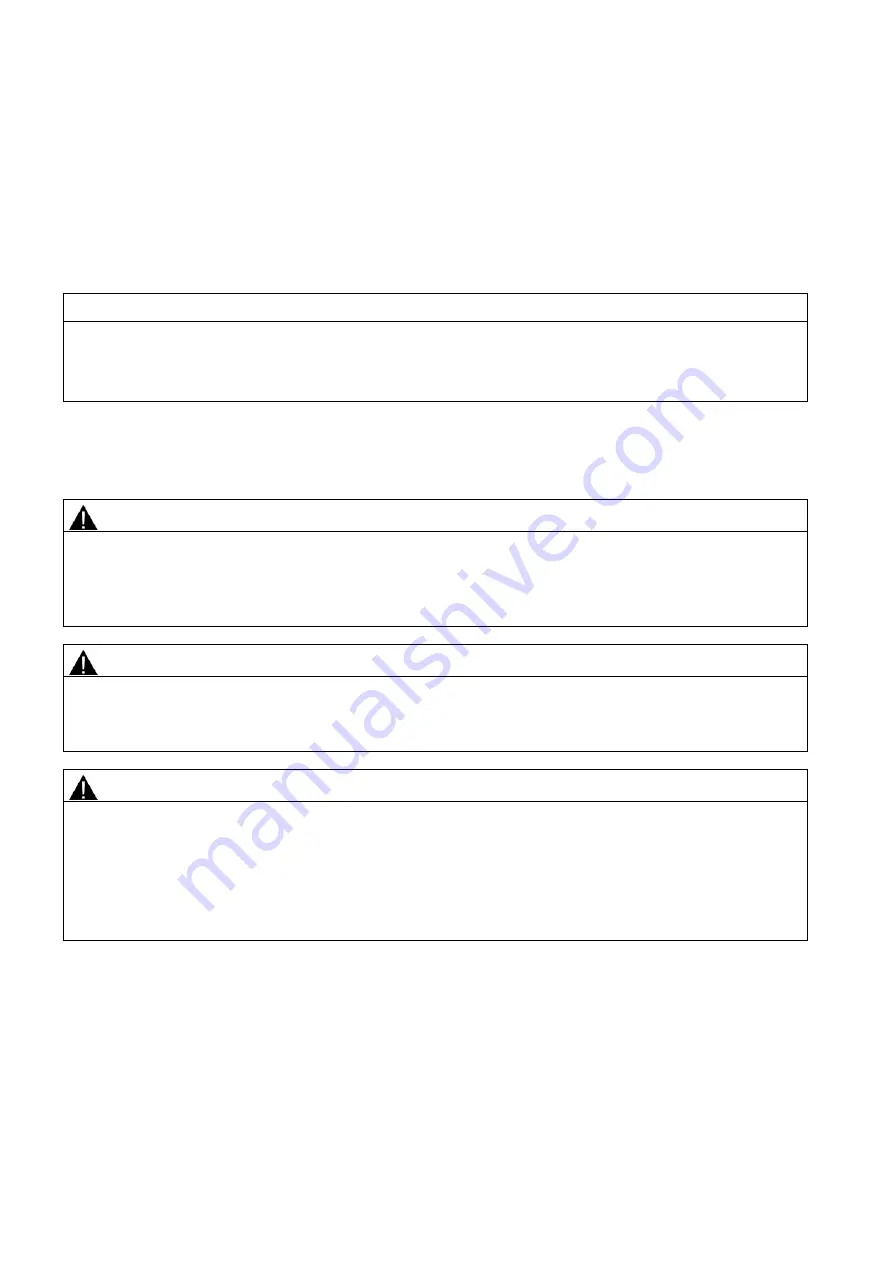
Compact Operating Instructions in accordance with EN 61010-1 and EN 60079-0
28
A5E45779389002-01, 09/2018
5
Commissioning
A useful startup of the analyzer is only possible when it is performed by a person who is familiar with the contents of the
relevant product manuals and operating instructions. The safety and warning information included there must be observed in
particular.
The analyzer has been parameterized and calibrated prior to delivery. However, a large number of parameters can be
subsequently adapted to specific requirements using menu-based functions.
The relevant product manuals/operating instructions provide you with information on the display and operator panel as well
as the operating modes. You will learn how to determine analyzer statuses, how to calibrate the analyzer, and how you can
enter or modify parameters.
NOTICE
Danger for persons and material
If uncontrolled sample gas leaks occur, this may put personnel and material in the environment of the analyzer at risk.
•
You should therefore always check the sample gas path for leaks before each startup.
•
Only start up analyzers with a leak-free sample gas path.
5.1
Safety instructions
5.1.1
General safety instructions
WARNING
Hazardous contact voltage
Risk of injury through hazardous contact voltage when the device is open or not completely closed.
The degree of protection specified on the nameplate or in Technical specifications (Page 37) is no longer guaranteed if the
device is open or not properly closed.
•
Make sure that the device is securely closed.
CAUTION
Loss of degree of protection
Damage to device if the enclosure is open or not properly closed. The degree of protection specified on the nameplate or in
Chapter "Technical specifications (Page 37)" is no longer guaranteed.
•
Make sure that the device is securely closed.
WARNING
Commissioning and operation with pending error
If an error message appears, correct operation in the process is no longer guaranteed.
•
Check the gravity of the error.
•
Correct the error.
•
If the error still exists:
–
Take the device out of operation.
–
Prevent renewed commissioning.