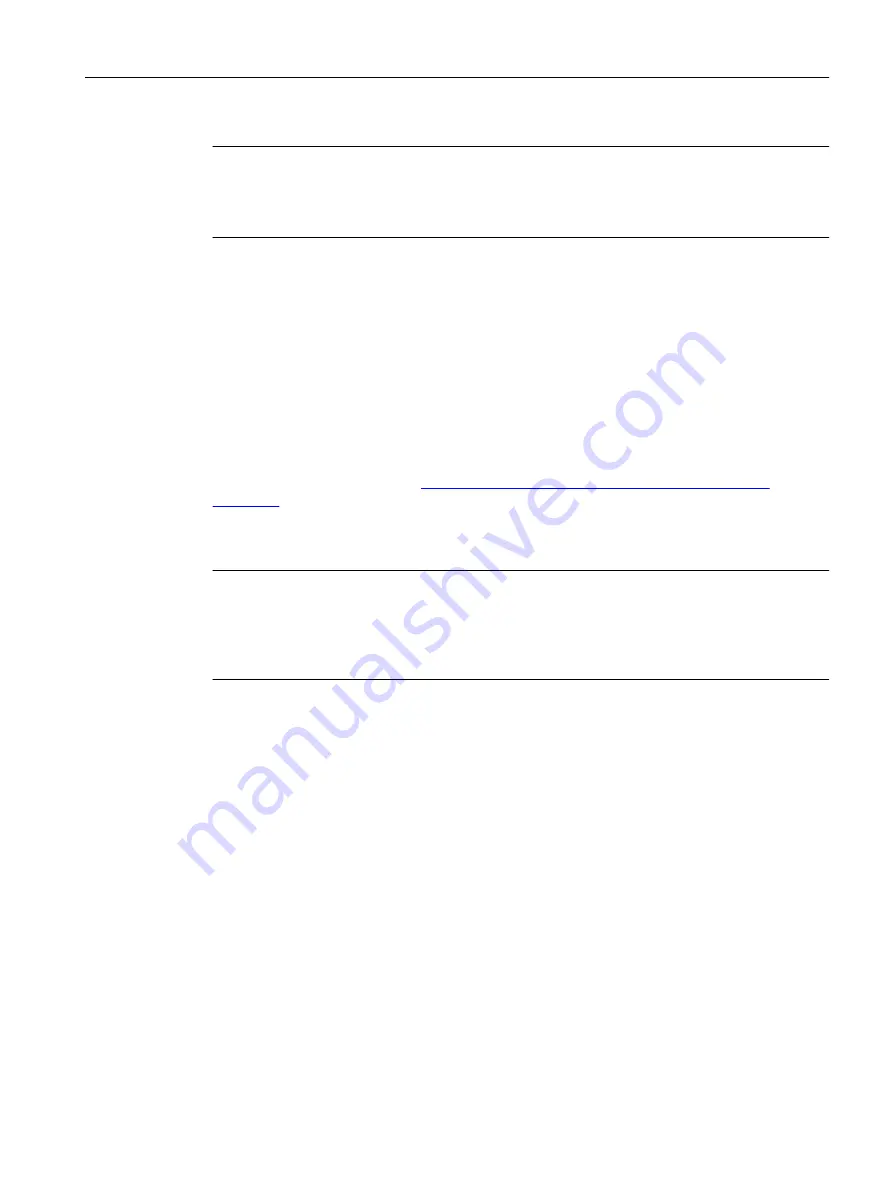
Note
Encoders with integrated DRIVE-CLiQ interface
These encoders must be certified at least according to IEC 61800‑5‑2 (SIL2) or ISO 13849‑1
(Performance Level d / Category 3).
A fault mode effect analysis (FMEA) for securing the encoder on the motor shaft or on the linear
drive must be performed. The result must be that the risk of the encoder mounting loosening is
defined as a fault that can be ruled out (see DIN EN 61800‑5‑2, 2008, Table D.16 ). The
encoder would no longer correctly map the motion if its mounting were to become loose.
It should be noted that the machine manufacturer has sole responsibility for the fulfillment of the
above-described requirements. Information on the internal realization of the encoder must
come from the encoder manufacturer. The FMEA must be created by the machine
manufacturer.
Information about Siemens motors with and without DRIVE-CLiQ connection, which can be
used for Safety Integrated Functions, is available in the SIOS Portal:
Suitable motors and encoders (
https://support.industry.siemens.com/cs/ww/en/view/
).
For these motors, the encoder mounting on the motor shaft can be considered to be safety
relevant, and faults associated with an encoder becoming loose ruled out.
Note
Basic absolute encoders with EnDat interface and additional sin/cos tracks
Basic absolute encoders (e.g. EQI) that offer an EnDat interface with additional sin/cos tracks,
but operate according to an inductive measuring principle internally, are not permitted for
SINAMICS Safety Integrated.
Safety functions integrated in the drive
4.19 Safe actual value acquisition
Safety Integrated (with SINAMICS S120)
Commissioning Manual, 02/2020, A5E46305916B AB
195