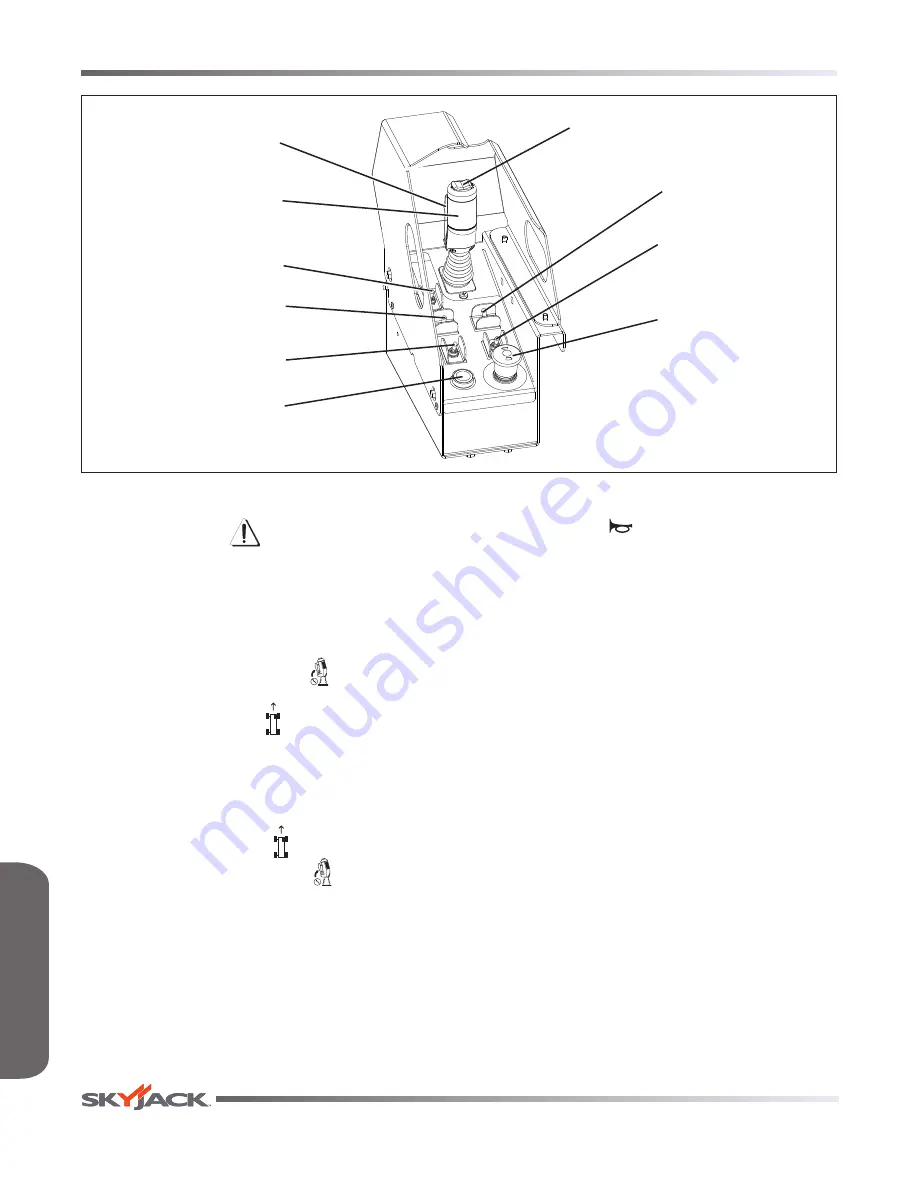
Page 30
December 2007
Rough Terrain Scissors
TM
Function Tests
Section 2 - Familiarization
It is the responsibility of the operator to read, completely understand and follow all instructions and warnings
contained in this operating manual and on the aerial platform.
FAMILIARIZA
TION
FAMILIARIZA
TION
•
Test Brakes
WARNING
Brakes will engage instantly when you
release the controller handle, causing
MEWP to stop immediately.
1. Ensure path of intended motion is clear.
2. Activate and hold “
” enable trigger
switch.
3. Drive MEWP “ ” forward. Test brake by
releasing controller handle.
Result:
MEWP should come to a stop. If
MEWP pulls to one side while stopping, do
not operate MEWP until brake adjustments
have been checked.
4. Drive MEWP “
” forward. Test brake
again by releasing “ ” enable trigger
switch only.
Result:
MEWP should come to an instant
and abrupt stop. If MEWP does not stop
immediately, or if MEWP pulls to one side
while stopping, do not operate MEWP until
brake adjustments have been checked.
•
Test Horn
1. Push “
” horn pushbutton.
Result:
Horn should sound.
Horn Pushbutton
Choke (Dual Fuel)/
Glow Plug (Diesel)
Pushbutton
Engine Start
Switch
Emergency Stop
Button
Torque Switch
Lift/Drive/Steer
Controller
Low/High Throttle
Switch
Rocker Switch
Lift/Drive/Steer Enable
Trigger Switch
Lift/Drive Switch
Summary of Contents for SJ6826 RT
Page 1: ...ROUGH TERRAIN SCISSORS MODELS SJ6826 RT SJ6832 RT 159172AA A December 2013 OPERATING MANUAL AS...
Page 55: ...Rough Terrain Scissors December 2007 Page 55 Notes...
Page 90: ...Page 90 December 2007 Rough Terrain Scissors TM Notes...
Page 91: ......
Page 92: ...www skyjack com P litelig lift l sninger av folk som bryr seg...