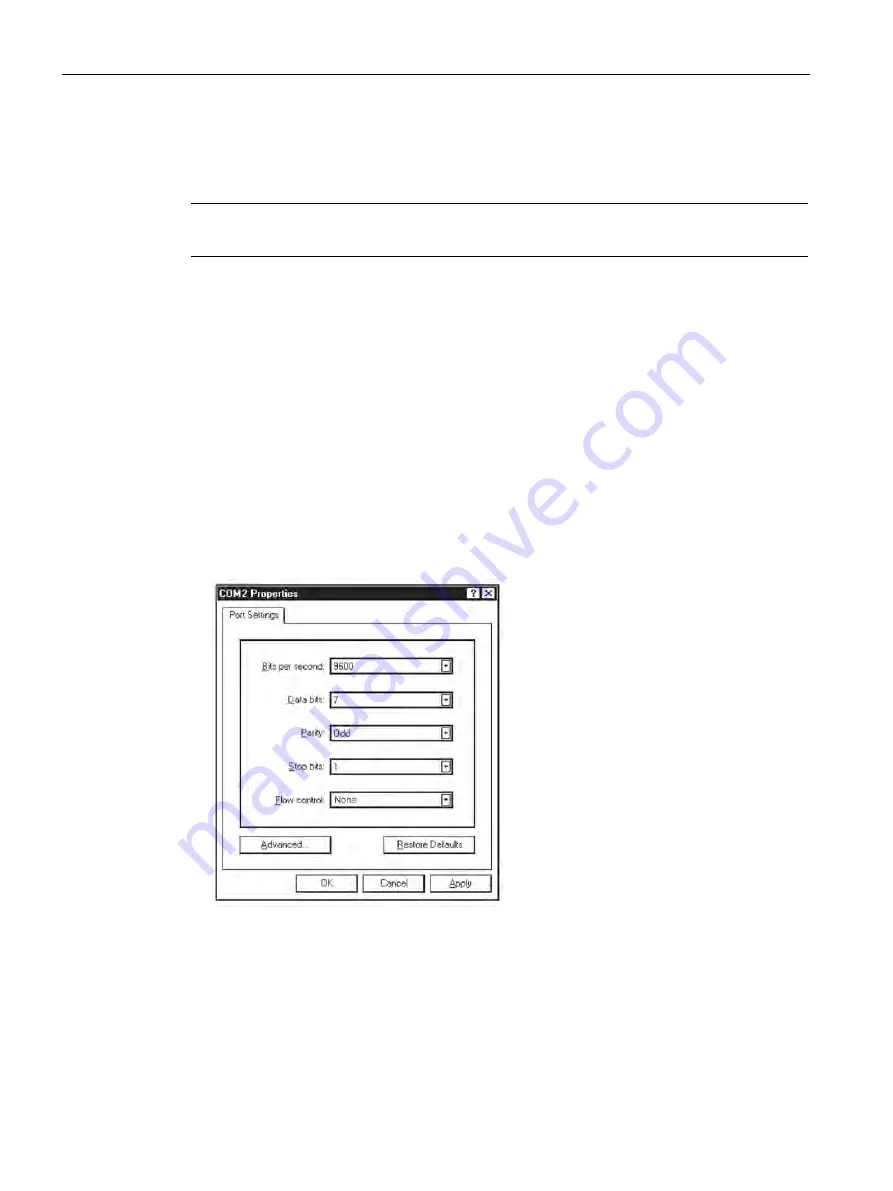
Appendix
A.4 RS-232 Connection
FUE1010 IP65 NEMA 4X
198
Operating Instructions, 12/2014, A5E03086491-AC
Windows provides a communication program called HyperTerminal, which is ideal for
interfacing your computer with the flow meter. The following typical example explains how to
set up HyperTerminal.
Note
Depending upon the Windows applications being used this setup procedure may vary.
1.
From the Windows desktop, left-click on the [START] button.
2.
Holding down the left mouse button, move the highlight up to [Programs], then across to
[Accessories]. Slide the highlight down to [HyperTerminal], then release the left mouse
button.
3.
Within the HyperTerminal window, move the mouse pointer down to [Hyperterm.exe] and
then double-click the left mouse button.
4.
This selects the [Connection Description] dialog box. Enter a name for your connection
(e.g., 1010N). You can optionally select an icon for this connection by clicking on one of
the icons displayed in the scrolling frame at the bottom of the window. Click [OK].
5.
This selects the [Phone Number] dialog box. Move the cursor to the arrow at the right of
the [Connect Using] field. Left click on the arrow to expand the field and then move the
highlight down to [Direct to Com 1 (or 2)] depending on the port connected to the
interface cable. Click [OK] to select the [Com 1 (or 2) Properties] Dialog box. Set up your
RS-232 parameters as shown in the example below. Left-click on the [OK] button.
6.
You will now see a blank terminal screen. Next left-click [File] on the top menu bar. Drag
the highlight down to [Properties] and then left-click.
Summary of Contents for SITRANS 7ME3500
Page 2: ......
Page 213: ......
Page 214: ......
Page 215: ......
Page 216: ......
Page 217: ......
Page 218: ......
Page 219: ......
Page 220: ......
Page 221: ......
Page 222: ......
Page 223: ......
Page 224: ......
Page 225: ......
Page 226: ......
Page 227: ......
Page 228: ......
Page 229: ......
Page 230: ......
Page 231: ......
Page 232: ......
Page 233: ......
Page 234: ......
Page 235: ......
Page 236: ......
Page 237: ......
Page 238: ......
Page 239: ......
Page 240: ......
Page 241: ......
Page 242: ......
Page 243: ......
Page 244: ......
Page 245: ......
Page 246: ......
Page 247: ......
Page 248: ......
Page 249: ......
Page 250: ......
Page 251: ......
Page 252: ......
Page 253: ......
Page 254: ...21614 C 1011NFPS 7 ...
Page 255: ...1011NFPS 7 C 21614 ...
Page 256: ...1011NFPS 7 C 21614 ...
Page 257: ...21614 C 1011NFPS 7 ...
Page 258: ......
Page 259: ......
Page 260: ......
Page 261: ......
Page 262: ......
Page 263: ...21614 C ...
Page 264: ......
Page 265: ......
Page 266: ...1012TN 7 INSTALLATION DRAWING 1010 SERIES TRANSDUCERS AND MOUNTING TRACKS 21614 C ...
Page 267: ...1012TN 7 INSTALLATION DRAWING 1010 SERIES TRANSDUCERS AND MOUNTING TRACKS 21614 C ...
Page 268: ...1012TNH 7 INSTALLATION DRAWING 1010 SERIES TRANSDUCERS AND MOUNTING TRACKS 21614 C ...
Page 269: ...1012TNH 7 INSTALLATION DRAWING 1010 SERIES TRANSDUCERS AND MOUNTING TRACKS 21614 C ...
Page 270: ......
Page 271: ......
Page 272: ......
Page 273: ......
Page 274: ......
Page 275: ......
Page 276: ...21614 C STEP 4 BAND LENGTH TABLE PERMANENT INSTALLATION SERVICE NOTE STEP 2 STEP 3 STEP 1 ...
Page 277: ......
Page 278: ......
Page 279: ......
Page 280: ......
Page 282: ......
Page 290: ...Glossary FUE1010 IP65 NEMA 4X 216 Operating Instructions 12 2014 A5E03086491 AC ...
Page 294: ...Index FUE1010 IP65 NEMA 4X 220 Operating Instructions 12 2014 A5E03086491 AC ...
Page 295: ......