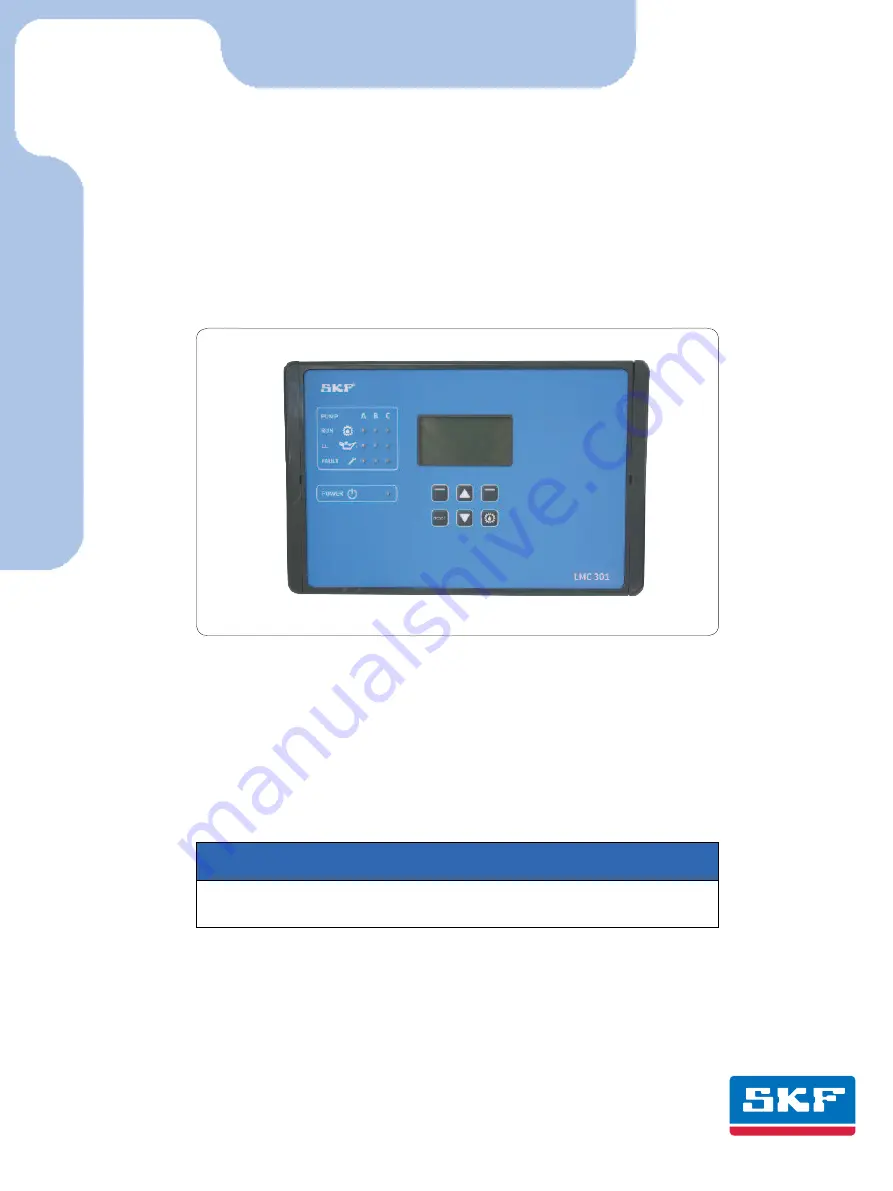
951-150-029-EN
This description is intended as an overview of installation for the LMC 301 Lubrication
Monitor Controller. It does not replace the assembly instructions for the LMC 301 controller.
These are contained on the enclosed USB stick. The assembly instructions can be ordered in
paper format from SKF Lubrication Systems Germany GmbH or Lincoln Industrial, One
Lincoln Way, St. Louis, MO 63120-1578 USA.
In case of discrepancies between the assembly instructions and the Quick Guide, the information
in the assembly instructions takes precedence.
for control of up to three pumps, each with an SKF Single Line / Progressive
and Dual Line centralized lubrication system containing one to three main lines.
Lubrication Monitor Controller
of series LMC 301
Quick Setup/Installation Guide
Version 03
ATTENTION!
The comprehensive assembly instructions (see page 2) are included on the enclosed USB stick
and can be downloaded from our homepage
http://www.skf.com/LMC301/
.