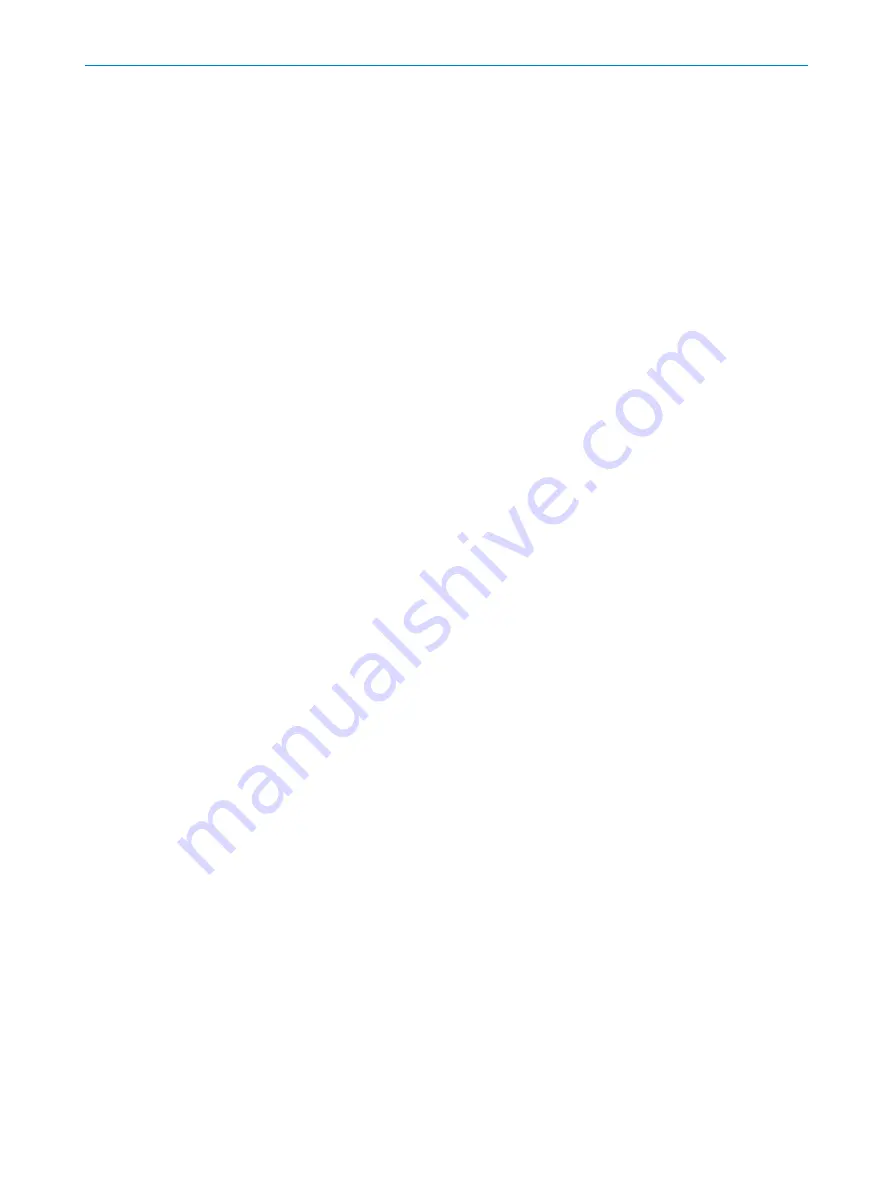
12.2
FCC and IC radio approval
The device fulfills the EMC requirements for use in the USA and Canada, in accordance
with the following extracts from the relevant approvals:
FCC § 15.19
This device complies with Part 15 of the FCC rules. Operation is subject to the following
two conditions:
•
This device may not cause harmful interference, and
•
this device must accept any interference received, including interference that may
cause undesired operation.
FCC §15.21 (warning statement)
[Any] changes or modifications not expressly approved by the party responsible for com‐
pliance could void the user’s authority to operate the equipment.
IC
This device complies with Industry Canada’s licence-exempt RSSs. Operation is subject
to the following two conditions:
•
This device may not cause interference; and
•
This device must accept any interference, including interference that may cause
undesired operation of the device.
Le présent appareil est conforme aux CNR d’Industrie Canada applicables aux appa‐
reils radio exempts de licence. L’exploitation est autorisée aux deux conditions sui‐
vantes :
•
l’appareil ne doit pas produire de brouillage;
•
l’utilisateur de l’appareil doit accepter tout brouillage radioélectrique subi, même
si le brouillage est susceptible d’en compromettre le fonctionnement.
12
ANNEX
40
O P E R A T I N G I N S T R U C T I O N S | TR10 Lock
8019972/2016-07-19 | SICK
Subject to change without notice