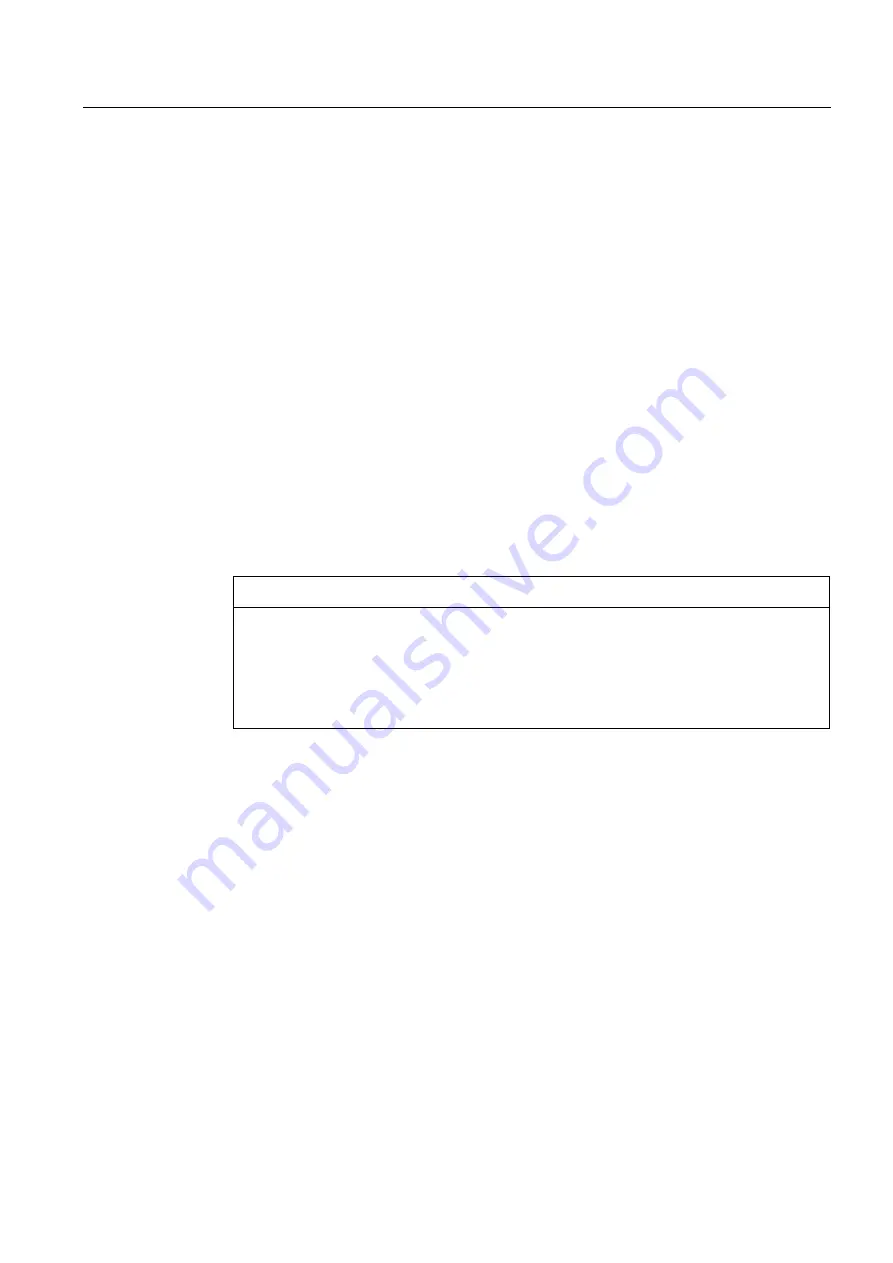
Mounting and connection
4.3 Mounting and connecting the TP 177micro
OP 73micro, TP 177micro (WinCC flexible)
Operating Instructions, 09/2007, 6AV6691-1DF01-0AB0
51
General requirements of equipotential bonding
Potential differences must be reduced by means of equipotential bonding in order to ensure
trouble-free operation of the relevant components of the electronic system. The following
must therefore be observed when installing the equipotential bonding circuit:
●
The effectiveness of equipotential bonding increases as the impedance of the
equipotential bonding conductor decreases or as its cross-section increases.
●
If two system parts are connected to each other via shielded data lines with shielding
connected to the grounding/protective conductor on both sides, the impedance of the
additionally installed equipotential bonding cables may not exceed 10% of the shielding
impedance.
●
The cross-section of a selected equipotential bonding conductor must be capable of
handling the maximum equalizing current. The best results for equipotential bonding
between two cabinets were achieved with a minimum conductor cross-section of 16 mm
2
.
●
Use equipotential bonding conductors made of copper or galvanized steel. Establish a
large-surface contact between the equipotential bonding conductors and the
grounding/protective conductor and protect these from corrosion.
●
Terminate the shielding of the data cable on the HMI device flush and near the
equipotential busbar using suitable cable clamps.
●
Route the equipotential bonding conductor and data cables in parallel with minimum
clearance between these. See the wiring diagram.
NOTICE
Equipotential bonding conductor
Cable shielding is not suitable for equipotential bonding. Always use the prescribed
equipotential bonding conductors. The minimum cross-section of a conductor used for
equipotential bonding is 16 mm². When you install MPI and PROFIBUS DP networks,
always use cables with a sufficient crosssection since otherwise the interface modules
may be damaged or destroyed.