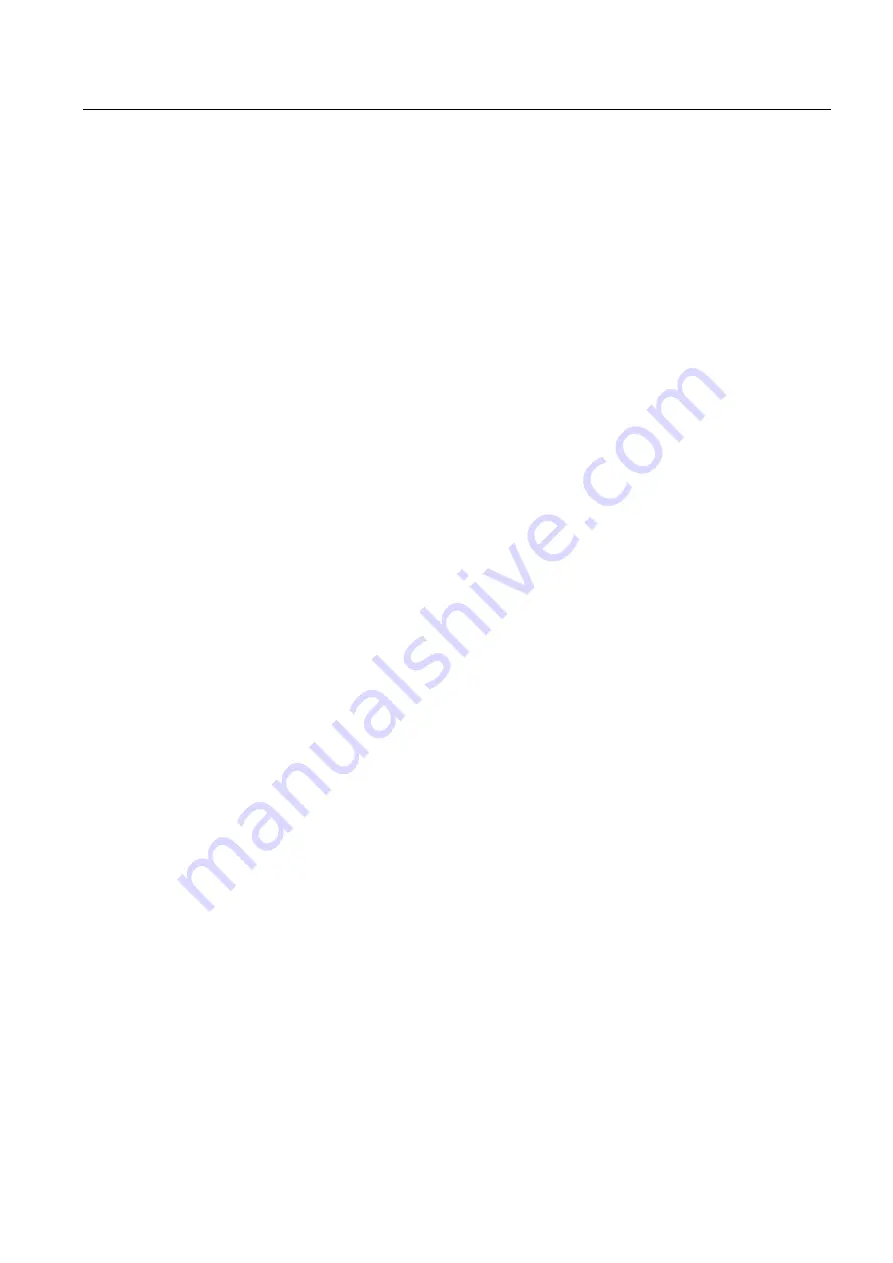
Configuration
2.4 Procedure when engineering
1FT7 Synchronous Motors
Configuration Manual, (PFT7S) 01/2009, 6SN1197-0AD13-0BP2
45
2.4.1
Clarification of the type of drive
The motor is selected on the basis of the required torque, which is defined by the application,
e.g. traveling drives, hoisting drives, test stands, centrifuges, paper and rolling mill drives,
feed drives or main spindle drives. Gearboxes to convert motion or to adapt the motor speed
and motor torque to the load conditions must also be considered.
As well as the load torque, which is determined by the application, the following mechanical
data is among those required to calculate the torque to be provided by the motor:
●
Masses to be moved
●
Diameter of the drive wheel
●
Leadscrew pitch, gear ratios
●
Frictional resistance
●
Mechanical efficiency
●
Traversing paths
●
Maximum velocity
●
Maximum acceleration and maximum deceleration
●
Cycle time
2.4.2
Defining the supplementary conditions and integration into an automation system
You must decide whether synchronous or induction motors are to be used.
Synchronous motors are the best choice if it is important to have low envelope dimensions,
low rotor moment of inertia and therefore maximum dynamic response ("Servo" control type).
Induction motors can be used to increase maximum speeds in the field weakening range.
Induction motors for higher power ratings are also available.
The following factors are especially important when engineering a drive application:
●
The line system configuration, when using specific types of motor and/or line filters on IT
systems (non-grounded systems)
●
The utilization of the motor in accordance with rated values for winding temperature rise
60 K or 100 K.
●
The ambient temperatures and the installation altitude of the motors and drive
components.
●
Heat dissipation from the motors through natural ventilation, forced ventilation or water
cooling
Other constraints apply when integrating the drives into an automation environment such as
SINUMERIK or SIMOTION.
For motion control and technology functions (e.g. positioning), as well as for synchronous
operation functions, the corresponding automation system, e.g. SIMOTION D, is used.
Summary of Contents for 1FT7 Series
Page 2: ......
Page 12: ...Preface 1FT7 Synchronous Motors 12 Configuration Manual PFT7S 01 2009 6SN1197 0AD13 0BP2 ...
Page 251: ......