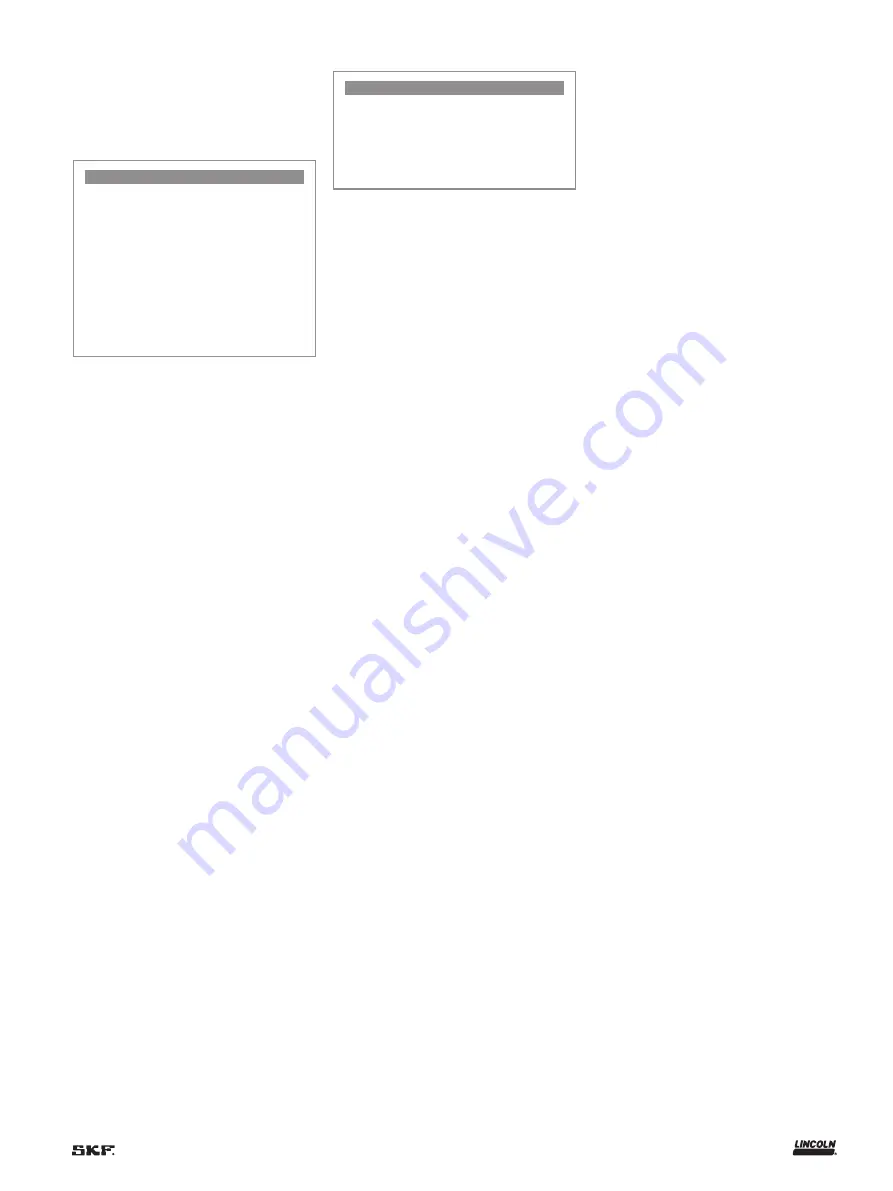
Refill and
maintenance
Pump with follower plate
Use grease fitting (
9
) (
† Fig. 1, page 6
) to fill
or refill reservoir. Make sure no air is trapped
under follower plate. Grease should be in full
contact with surface of follower. It is
recommended to run motor by initiating
lube cycle during first fill of reservoir. Stirring
paddle of running motor will help to evenly
distribute grease under follower minimizing
air pockets. Reservoir has a vent hole (
11
).
Fill grease to maximum follower position
until follower seal will slightly cross vent
hole. If air is still trapped under follower, add
some more grease to expel air through vent
hole.
Pump without follower plate
Use same grease fitting (
9
) to fill or refill
reservoir. It is recommended to run motor by
initiating lube cycle during first fill of
reservoir. Stirring paddle of running motor
will help to evenly distribute grease in
reservoir minimizing air pockets.
To speed up filling or refilling of pump,
grease fitting can be replaced with
1
/
8
in
(3,175 mm)
(swivel connection to
attach hose from larger output filling pump).
Pump cleaning
Use petroleum or benzene based cleaning
solutions. Do not use tri-, perchloroethylene
or similar solvents. Do not use polar organics
such as alcohol, methyl alcohol, acetone or
similar solvents.
CAUTION
First time filling of reservoir with grease is
very critical for proper pump operation.
Pump may be shipped with small amount of
Fuchs Renocal FN 745/Lincoln grease used
for final testing and inspection.
Grease thickener is Ca-12-OH-stearat.
Check compatibility of Renocal FN 745/
Lincoln with grease and remove test grease if
necessary.
Failure to comply may result in personal
injury or damage to equipment.
CAUTION
Do not exceed maximum fill mark when filling
reservoir with large output fill or refill pump.
Risk of reservoir bursting if overfilled.
Failure to comply may result in personal
injury or damage to equipment.
43
Summary of Contents for Lincoln P653S
Page 47: ...Fig 33 Pump with follower 54 53 52 51 50 49 48 47 46 45 44 41 42 43 47...
Page 50: ...Fig 35 Pump without follower 50 49 48 47 46 45 44 43 42 50...
Page 53: ...This page left intentionally blank 53...
Page 54: ...This page left intentionally blank 54...