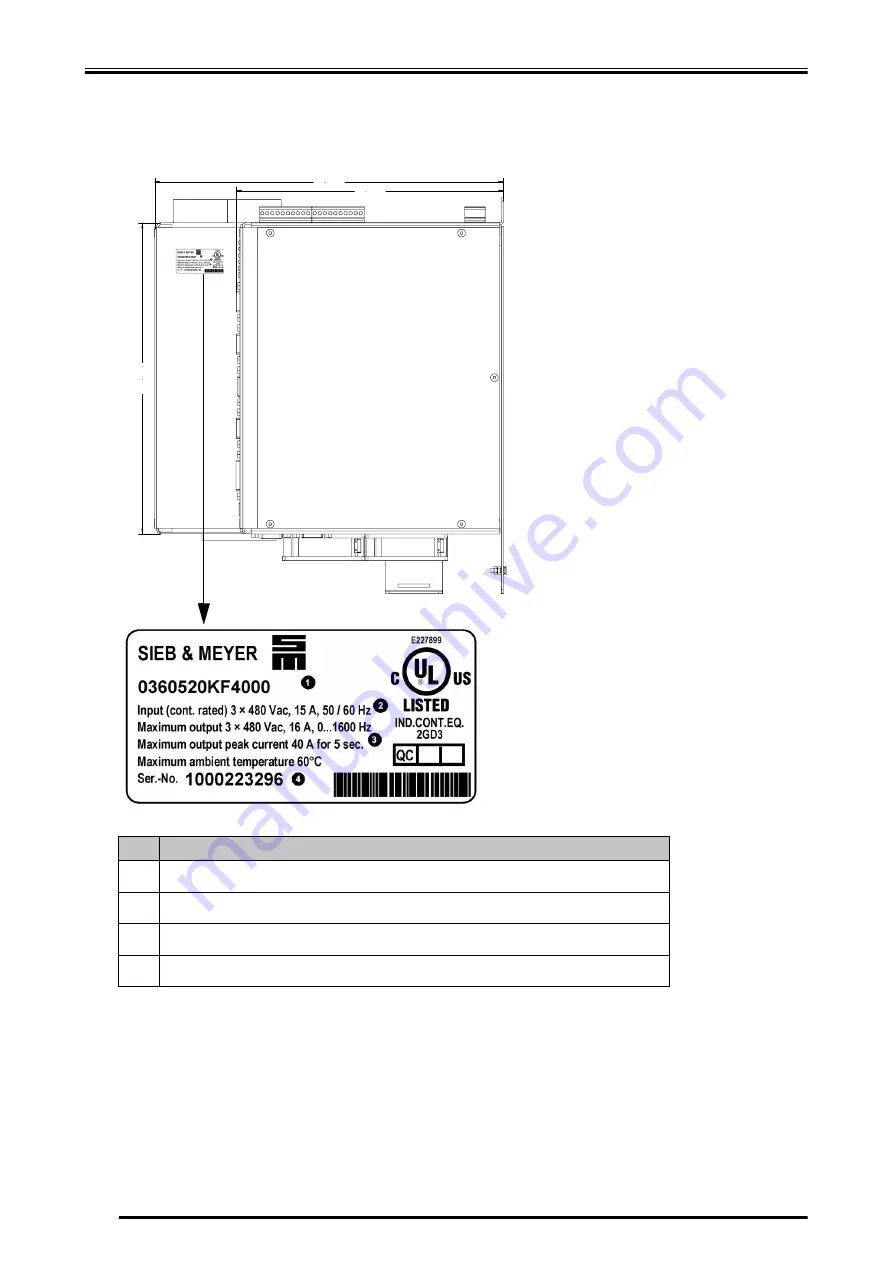
sinudyn-36
Hardware Description 0360520xx
23
6.2
Type Plate
sinudyn
-0360520xx
Nach DIN 7168
211.00
276.00
242
.
0
0
No.
Meaning
n
Module designation (0360520KF) with indication of the option module (4000), see
o
Mains voltage
p
rated current/peak current
q
serial number
Summary of Contents for sinudyn-0360520 Series
Page 7: ...Symbols 6 Symbols...
Page 13: ...Safety Instructions and Application Advice 12 Safety Instructions Application Advice...
Page 15: ...Unit Assembly Complying EMC 14 EMC...
Page 59: ...Specification of the Digital Inputs and Outputs 58 Hardware Description 0360520xx sinudyn 36...
Page 75: ...General Information Regarding the Wiring 74 Hardware Description 0360520xx...
Page 93: ...Appendix Manufacturers 92 List of Manufacturers...