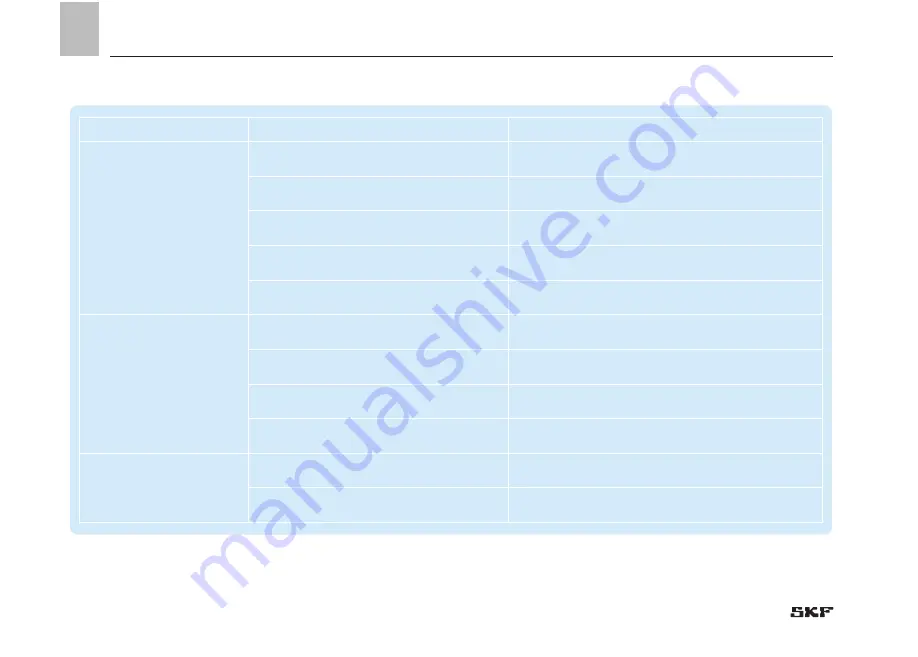
42
EN
11. Faults, causes and remedies
Fault
Cause
Remedy
o No or incomplete lubricant
supply
Lubricating device set to zero flow
• Check the setting and change it if necessary.
Pressure of the feed pump too low
• Check feed pump and pressure setting elements.
Distance of the lubricating head to the lubricating
point to large
• Check installation position.
Pneumatic cylinder
does not push the lubricating
head to the lubricating point
• Check function of the pneumatic cylinder and direction
control valve. Check pipes and mechanical connections.
Lubricating head pushes the chain too far away
• Lead chain.
o Driver does not extend
No signal from proximity switch
• Check proximity switch and replace if necessary.
Direction control valve does not switch
• Check
directional control valve
and replace if necessary.
Pneumatic cylinder does not extend
• Check
pneumatic cylinder
and replace if necessary.
No compressed air supply
• Check
compressed air supply and pipes
and, if
necessary, rectify fault.
o Driver does not drive on time
before each chain roller in
the feed area of the transport
chain
Movement too slow
• Check
inlet air pressure
and correct if necessary (see
chapter “Technical details” on page 21).
Position of the proximity switch defective
• Adjust the position of the proximity switch.
Summary of Contents for Lincoln COBRA 1X-R2
Page 51: ...Notes...