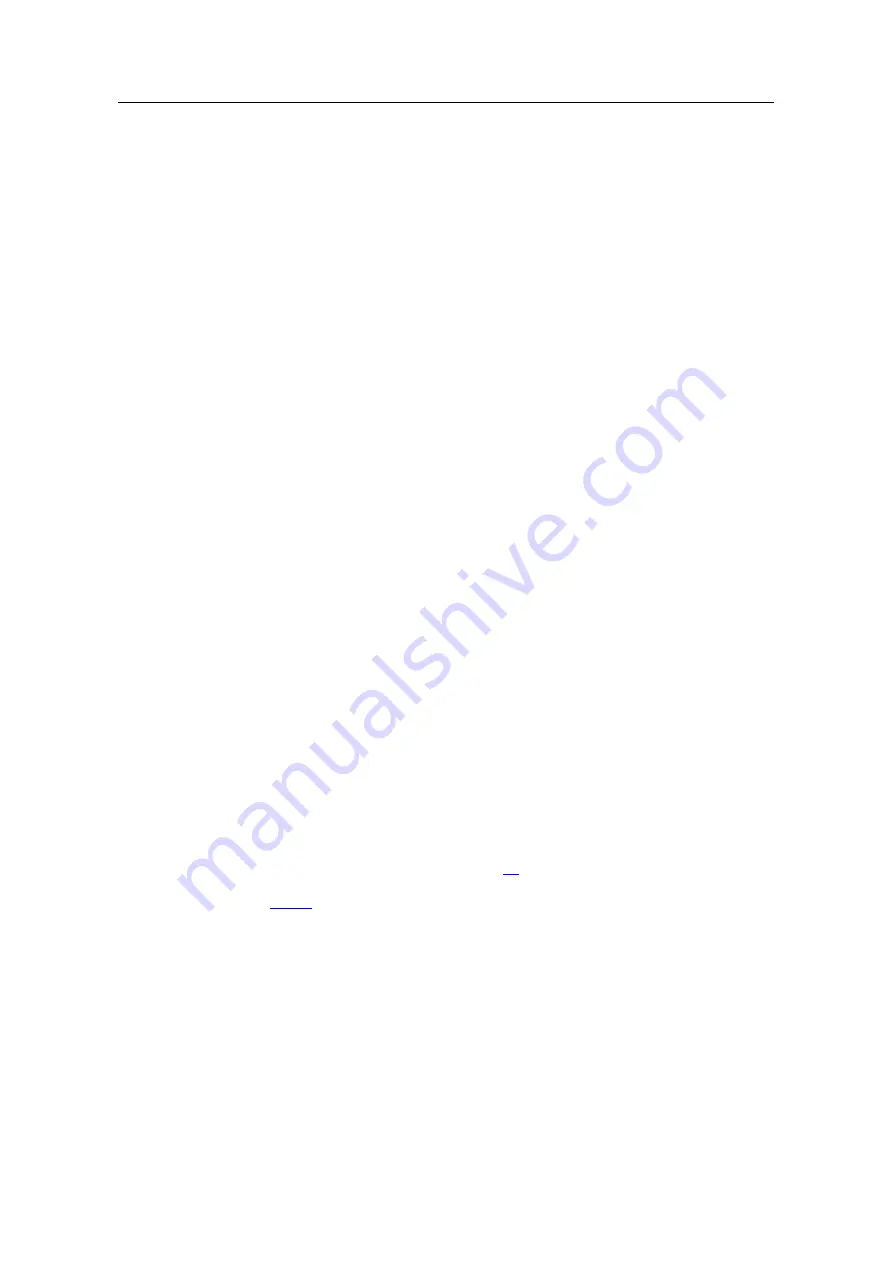
3 Engineering
Blocking Protection for Pumps with SIMOCODE pro V
Article ID: 109478058, V2.0, 09/2020
21
©
S
iem
e
n
s A
G
2020
A
ll r
igh
ts
re
se
rv
e
d
3.1.1
Basic unit (BU)
A SIMOCODE pro V PN motor control device is built into the application example
with a PROFINET interface. However, you can also use basic units with
PROFIBUS interface or MODBUS RTU. The basic parameterization matches a
reversing starter.
3.1.2
Detecting irregularities in the conveying flow
With respect to this application example, the SIMOCODE pro V PN basic unit
extrapolates irregularities in the pump's conveying flow based on the motor current
i
max
and the power factor cos φ. To do this, the associated current/voltage
measuring module taps into the three-phase motor voltage and the three-phase
motor current at the feeder.
3.1.3
Clearing blockages in the conveying flow
Thanks to the wide selection of logic modules implemented in the basic unit (such
as truth tables, counters and timers) that can be interconnected as desired, a logic
has been implemented that briefly reverses the pump drive up to three times if an
irregularity is detected in the conveying flow in order to create a chance for
successful smooth operation. If this succeeds, an impending forced shutdown can
be avoided.
3.1.4
Digital module (DM)
The example allows status signals "ON<", "OFF" and "ON>" to be output at
indicator lamps. Because the SIMOCODE pro V PN basic unit can only provide a
relay output for "ON<", two relay outputs of the digital module are used for "OFF"
and "ON>".
3.1.5
Operator panel (OP)
In the example the motor feeder can also be controlled via the operator panel as a
control station. Additionally, the operator panel can display current measured
values, operational and diagnostic data as well as status information.
3.1.6
Communication with a PLC
The application example can be operated in the absence of communication with a
PLC. However, the default reversing starter interconnections exist for the cyclic
receive and send data (see Getting Started
) so that the drive can be monitored
and controlled with a PLC if communications are appropriately parameterized.
Chapter
describes an additional application-specific data exchange with a
controller. The PROFINET interface of the SIMOCODE device used in the example
project matches the default parameterization and has the IP address 192.168.0.1.