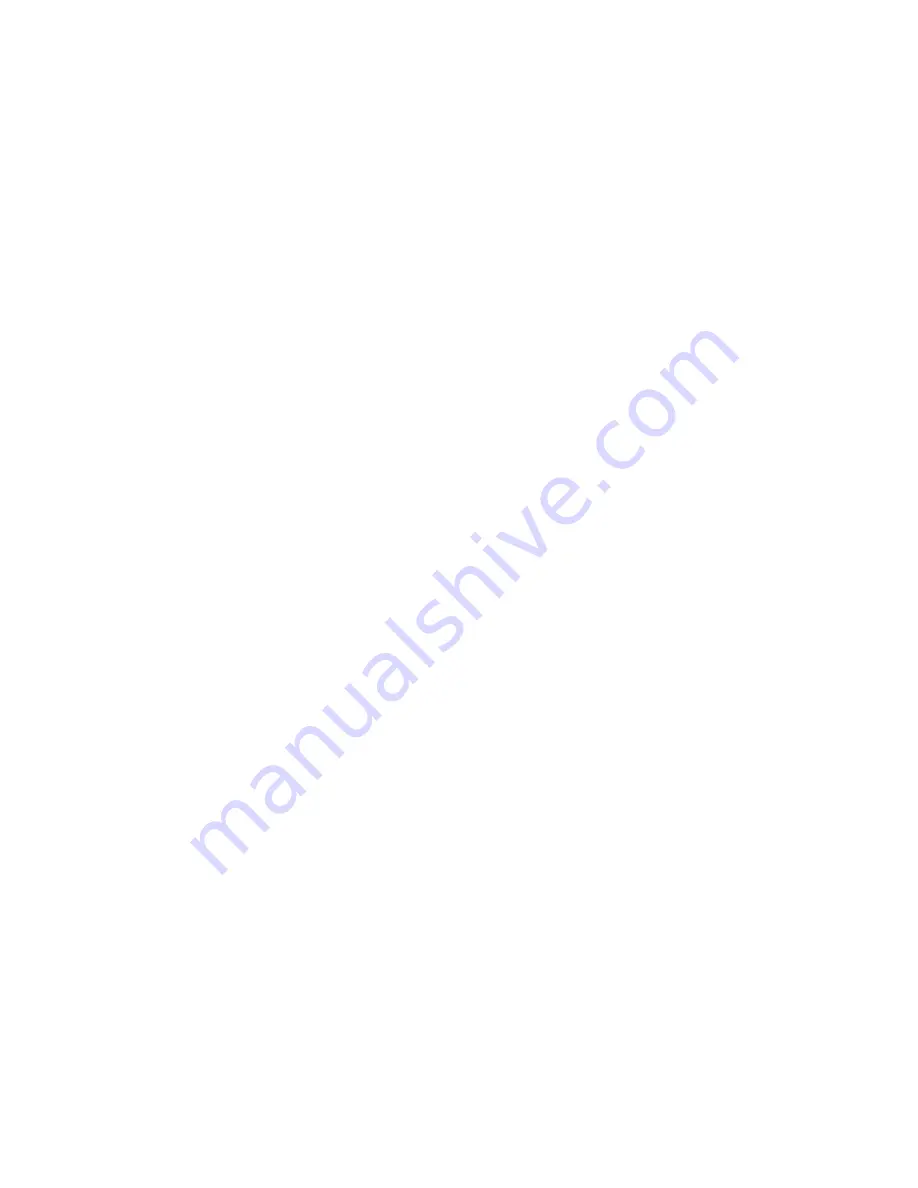
.
66.
a
Assemble the tank per the manufacturers instructions, add carburetor and pressure lines and slide the tank into the fuel
compartment. Blow in the carburetor line and check for free flow of air. It’s much easier to fix any problems before
anything else gets in the way.
b.
Pack around the tank with styrofoam or foam rubber to prevent shifting during flight and to reduce fuel foaming from
vibration.
67
a.
The most convenient way to mount the servos is to use the trays that come with the radio. Follow the radio manufacturers
instructions for mounting the servos, packing the battery and receiver and mounting the switch harness and charge jack.
b.
The servos tray mounted in the fuselage (rudder, elevater and throttle) should be screwed to a pair of mounting rails.
Servo mounting rails for the fuselage should be cut from the 3/8” x 3/8” basswood provided. The location of the rails
should be established based on the desired balance point of the airplane. The position shown on the plans should be
close for the average weight engine. A heavier or lighter engine or tail surfaces may require shifting the rails fore or aft to
help balance the airplane.
c.
The aileron servo can be mounted directly to the center of the lower wing with or without the tray.
d.
The switch harness and charge jack can be mounted in the cockpit area for easy access but will still be protected from the
engine exhaust.
e.
Don’t worry about the location of the receiver or battery pack until we do the final assembly of the airplane.
68
a.
Trim the servo end of the outer pushrod for the elevator (pushrod closest to the bottom of the elevator) so that it extends
forward beyond former F5 about 2".
b.
Make up the control surface end of the elevator inner pushrod first. Cut one of 2-56 threaded steel rods to 3-1/4”. Slide the
plain end of the threaded rod into one end of a 13/64" outside diameter (inner part) nylon tube and screw the threaded
section of the rod about 3/16” into the nylon tube. Wick some thin CA down the threads of the rod into the tube to lock the
threaded rod in place. Thread a nylon clevis on the exposed end of the threaded rod until the threads are through the
clevis.
c.
Tape the elevators firmly in the neutral position and install an inner pushrod assembly in the outer tube closest to the
bottom of the stabilizer. Using the plan and the pushrod assembly as guides mark the location of the two holes for bolting
on the elevator horn. Drill a 3/32" hole at each mark. ‘Harden’ the hole with thin CA and after the glue has cured redrill the
hole. Bolt the elevator horn in place with two #2 x 3/4" sheet metal screws and clip the clevis to the horn. Operate the
elevator by moving the servo end of the pushrod to check for easy, slop-free motion of the elevator. Correct any binding
or excess slop before proceeding to the next step.
d.
Re-tape the elevators firmly in the neutral position. Cut off the inner pushrod tube about 1-1/4" from the elevator servo
arm. Take the shortned 2-56 threaded rod and screw the threads completely into the servo end of the elevator pushrod.
Slide a 2-56 solder link onto the wire pushrod, line the linkpin up with an outer hole in the servo arm, mark the correct
length of the wire pushrod and cut off the wire. Solder the link to the wire.
69.
Repeat step 68.a. through 68.d. for the rudder pushrod.
70
a.
Find F-5B pushrod support and place it against Former F-5 above the pushrods. Mark the location where the two
pushrods should go through the support and drill a 9/32" hole at each mark.
b.
Thread the pushrods through the pushrod support and slide the pushrod support against F-5. Tack glue the pushrod
support in place.
c.
Cycle both servos with the radio to make sure that nothing hangs up and that everything operates freely. If everything
operates correctly glue the pushrod support and pushrod outer sheath permanently in place.
71
a.
Locate the servo end of the throttle cable and make up a support out of scrap materials to locate the outer tube in line with
the arm of the servo.
b.
Sweat solder both ends of the 1/16” steel cable for at least 1” to help support the ends that extend past the outer tube.
Slide the cable into the outer tube and check for any binding that may re-sult from too tight a bend. Correct any problems
now.