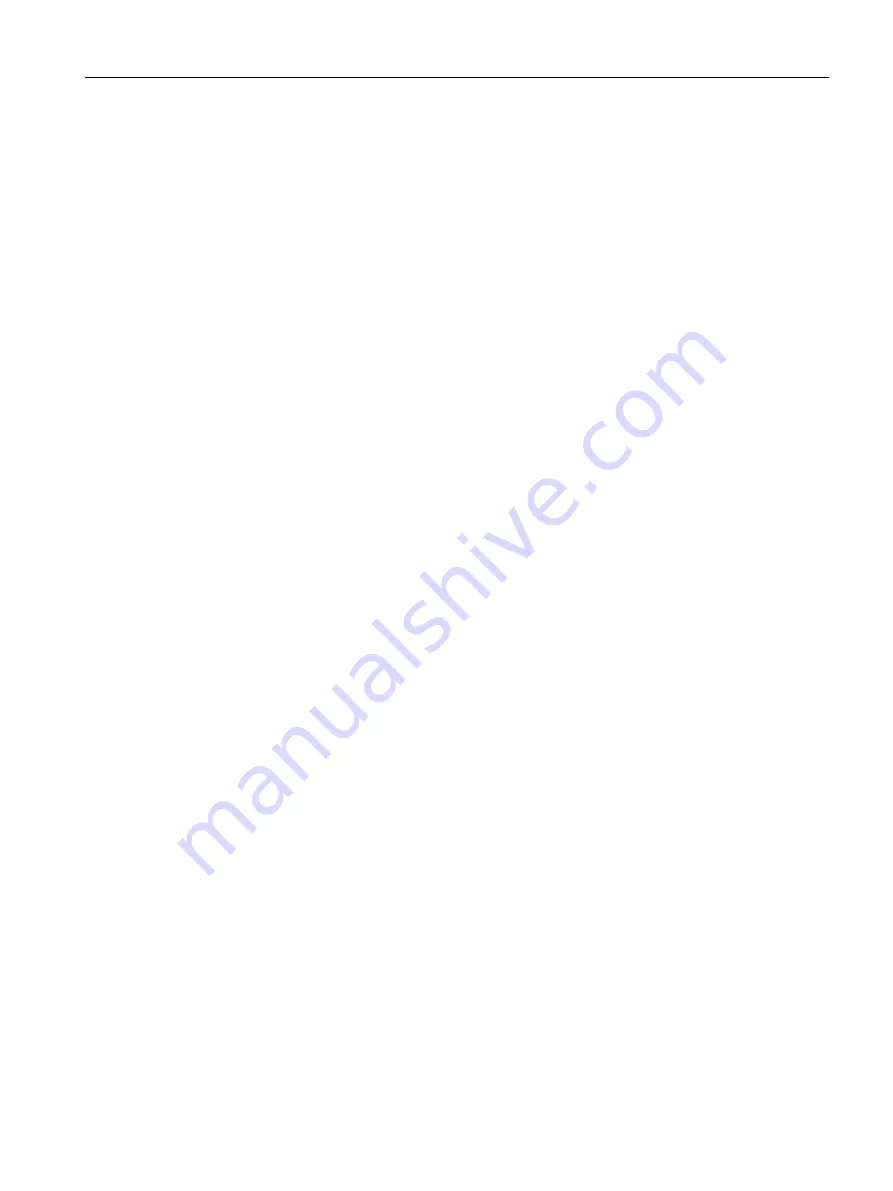
Signal input P1 and P2 (position switches for protective door)
P1 is supplied by test signal T1, and P2 by test signal T2. These terminals are used to connect the
position switches for the protective door with a tumbler. To achieve maximum fail-safety
(Performance Level e in accordance with DIN EN ISO 13849-1 and SIL3 in accordance with
IEC EN 61508), the position switches are connected with two channels.
The position switches are monitored for simultaneity. When the position switches are opened,
contacts P1 and P2 must be opened within t < 0.5 s. If simultaneity is not satisfied, a diagnostics
message appears on the display. After correction of the fault, it is necessary to perform a reset
(see Chapter "Troubleshooting (Page 64)") or a restart by switching the supply voltage off and
on.
Both position switches must be closed to start output contact 23/24. When connecting a single-
channel position switch or two individual single-channel position switches for a lower category,
detection of simultaneity must be disabled in the menu. Terminals T2 and P2 must be jumpered
when using a single-channel position switch.
If no position switches are used, terminals T1 must be jumpered with P1, and terminals T2 with
P2.
If setup mode (control of terminal EA1) is selected, monitoring of the protective door contacts
is deactivated (sensor circuits T1/P1 and T2/P2). The protective door can now be opened by an
enabling command to the interlock magnets.
Signal input EA1 and EA2 (operating mode selection)
The speed monitor is suitable for monitoring 2 operating modes (setup and automatic mode).
The relevant speed limits for both operating modes are set in the menu using the pushbuttons.
Safety-related selection of the operating mode, and thus the speed to be monitored, is carried
out with an antivalent switch connected in a two-channel configuration to connections EA1 and
EA2.
Monitoring of the setup speed is selected if EA1 is connected with T1 via the antivalent selector
switch, and EA2 is disconnected from T2 by the antivalent switch. To monitor automatic speed,
EA1 must be disconnected from T1 by the antivalent switch, and EA2 must be connected to T2
via the antivalent selector switch. The two channels of the switch are monitored for simultaneity
(t
diff
< 0.5 s). If simultaneity is not satisfied, or a cross-circuit exists between EA1 and EA2, the
device goes to a safe fault state. After correction of the fault, it is necessary to perform a reset
(see Chapter "Troubleshooting (Page 64)") or a restart by switching the supply voltage off and
on.
If the 3TK2810-1 safety-related speed monitor is switched to the setup mode (control of
terminal EA1), the output contact 13/14 closes immediately. If the machine speed is also within
the parameterized speed window, the output contact 23/24 closes.
Functions
4.1 Terminals and their functions
3TK2810-1 safety-related speed monitor
Equipment Manual, 05/2020, NEB926246402000/RS-AE/007
33