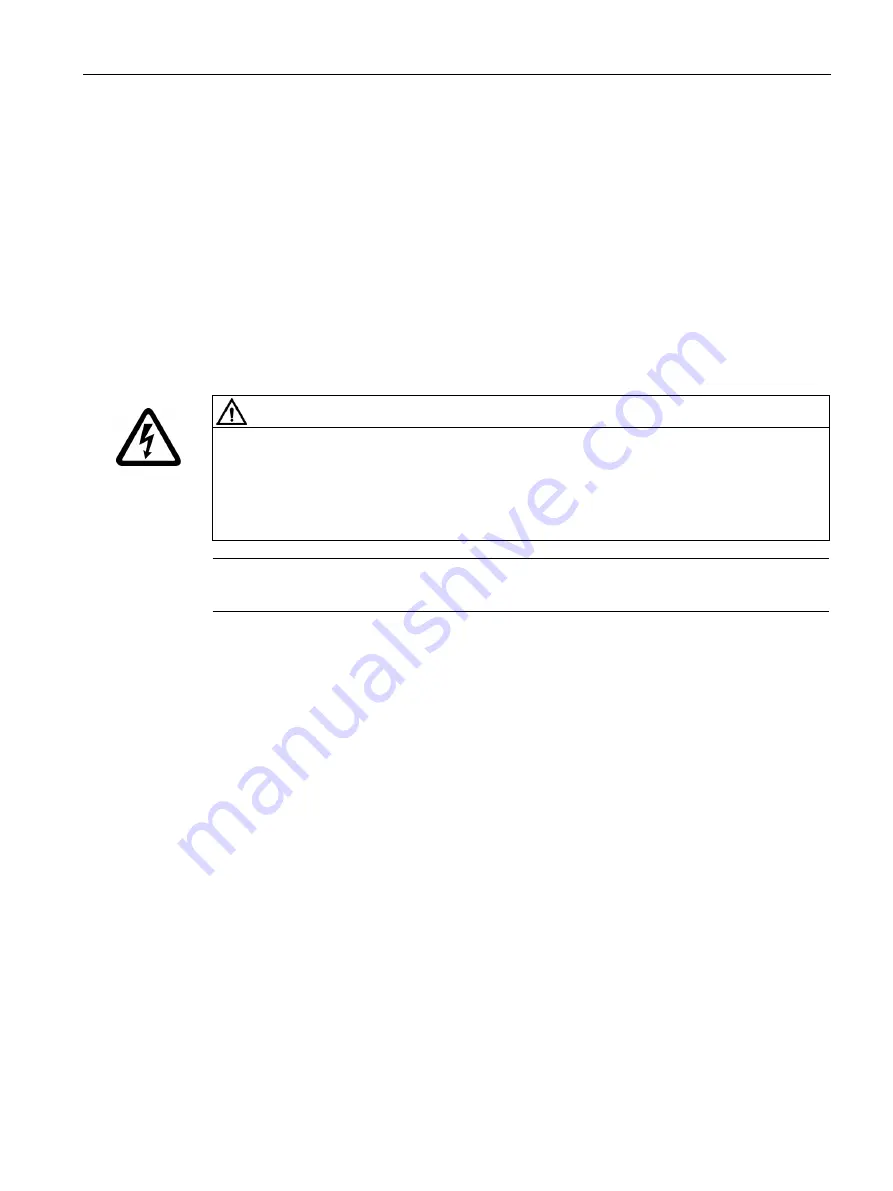
Appendix
A.3 Application examples for functional safety (STO / SS1-t)
Power Module PM330
Hardware Installation Manual, 12/2018, A5E32844552B AF
121
A.3
Application examples for functional safety (STO / SS1-t)
A.3.1
General requirements
Power supply:
The PM330 has an internal 24 V DC supply. This voltage is made available at X9:1/2; an
external 24 V DC supply can also be connected here.
●
The safety relay can be externally supplied with 24 V DC (see example).
●
The safety relay can be supplied via the -X9 interface from the PM330.
WARNING
Hazardous voltage when connecting an unsuitable power supply
Death or serious injury can result when live parts are touched in the event of a fault.
•
Only use power supplies that provide SELV (Safety Extra Low Voltage) or PELV
(Protective Extra Low Voltage) output voltages for all connections and terminals of the
electronics modules.
Note
Together, the loads at X9:1 and X9:8 may be a maximum of 250 mA.
Cable length:
●
Cable length between the safety relay and-X41 / -X9, max. 30 m
Diagnostics of the two switch-off signal paths:
●
Connect both floating contacts of the PM330 into the feedback circuit of the safety relay
Executing a forced checking procedure (test stop):
●
For example, a timer in the PLC program or in the ES software of the 3SK2
-> automated test stop/manual, based on an appropriate alarm
●
Manual based on the user documentation etc.
Interrelationship, test stop interval to SIL / PL, Cat:
●
SIL 2 / PL d: Test stop at least once per year
●
SIL 3 / PL e, Cat. 3: As a minimum, a test stop every 3 months
●
SIL 3 / PL e, Cat. 4: Test stop at least once per day
Summary of Contents for PM330
Page 1: ......
Page 2: ......
Page 8: ...Table of contents Power Module PM330 6 Hardware Installation Manual 12 2018 A5E32844552B AF ...
Page 20: ...Introduction Power Module PM330 18 Hardware Installation Manual 12 2018 A5E32844552B AF ...
Page 149: ......
Page 150: ......