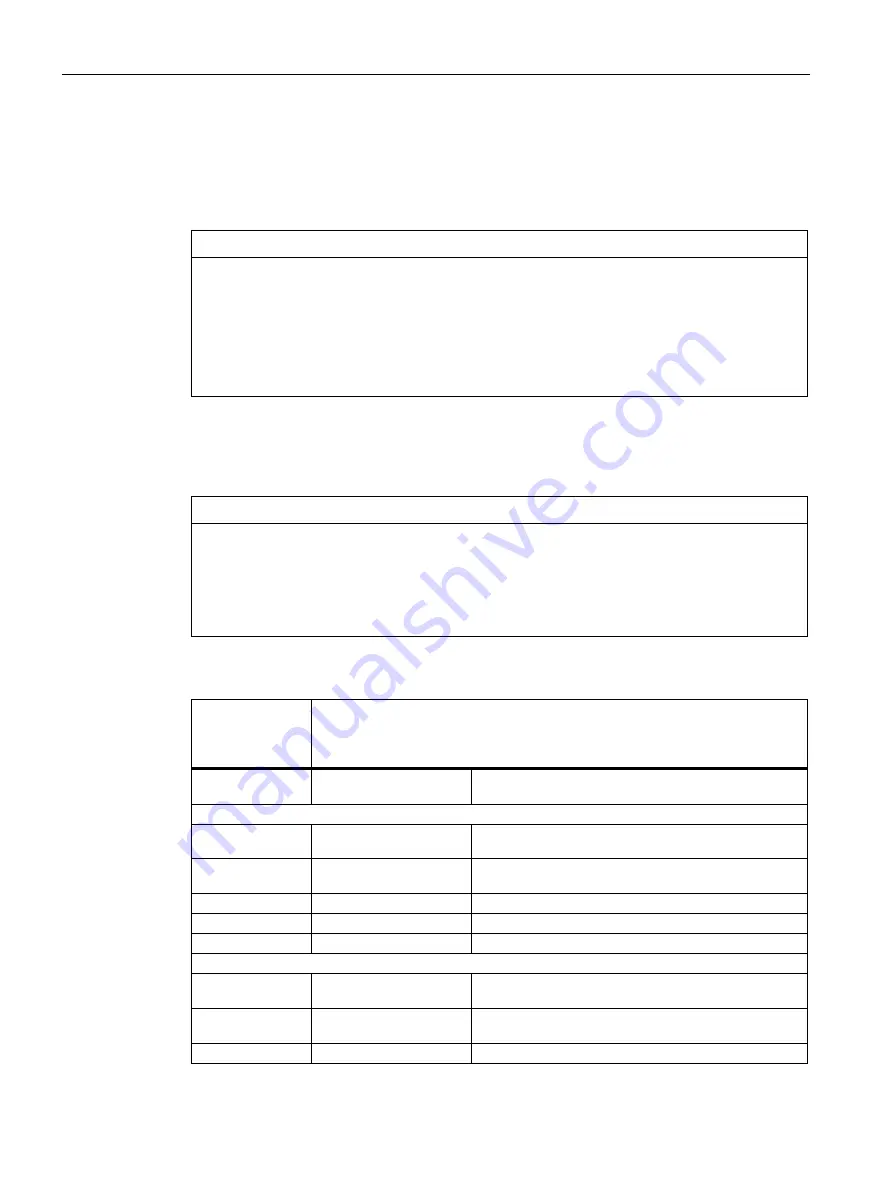
Description of the motors
2.6 Mounting and options
1FK7 G2 synchronous motors
36
Operating Instructions, 05/2021, A5E50907562B AA
Encoder systems without a DRIVE-CLiQ interface
For motors without an integrated DRIVE-CLiQ interface, the analog encoder signal is first
converted to a digital signal in the drive system. For these motors, the encoder signals for
SINAMICS S110 / S120 must be transferred via Sensor Modules.
NOTICE
Damage to components that are sensitive to electrostatic discharge
The contacts of the connector plug have direct contact to components that can be
damaged/destroyed by electrostatic discharge (ESDs).
•
Do not touch the connections directly even with tools that could be electrostatically
charged.
2.6.4.1
Overview of the encoders that can be deployed
NOTICE
Destruction of the encoder when incorrectly handling ESD parts and components
Encoders are ESD components.
•
Carefully comply with the regulations for handling parts and components that can be
destroyed by electrostatic discharge. See Equipment damage due to electric fields or
electrostatic discharge (Page 16)
The following encoders can be used with the 1FK7.
Encoders with DRIVE-CLiQ interface:
For SINAMICS drive systems
Single-turn absolute
encoders
Multiturn absolute encoders
High resolution, suitable for Safety Integrated Extended Functions
Encoder designa-
tion
AS24DQI
AM24DQI
Identification in
the article number
B
C
Resolution
16,777,216 = 24 bits
16,777,216 = 24 bits
Absolute position
Yes, one revolution
Yes, 4096 revolutions (12 bits)
Max. angular error
± 40"
± 40"
Average resolution, suitable for Safety Integrated Extended Functions
Encoder designa-
tion
AS20DQI
AM20DQI
Identification in
the article number
Q
R
Resolution
1,048,576 = 20 bits
1,048,576 = 20 bits