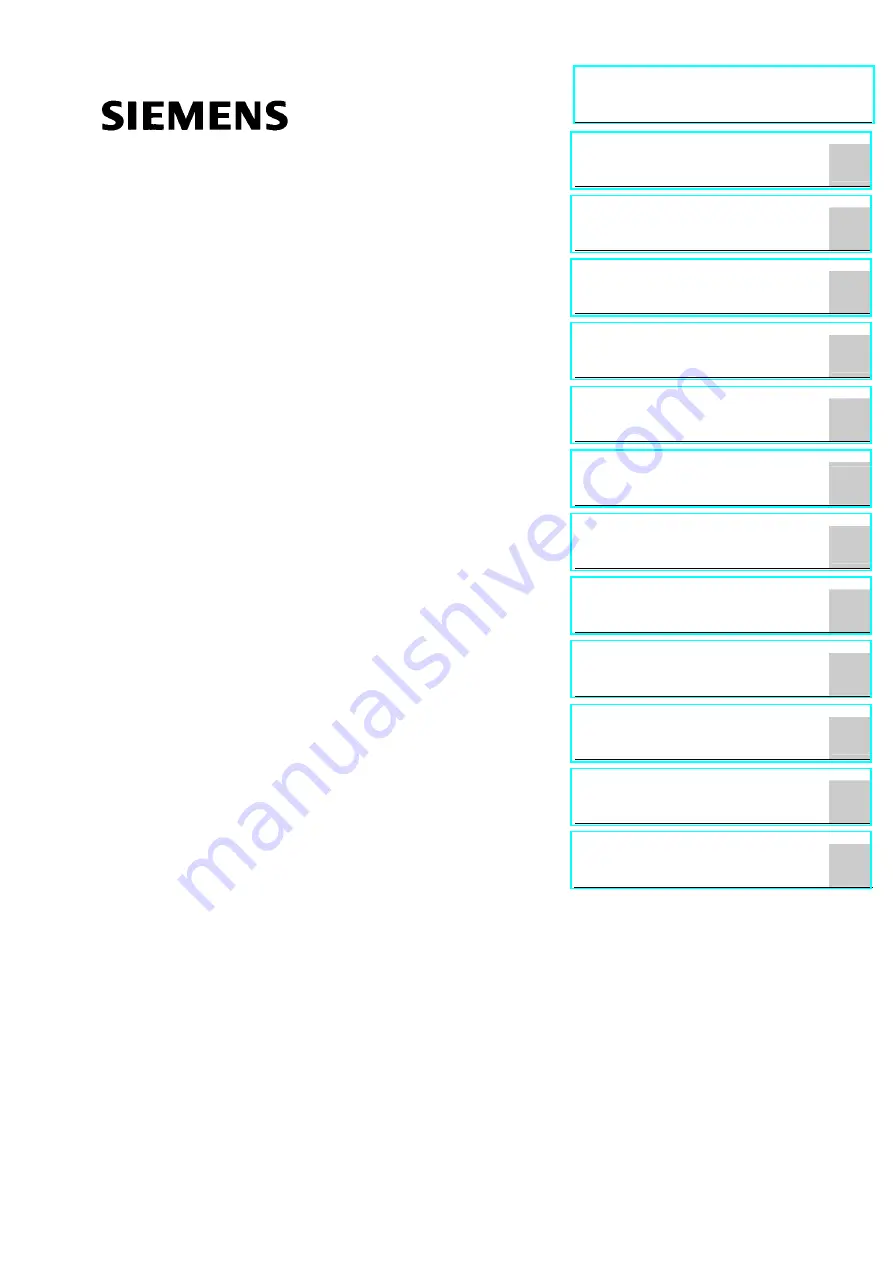
SIMATIC Distributed I/O System Fail-Safe Engineering ET 200S Distributed I/O System - Fail-Safe Modules
______________
______________
______________
______________
______________
______________
______________
______________
______________
______________
______________
______________
SIMATIC
Distributed I/O System Fail-Safe
Engineering
ET 200S Distributed I/O System -
Fail-Safe Modules
Installation and Operating Manual
08/2008
A5E00103686-07