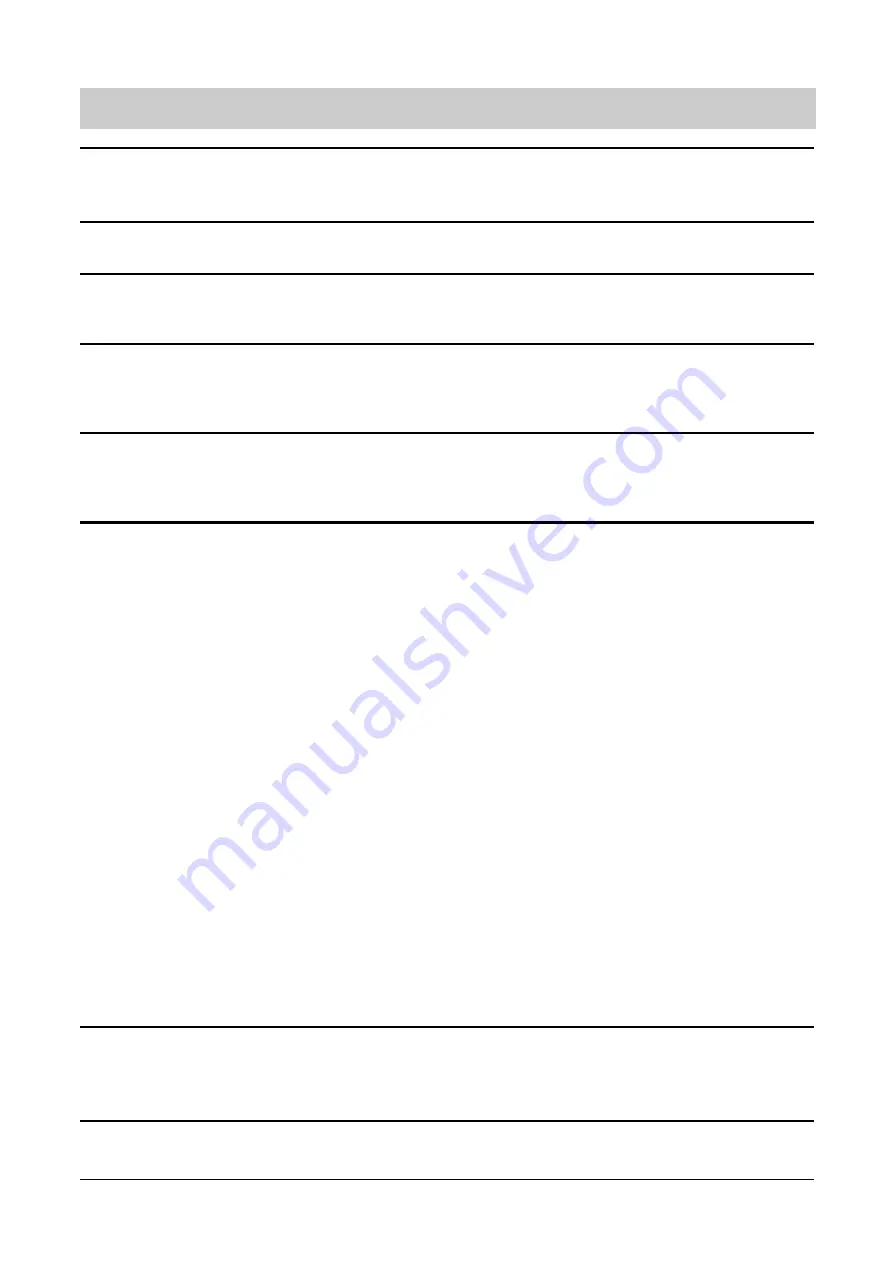
English
6. SYSTEM PARAMETERS
Parameter Function
Range
[Default]
Description / Notes
G85139-H1751-U529-D1
© Siemens plc 1999
4/8/99
44
P011
Frequency setpoint memory
0 - 1
[0]
0
= Disabled
1
= Enabled after switch-off. i.e. the setpoint alterations made with the
D
/
Ñ
buttons are stored even when power has been removed from the
inverter.
P012
·
Minimum motor frequency (Hz)
0 - 650.00
[0.00]
Sets the minimum motor frequency (must be less than the value of P013).
P013
·
Maximum motor frequency (Hz)
0.01-650.00
[50.00]
Sets the maximum motor frequency.
CAUTION:
To maintain stable operation when in sensorless vector control
mode (P077=3), the maximum motor frequency (P013), should not exceed 3x
nominal rating plate motor frequency (P081).
P014
·
Skip frequency 1 (Hz)
0 - 650.00
[0.00]
A skip frequency can be set with this parameter to avoid the effects of
resonance of the inverter. Frequencies /- (the value of P019) of this
setting are suppressed. Stationary operation is not possible within this
suppressed frequency range - the range is just passed through. Setting
P014=0 disables this function.
P015
·
Automatic restart after mains failure.
0 - 1
[0]
Setting this parameter to ‘1’ enables the inverter to restart automatically after
a mains break or ‘brownout’, provided the external run/stop switch, connected
to a digital input, is still closed, P007 = 0 and P910 = 0, 2 or 4.
0
= Disabled
1
= Automatic restart
P016
·
Start on the fly
0 - 4
[0]
Allows the inverter to start onto a spinning motor.
Under normal circumstances the inverter runs the motor up from 0 Hz. However, if
the motor is still spinning or is being driven by the load, it will undergo braking
before running back up to the setpoint - this can cause an overcurrent trip. By using
a flying restart, the inverter ‘homes in’ on the motor's speed and runs it up from that
speed to the setpoint. (
Note
: If the motor has stopped or is rotating slowly, some
‘rocking’ may occur as the inverter senses the direction of rotation prior to
restarting.)
0
= Normal restart
1
= Flying restart after power up, fault or OFF2 ( if P018 = 1).
2
= Flying restart every time (useful in circumstances where the motor
can be driven by the load).
3
= As P016 = 1 except that the inverter will only attempt to restart the
motor in the direction of the requested setpoint. The motor is
prevented from ‘rocking’ backwards and forwards during the initial
frequency scan.
4
= As P016 = 2 except that the inverter will only attempt to restart the
motor in the direction of the requested setpoint. The motor is
prevented from ‘rocking’ backwards and forwards during the initial
frequency scan.
Note:
For MIDIMASTER Vector units, it is recommended that if P016 > 0
then P018 should be set to ‘1’. This will ensure correct re-starting
if the inverter fails to re-synchronise on the initial attempt.
IMPORTANT:
When P016 > 0, care must be taken to set up the motor
nameplate data (parameters P080 toP085) and to perform an
auto stator resistance calibration (P088=1) on a cold motor.
Recommended maximum operating frequency should be less
than 120 Hz.
P017
·
Smoothing type
1 - 2
[1]
1
= Continuous smoothing (as defined by P004).
2
= Discontinuous smoothing. This provides a fast unsmoothed response to
STOP commands and requests to reduce frequency.
Note:
P004 must be set to a value > 0.0 for this parameter to have any
effect.