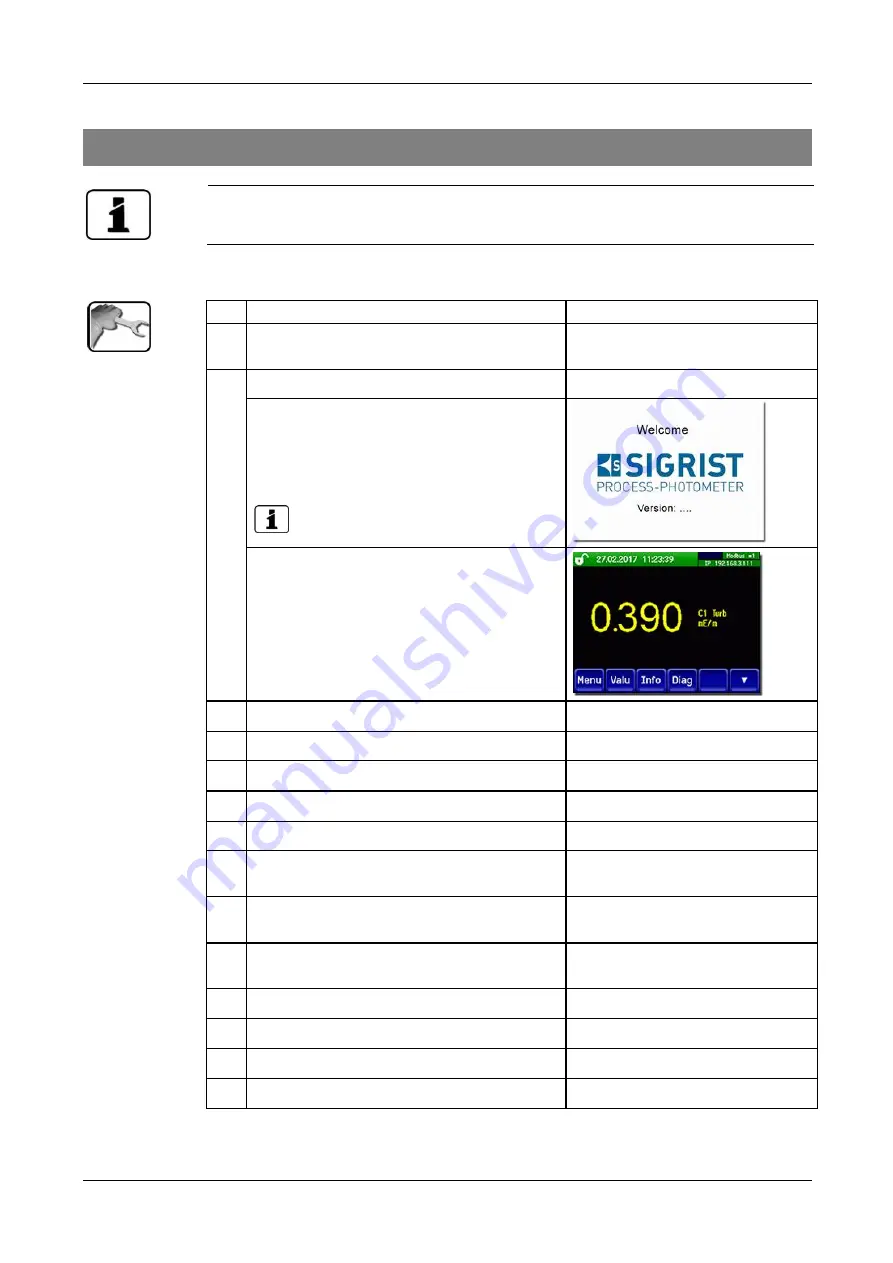
Instruction Manual VisGuard 2
Commissioning
54
14162E/2
6
Commissioning
The initial start-up of the web user interface is described in the Reference Manual.
Proceed with the initial start-up in accordance with the following table:
WORKSTEP
ADDITIONAL INFO / IMAGES
1.
Ensure that all components are correctly moun-
ted and connected.
2.
2.1: Establish the service voltage.
On installations with SIPORT 2:
2.2: Plug the SICON-C into the SIPORT 2 ac-
cording toSection 7.3.
Wait until the welcome screen appears in the
display.
The factory setting language is English.
2.3: The instrument is ready for measurement.
3.
Set the language.
Section 8.1
4.
Set the current outputs.
Section 8.3
5.
Set the limits.
Section 8.4
6.
Set the outputs.
Section 8.5
7.
Set the recalibration.
Section 8.6
8.
If an optional Profibus module is present, set
the Profibus parameters.
Section 8.7
9.
If an optional Profinet IO module is present, set
the Profinet parameters.
Section 8.8
10.
If an optional Modbus module is present, set
the Modbus parameters.
Section 8.9
11.
Set the date and time.
Section 8.2
12.
Enter the access code.
Section 8.10
13.
Carry out recalibration.
Section 9.6
14.
Back up the configured data.
Section 8.11