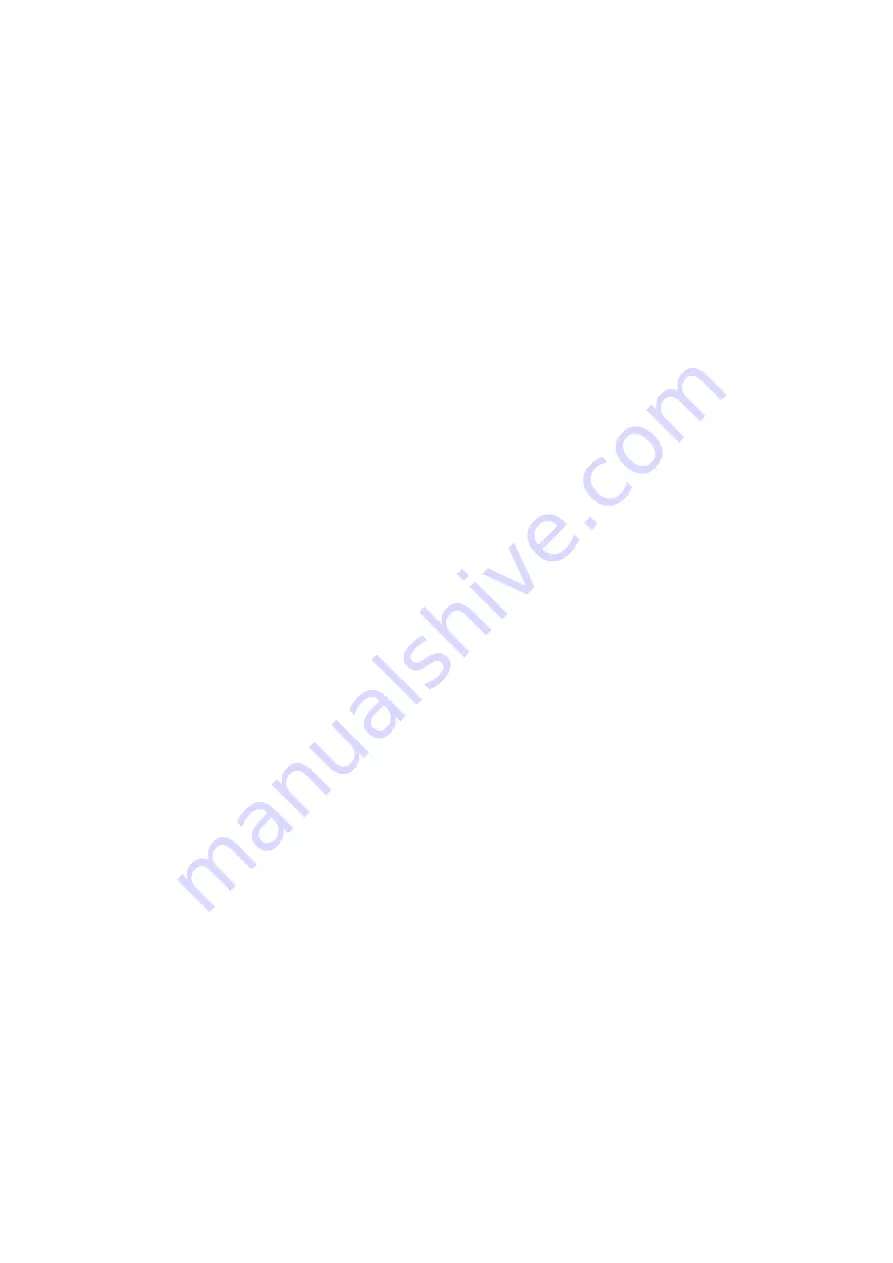
First calibrate sensitivity and then set the zero position for the assembly.
If the message persists, check the following:
that the search card reads correctly by performing the encoder test (see paragraph “Service programmes”);
PK modules and phases as indicated in the paragraph “Service Programmes”.
E 3 I/E 2/3
Error condition at end of sensitivity calibration. Repeat the calibration; if the message persists perform the following checks:
Correct sensitivity calibration procedure; Correct fastening and position of the calibration weight;
Check mechanical integrity of the calibration weight;
Check that the search card is reading correctly by performing the encoder test;
PK modules and phases as indicated in the paragraph “Service Programmes”:
Geometry of the wheel used
If the first gramme display function is enabled in the service environment (indicated by “1 ON” in the relative area), the following parameters
are displayed at the end of calibration:
L1= residual wheel unbalance calculated with respect to the barycentre of the calibration weight. The recommended value is less than 100g per
side, otherwise balance the wheel before performing the calibration;
L2= unbalance detected with the calibration weight in position as indicated in the second calibration spin. This value must be 100g +/-5 on the
inner side and less than 5g on the outer side;
L3= unbalance detected with the calibration weight in position as indicated in the third calibration spin. This value must be less than 5g on the
inner side and 100g +/-5 on the outer side.
When error “E 3” is displayed, this means that the grammes acquired by the machine during the second (L2) and/or third spin (L3), are out of
tolerance, therefore the previously described checks must be performed.
E 4
Error condition during calibration of
internal sensor and/or of external sensor (if installed). Calibrate the internal sensor and the external sensor, if present.
E 6
Error condition when executing optimisation programme.
Repeat the procedure from the beginning.
E 12
a) Width sensor not in the rest position when machine was switched on. Switch off the machine, return the sensor to the correct position and
switch back on.
b) External sensor not present or faulty. Visualisation of this error can be disabled by performing the following procedure:
- Select the "Sensor calibration" icon and press Enter.
E 27
Excessive braking time. Check:
• that relay “RL1”, which inverts current for braking, is working correctly. If the relay functions correctly, at the beginning of braking, you will
hear a mechanical tone coming from the power supply card. If not, replace the PEAL32F power supply card;
• check that the motor cables are connected correctly in the 6-pole connector;
• check that the 6-pole connector is connected correctly to the PEAL32F card.
E 28
Encoder counting error.
In this case, check the following:
• check the state of the encoder disc;
• check that the search card reads correctly by performing the encoder test (see paragraph “Service Programmes);
• check that the search card and the Main board are connected correctly with the 8 pole ribbon cable;
• if necessary, replace the search card or the Main board.
E 30
Wheel spin device failure.
Error condition related to the non-rotation of the unit after pressing the START key.
If the wheel begins to rotate:
• check the encoder card is working.
If the motor does not start up:
• check that the motor power supply cable is correctly connected to the PEAL32F power supply card;
• check that the PEAL32F power supply card is working;
• check the motor is working.
E 32
The wheel balancer was jolted during the reading phase. Repeat the spin.
The wheel balancer makes checks on the disturbances; if the machine suffers excessive jolts during the reading of the unbalances, it displays
this error.
If the machine was not knocked, check inside the machine whether:
• the wheel balancer is resting firmly on the floor;
• the swinging unit has noisy bearings;
• the securing ring nut is fastened tightly.
• check that the search card reads correctly by performing the encoder test (see paragraph “Service Programmes");
• check PK modules (see paragraph “Service Programmes“).
CCC CCC
Summary of Contents for S 64E
Page 43: ...Fig 20 fig 21...
Page 45: ......
Page 46: ...SECOND VERSION OF PNEUMATIC SYSTEM from April 2016...
Page 47: ...THIRD VERSION OF PNEUMATIC SYSTEM from March 2017...
Page 48: ...FOURTH VERSION OF PNEUMATIC SYSTEM...
Page 50: ...PEAL 32F...
Page 51: ......
Page 52: ...MBUGRF 2 LIGHT...
Page 53: ......
Page 54: ...COMIM Cod 4 119446B_EN 05 2018...