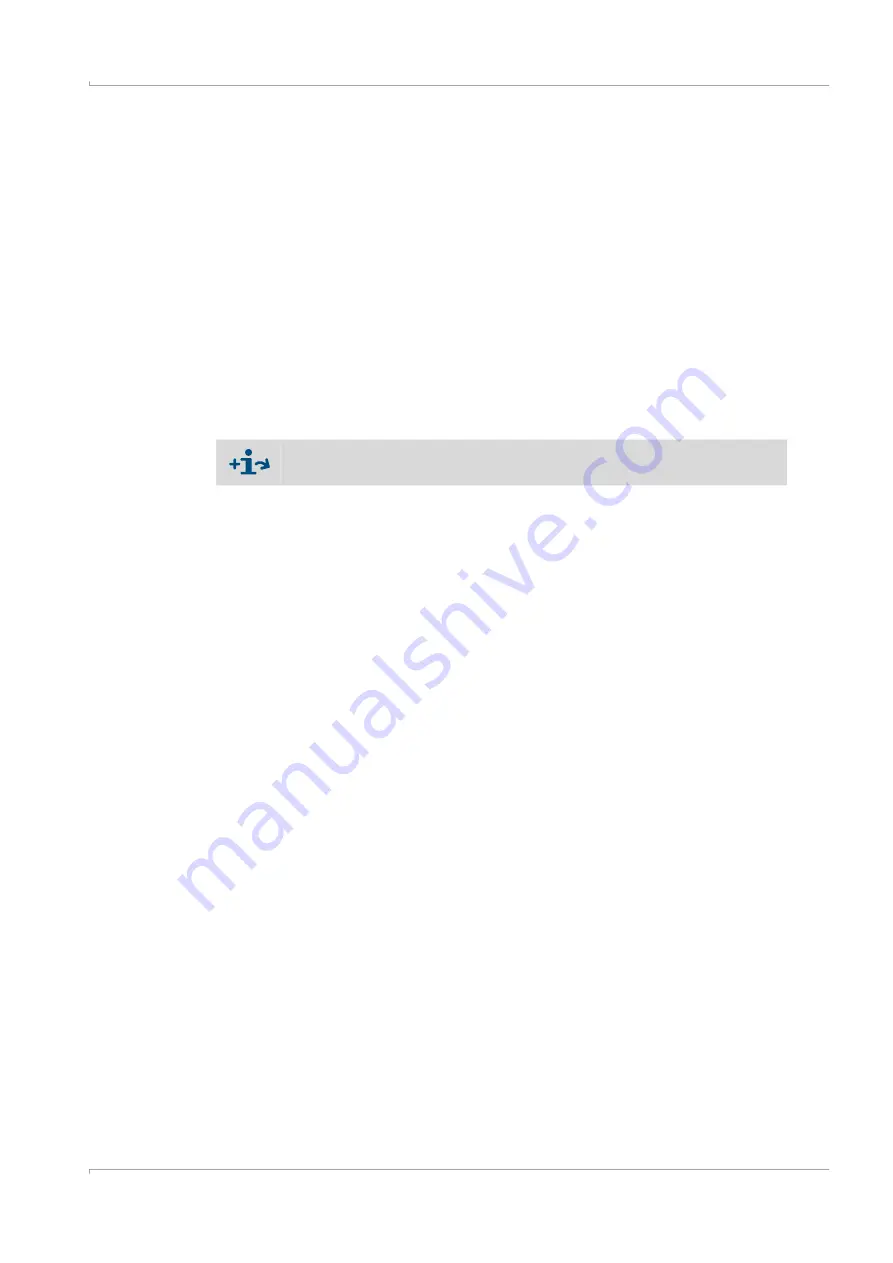
Product description
FLOWSIC600-XT · Operating Instructions · 8018846/1BHP/V2-1/2021-05 · © SICK Engineering GmbH
29
Su
bje
ct to
ch
an
ge
w
ith
ou
t n
otic
e
2.6.4
Serial data interfaces
● RS-485 (3x, for configuration, measured value output and diagnostics)
MODBUS ASCII, MODBUS RTU;
The configuration of the RS485.1 interface at the factory is configured uniform to
support smooth calibration of the device.
Configuration:
– Protocol type: MODBUS-RTU
– Modbus configuration: FL600XT (standard)
– Baud rate: 38,400 baud
– Bit protocol: 8N1
● Ethernet (1x optional for configuration, measured value output and diagnostics),
MODBUS TCP
The serial interfaces can be used as metrological secured point to point connection for
connecting volume converters or auxiliary equipment. In this case, the compatibility is
defined in the documents of the downstream device.
2.6.5
Optical data interface
The FLOWSIC600-XT has an optical interface compliant with IEC 62056-21 on the front
panel with bit-serial, asynchronous data transfer (protocol MODBUS RTU).
A computer can be connected using an infrared/USB adapter (Part No. 6050602).
The interface can be used to read out data and parameter values as well as to configure
the device. A firmware update can be carried out using this interface when the parameter
locking switch is open.
2.7
Totalizers
In addition to the main encoder totalizer, the volumes measured during a malfunction are
recorded for each flow direction by a special malfunction volume encoder totalizer.
Resetting the malfunction volume encoder totalizer can be traced in the Event logbook of
the meter.
The FLOWSIC600-XT is designed bi-directional and has a configurable zero-flow cutoff set
to 0.25 Q
min
at the factory.
2.8
Diagnostics function i-diagnostics
TM
i-diagnostics™ is the intelligent combination of firmware and software that means safe,
reliable, and easy to use device operation for the entire operating time.
i-diagnostics™ is based on the FLOWSIC600's CBM (Condition Based Maintenance) smart
self-diagnostics functionality. In addition to meter diagnostics, it provides useful
information about the system status and any changes to it.
In order to assess the application, diagnostics data from cross-eyed beams is first factored
in, with application faults, such as blocked flow conditioners, background noise, corrosion
or liquids in the gas being detected automatically. Process data is constantly assessed on
the basis of the integrated Fingerprint concept.
This means the measurement conditions during calibration can be compared with the
measurement conditions during commissioning and with the current measurement and
diagnostics data. An internal dialog continuously logs measured values which allow trend
analyses to check the historical measurement process. An internal dialog continuously logs
the self-monitoring results so that a retroactive check of the measurement process in the
form of a graphic trend analysis is also possible.
For further information, see document “8019260 Addendum to Operating
Instructions FLOWSIC600-XT: Interfaces”.