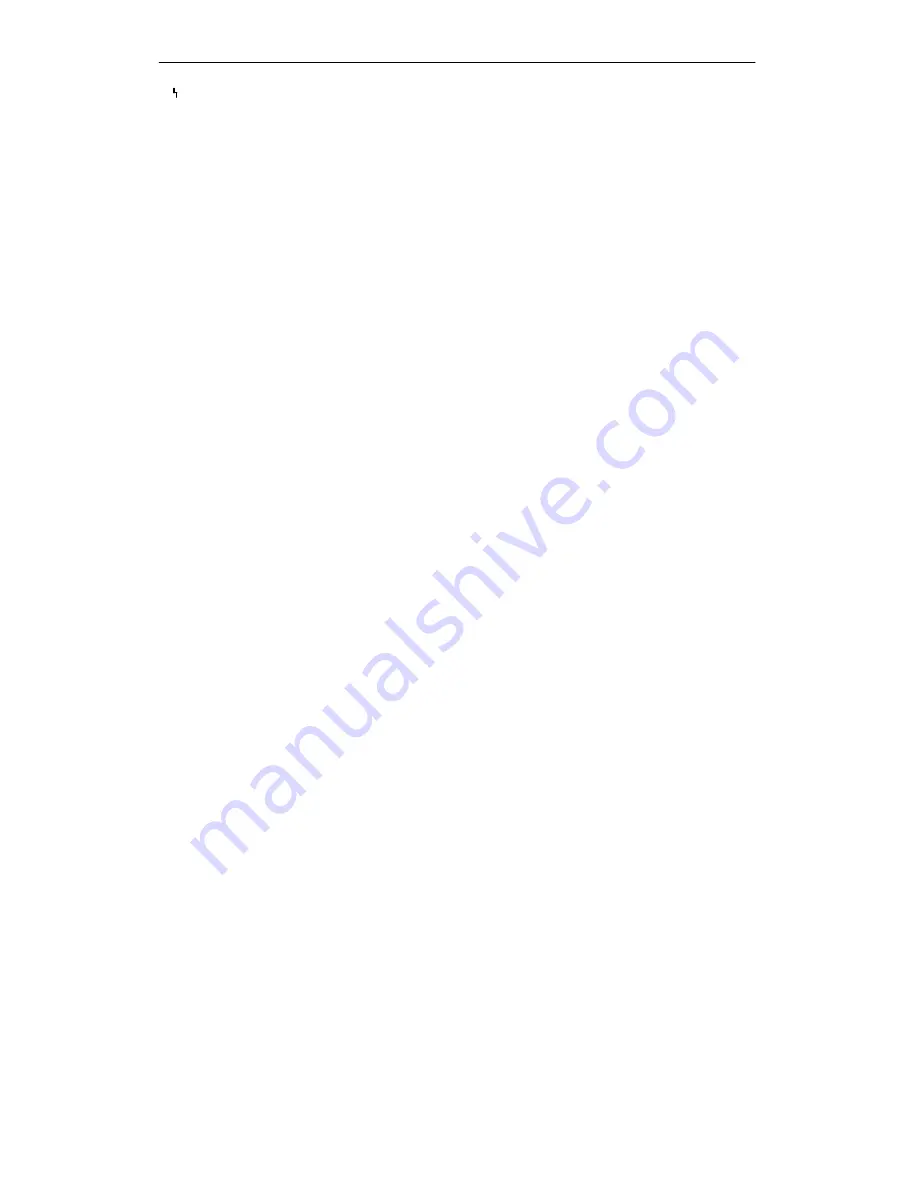
Operation
112
SIPART PS2 Manual
A5E00074631--06
General control valve malfunction
This parameter activates the dynamic monitoring of the control valve
reaction. To do this, the actual position sequence is compared to the
guide value and the expected position sequence, which allows
conclusions with regard to the correct operational behavior of the
control valve.
When the parameter is activated, the submenu for the general control
valve malfunctions from b1 to b5 opens. The function can be
configured there.
Time constant of the low-pass filter
The time constant of the low-pass filter is determined during the
automatic initialization of the device. In the factory setting, parameter
b1 therefore indicates “Auto”.
If the user is very familiar with the process sequence or desires a
certain filter time constant for application-specific reasons, parameter
b1 can be set from one second to 400 seconds manually. One second
causes no damping, 400 seconds result in a strong damping effect.
Limit for the general control valve malfunction
Sets the limit for the deviation from the model behavior. This limit is a
reference value for the error message factors. Factory setting is 1.0 %.
Factor 1
Input of the factor for the threshold 1 error message. This factor refers
to the limit for the general control valve malfunction. Factory setting for
factor 1 is 5.0. That means, for b2.LIMIT = 1.0% and factor 1 = 5.0, the
first error message is triggered at a control deviation of 5.0 % from the
model behavior.
Factor 2
Input of the factor for the threshold 2 error message. This factor refers
to the limit for the general control valve malfunction. Factory setting for
factor 2 is 10.0. That means, for b2.LIMIT = 1.0% and factor 2 = 10.0,
the second error message is triggered at a control deviation of 10.0 %
from the model behavior.
Factor 3
Input of the factor for the threshold 3 error message. This factor refers
to the limit for the general control valve malfunction. Factory setting for
factor 3 is 15.0. That means, for b2.LIMIT = 1.0% and factor 3 = 15.0,
the third error message is triggered at a control deviation of 15 % from
the model behavior.
b. DEVI
b1.TIM
b2.LIMIT
b3.FACT1
b4.FACT2
b5.FACT3
Summary of Contents for SIPART PS2 6DR50 Series
Page 40: ...Design and Functional Principle 40 SIPART PS2 Manual A5E00074631 06 Table 2 1 Scopetuator ...
Page 88: ...Preparing for Operation 88 SIPART PS2 Manual A5E00074631 06 ...
Page 96: ...Operation 96 SIPART PS2 Manual A5E00074631 06 Figure 4 6 Parameter table of the positioner ...
Page 144: ...Operation 144 SIPART PS2 Manual A5E00074631 06 ...
Page 160: ...Appendix 160 SIPART PS2 Manual A5E00074631 06 ...