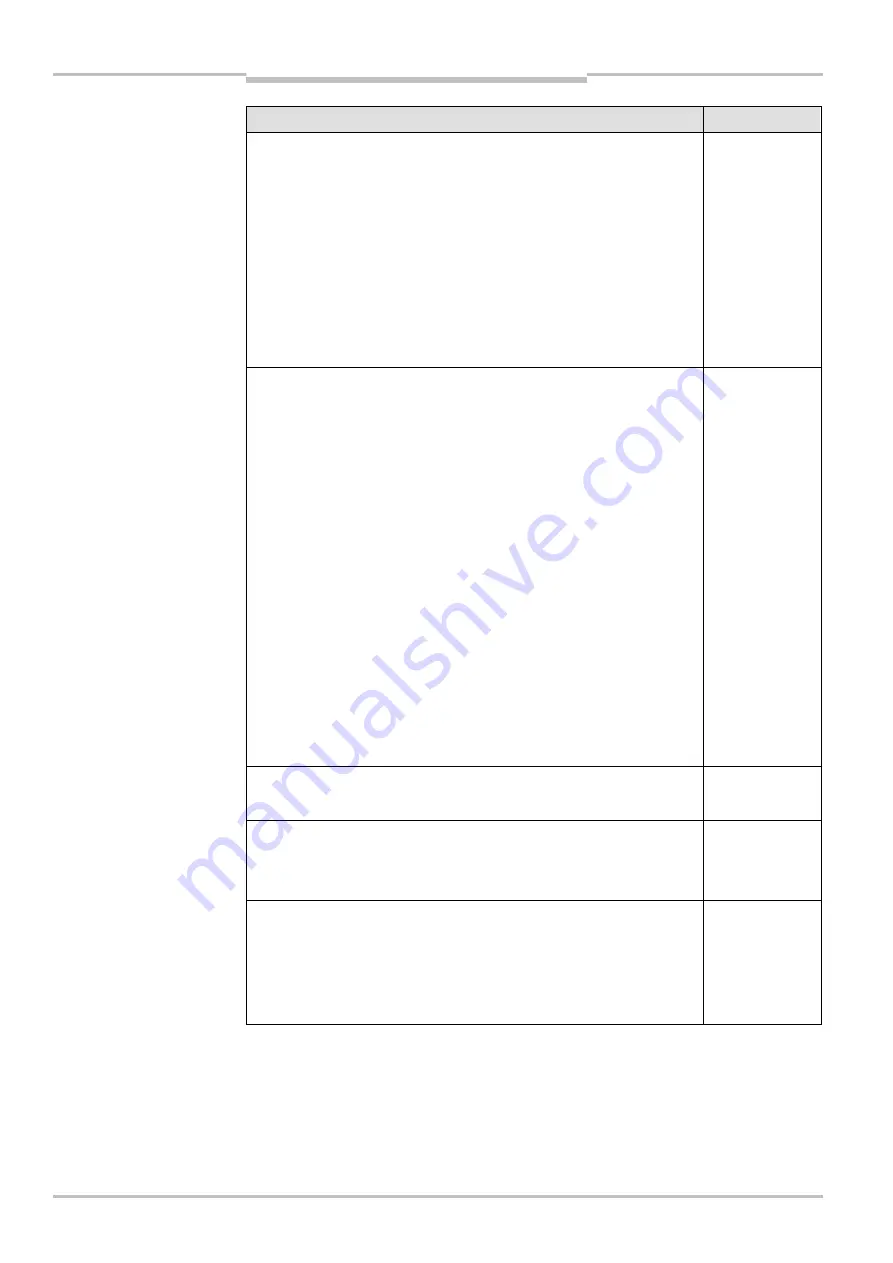
Chapter
14
Operating Instructions
M4000 Adv., Adv. A/P, Area
140
© SICK AG • Industrial Safety Systems • Germany • All rights reserved
8010797/YT72/2016-02-19
Subject to change without notice
Ordering information
Part
Part number
Muting lamps
for connection to UE403
Version with incandescent lamp, incl. 2 m connecting cable with
M12 plug, mounting bracket and mounting kit
2033116
Version with incandescent lamp, incl. 10 m connecting cable with
M12 plug, mounting bracket
2033117
Version with LED, incl. 2 m connecting cable with M12 plug,
mounting bracket and mounting kit
2033118
Version with LED, incl. 10 m connecting cable with M12 plug,
mounting bracket
2033119
Muting mechanism components
1 × round steel arm 400 mm
For PU3H column profile and M4000 device profile
incl. 1 × universal bracket
2045506
incl. 2 × universal brackets
2045507
incl. 1 × universal bracket with reflector P250 fitted
2045513
incl. 2 × universal brackets with reflectors P250 fitted
2045512
incl. 1 × universal bracket with sensor WL280P132 fitted and 2 m
connecting cable with M12 plug
2045729
incl. 2 × universal brackets with sensors WL280P132 fitted and
2 m connecting cable with M12 plug
2045730
2 × round steel arm 400 mm
For PU3H column profile and M4000 device profile
incl. 4 × universal brackets (for exit monitoring)
2045508
incl. 2 × universal brackets with sensors WL280P132 mounted and
2 m connection cable with M12 plug and 2 × universal brackets
with reflectors P250 mounted (for exit monitoring)
2060157
Connection cable for PC
For the connection between PC and M4000 or UE403 (2.0 m)
6021195
External laser alignment aid
AR60 1015741
Adapter for M4000 housing
4040006
Accessories included in a standard delivery
CDS (Configuration & Diagnostic Software) on CD
E
ROM incl. Online
documentation and operating instructions in all available languages
2032314
Sliding nuts for mounting bracket/side bracket, 4 pcs
2017550
Alignment template for integrated laser alignment aid
4040263
41)
Only with devices with integrated laser alignment aid.