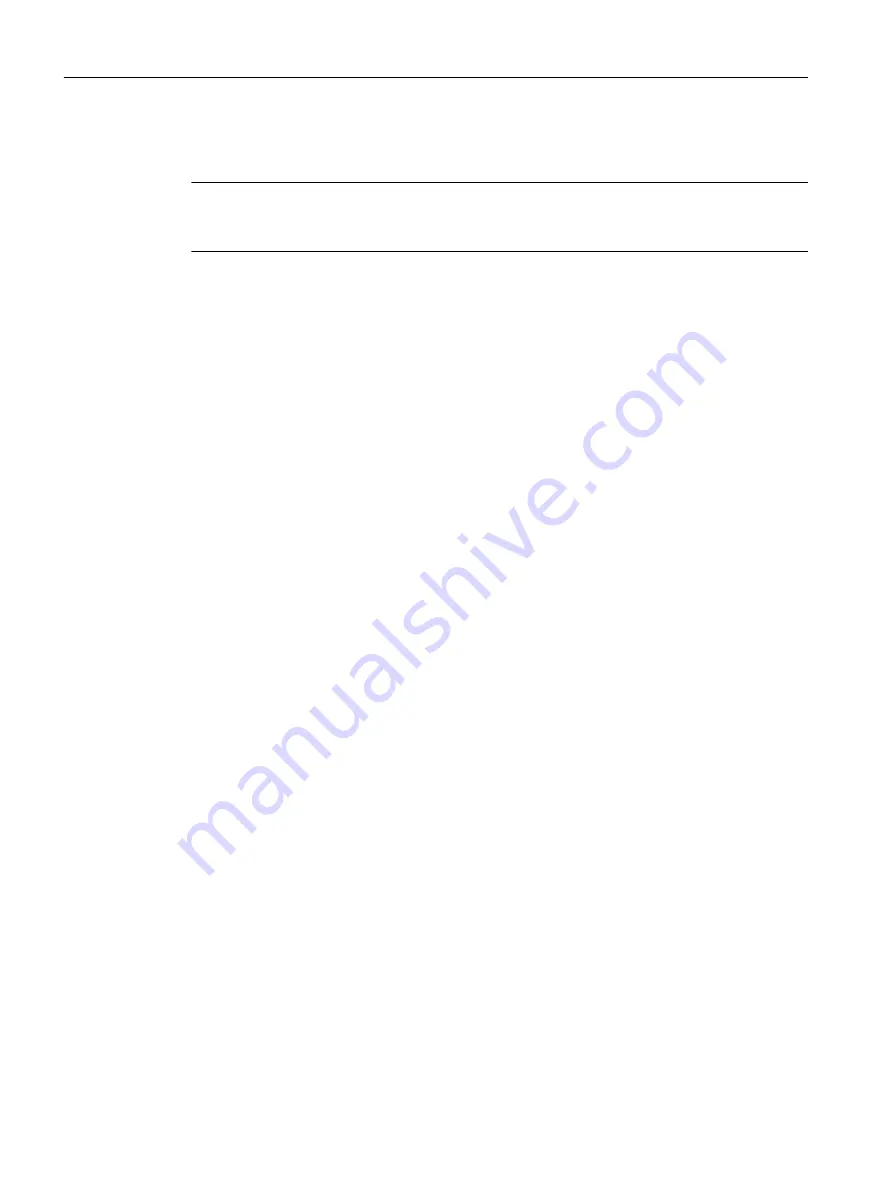
To provide this verification, you must calculate the total response time of the application you
have configured.
Note
Note that the results of calculating the response time affect the level of safety and affect the
overall design of the system.
Response time up to the switch-off procedure after expiry of the set start override time
The maximum response time up to detection of a violation of the upper/lower limit depends on
the selected parameters. The lower the set values, the longer the device requires to detect the
pending fault.
To achieve a faster response time, encoders or gear wheels that supply several pulses per
revolution can be used (e.g. encoders with 32 pulses). This reduces the time 1 / f
threshold
by the
factor of the number of pulses of the encoder or the number of teeth on the gear wheel.
The following applies in general: t
Switch-off_max
= 1 : f + t
Response
e.g. under-speed in setup mode to be checked 120 rpm = 2 Hz
with initiators (1 pulse/rev.): t
Switch-off_max
= 1 : 2 Hz + 150 ms = 650 ms
with encoder with number of pulses = 32: t
Switch-off_max
= 1 : (2 Hz x 32) + 150 ms = 166 ms
f = set frequency threshold or frequency of the applied measuring signal (e.g. under-frequency
in setup mode)
t
Response
= internal response time following detection of the switch-off frequency (max. 150 ms)
Indication on the display
In the normal operating mode, all set values can be checked at any time by pressing the "Up" or
"Down" key.
In addition, the current speed is indicated by initiator 1 or by the encoder. However, this speed
does not correspond to the accuracy of the device and is used exclusively for diagnostics
purposes!
Operation
7.1 Times
3TK2810-1 safety-related speed monitor
48
Equipment Manual, 05/2020, NEB926246402000/RS-AE/007