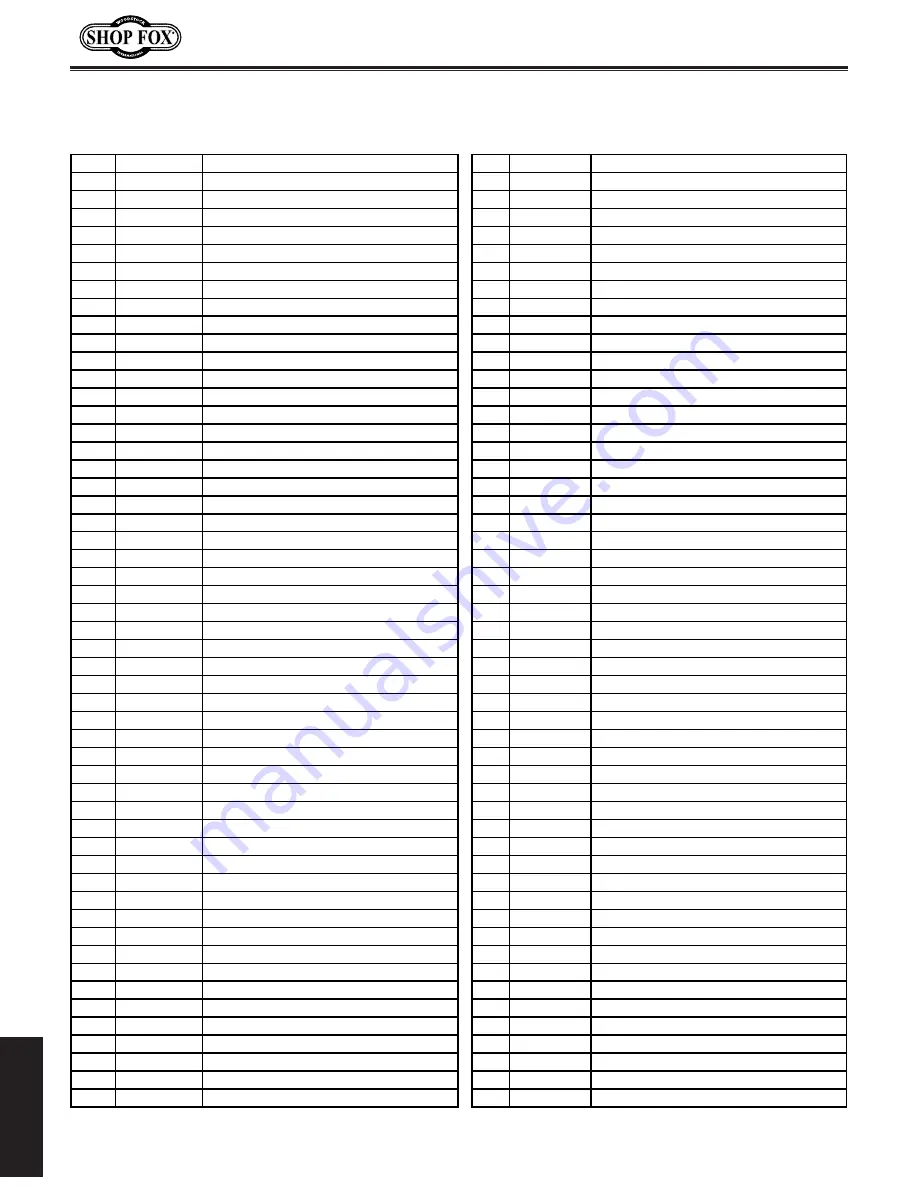
-50-
Model W1867/W1868/W1869 (For Machines Mfd. Since 11/18)
PA
RT
S
W1867.Parts.List
REF PART #
DESCRIPTION
REF PART #
DESCRIPTION
1
X1867001
BASE
44
X1867044
PHLP HD SCR M6-1 X 10
2
X1867002
SUPPORT LEG
45
X1867045
PHLP HD SCR M5-.8 X 8
3
X1867003
IMPELLER HOUSING
46
X1867046
PADDLE SPINDLE BRACKET RETAINER
4
X1867004
COLLECTION DRUM, 20 GALLON
47
X1867047
PHLP HD SCR M5-.8 X 15
5
X1867005
INTAKE BARREL
49
X1867049
MAG SWITCH NHD MS1-12D 110V
6
X1867006
CYCLONE FUNNEL
49-1 X1867049-1 CONTACTOR NHD C-12D10 110V
7
X1867007
FILTER COVER PLATE
49-2 X1867049-2 E-STOP SWITCH NHD NPB22-H
8
X1867008
CANISTER FILTER ASSY 14-1/2" X 24"
49-3 X1867049-3 CONTACT BLOCK NHD CB-01
9
X1867009
COLLECTION DRUM LID
49-4 X1867049-4 REMOTE CONTROL RECEIVER
10
X1867010
CASTER 2", SWIVEL
49-5 X1867049-5 STRAIN RELIEF TYPE-3 M20-1.5
11
X1867011
HEX NUT 5/16-18
49-6 X1867049-6 MAG SWITCH BASE
12
X1867012
CASTER 2-1/2", LOCKING SWIVEL
49-7 X1867049-7 MAG SWITCH COVER
13
X1867013
INLET ADAPTER 6" X 4" X 2
49-8 X1867049-8 PHLP HD SCR 10-24 X 3/4
14
X1867014
LOCK HANDLE GUIDE
49-9 X1867049-9 HEX NUT 10-24
15
X1867015
MOUNTING PLATE
50
X1867050
FILTER BAG 20" X 23"
16
X1867016
SPRING BRACKET
51
X1867051
BAG CLAMP 15"
17
X1867017
COPPER PLATE
52
X1867052
INLET ADAPTER CAP 4"
19
X1867019
HEX BOLT 5/16-18 X 1
53
X1867053
PHLP HD SCR 10-24 X 3/8
20
X1867020
LOCK NUT 5/16-18
54
X1867054
FLANGE BOLT 5/16-18 X 3/4
21
X1867021
COMPRESSION SPRING 3 X 33 X 70
55
X1867055
FLAT HD SCR 5/16-18 X 1-1/4
22
X1867022
SPRING RETAINER
56
X1867056
BUTTON HD CAP SCR 5/16-18 X 1/2
23
X1867023
DRUM LOCK HANDLE
57
X1867057
COLLECTION DRUM LID LATCH
24
X1867024
LOCK HANDLE LINK
58
X1867058
FLEX HOSE 7" X 5"
25
X1867025
FLAT WASHER 3/8 PLASTIC
59
X1867059
FILTER PADDLE
26
X1867026
BUTTON HD CAP SCR 5/16-18 X 3/4
60
X1867060
HEX BOLT M6-1 X 12
27
X1867027
FLAT WASHER 5/16
61
X1867061
FOAM GASKET, 120 X 140MM
28
X1867028
HEX BOLT 5/16-18 X 1-3/4
62
X1867062
DRUM WINDOW, 120 X 140MM ACRYLIC
29
X1867029
MOTOR 1.5HP 110V 1-PH
63
X1867063
RIVET 2 X 4MM
29-1
X1867029-1 MOTOR FAN COVER
64
X1867064
COLLECTION DRUM HANDLE
29-2
X1867029-2 MOTOR FAN
65
X1867065
PHLP HD SCR 1/4-20 X 5/8
29-3
X1867029-3 MOTOR JUNCTION BOX
66
X1867066
ACORN NUT 1/4-20
29-4
X1867029-4 R CAPACITOR 50M 250V 1-1/2 X 2-3/8
67
X1867067
REMOTE CONTROL
29-5
X1867029-5 S CAPACITOR 300M 125V 1-3/8 X 2-5/8
67-1 X1867067-1 REMOTE BATTERY TYPE A27 12V
29-6
X1867029-6 CIRCUIT BREAKER ZING EAR ZE-700 25A
68
X1867068
PHLP HD SCR M4-.7 X 8
29-7
X1867029-7 STRAIN RELIEF TYPE-2 15MM
69
X1867069
LOCK NUT M4-.7
29-8
X1867029-8 CENTRIFUGAL SWITCH
70
X1867070
IMPELLER 12-3/4"
29-9
X1867029-9 CONTACT PLATE
71
X1867071
IMPELLER WASHER 6 X 38 X 4MM
29-10 X1867029-10 MOTOR CORD W/PLUG 14G 3W 30"
72
X1867072
CAP SCREW M6-1 X 30
29-11 X1867029-11 BALL BEARING 6203-2RS
73
X1867073
COLLECTION DRUM GASKET
29-12 X1867029-12 BALL BEARING 6205-2RS
74
X1867074
HOSE CLAMP 1-3/4"
31
X1867031
FENDER WASHER 5/16
75
X1867075
VACUUM HOSE 1-1/2" X 60"
32
X1867032
RUBBER GASKET 43MM
76
X1867076
HOSE CLAMP 8-1/2"
33
X1867033
BEARING RETAINER, UPPER
77
X1867077
POWER CORD 14G 3W 72" 5-15P
34
X1867034
PHLP HD SCR M5-.8 X 8
78
X1867078
VACUUM RING
35
X1867035
SLEEVE BEARING 12 X 14 X 6MM
79
X1867079
COLLECTION DRUM BAG 30" X 41"
36
X1867036
FILTER PADDLE HANDLE
80
X1867080
GROUND WIRE 18G 17-1/2"
37
X1867037
FLANGE BOLT 5/16-18 X 1/2
81
X1867081
PHLP HD SCR 10-24 X 3/8
38
X1867038
BEARING RETAINER, LOWER
82
X1867082
HEX NUT 10-24
39
X1867039
PADDLE HANDLE SPINDLE
83
X1867083
FLANGE NUT 5/16-18
40
X1867040
HEX BOLT M6-1 X 16
84
X1867084
LOCK HANDLE STOP
41
X1867041
FILTER PADDLE SPINDLE
85
X1867085
KEY 7 X 7 X 29
42
X1867042
PADDLE SPINDLE BRACKET
86
X1867086
CAP SCREW M6-1 X 16
43
X1867043
FLAT WASHER 1/4
87
X1867087
EXT TOOTH WASHER #10
Summary of Contents for W1867
Page 57: ...Model W1867 W1868 W1869 For Machines Mfd Since 11 18...
Page 60: ......