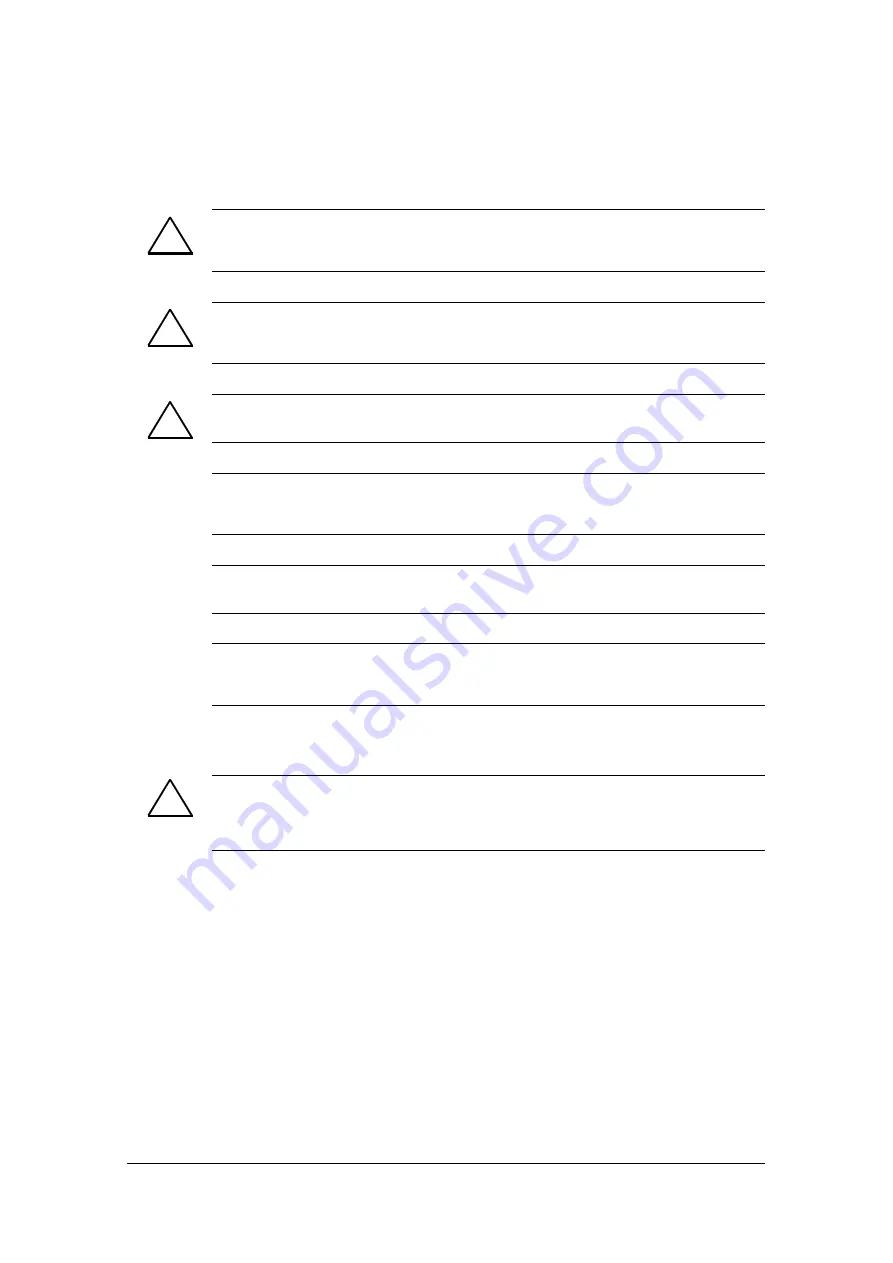
Copyright © Siemens AG 2004 All rights reserved
Disclaimer of liability
Passing on and duplication of this document as well as
utilization and revelation of its contents is not permitted
without express permission. Violators will be prose-
cuted for damages. All rights reserved particularly in
the event a patent is granted or a utility model is regis-
tered. The designations used in this documentation
may be brands whose use by third parties for their own
pur-poses may violate the rights of the owners.
Although we have checked the contents of this publication
for correspondence to the described hardware and soft-
ware, errors cannot be excluded. The information in this
publication is checked at regular intervals and necessary
corrections included in the next edition. You comments and
ideas are welcome. Subject to technical change without
prior notice
Siemens Aktiengesellschaft
(4)J31069-D0427-U001-A2-7618
Technical safety notes
This documentation contains information which you must adhere to for your own personal safety and
for the avoidance of property damage. The information is highlighted with a warning triangle. The de-
gree of danger is presented as shown below.
!
Danger
Means that death, severe injury or substantial property damage will occur if the appropriate precautions
are not taken.
!
Warning
Means that death, severe injury or substantial property damage may occur if the appropriate precau-
tions are not taken.
!
Caution
With a warning triangle: means that minor injury may occur if the appropriate precautions are not taken.
Caution
With no warning triangle: means that property damage may occur if the appropriate precautions are not
taken.
Attention
Means that an undesired result or an undesired state may occur if this information is not adhered to.
Note
Important information on the product, the handling of the product, or the particular part of the documen-
tation which requires special attention.
Intended use
!
Warning
The described product may only be used for the applications stated in this documentation and only in
connection with Siemens components or components and devices of other manufacturers which been
recommended or authorized by Siemens.
Brands
SIMATIC® is a registered brand of Siemens AG.
The other designations used in this publication may be brands whose use by third parties for their own
purposes may violate the rights of the owners.