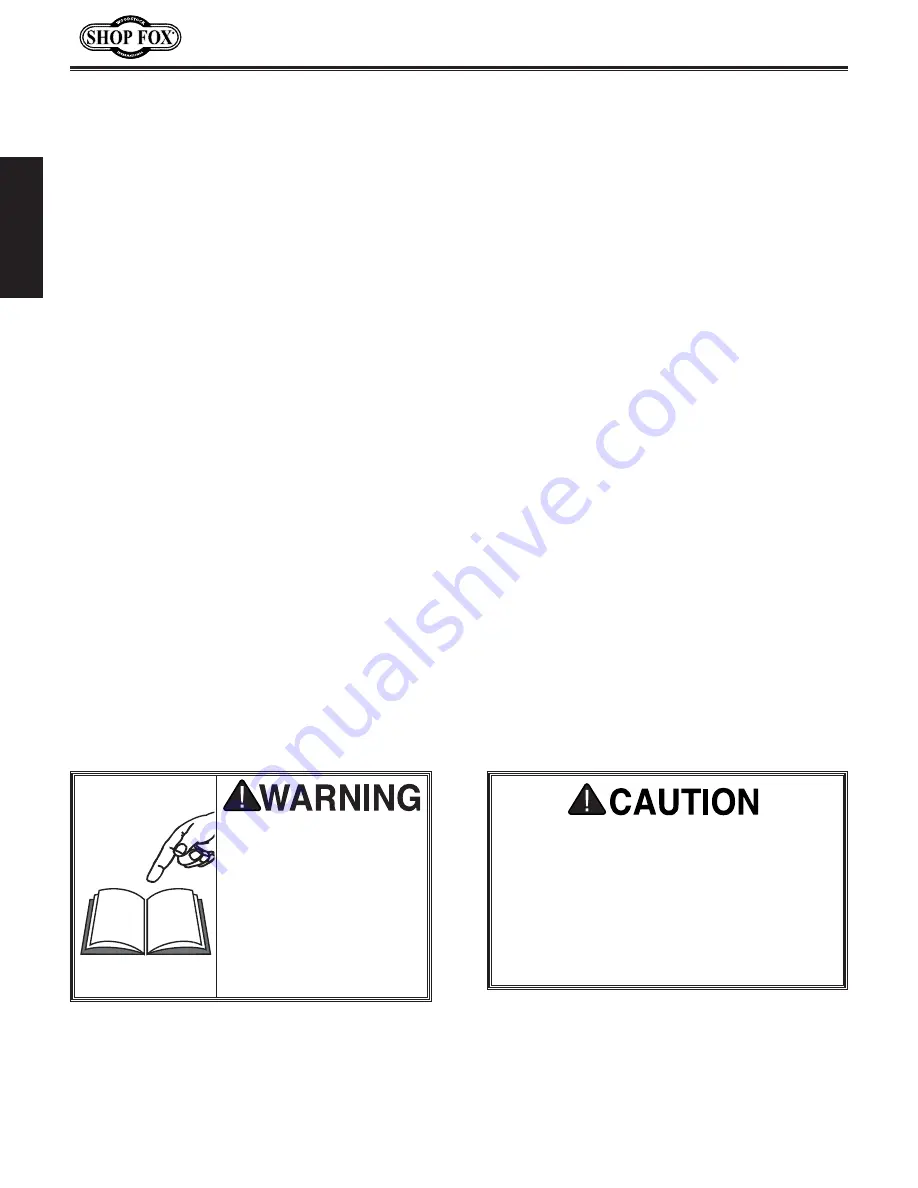
-8-
M1036 Micro Mill
SA
FE
T
Y
Additional.Safety.for.Milling.Machines
READ.and.understand.this.
entire.manual.before.using.
this.machine..Serious.per-
sonal. injury. may. occur.
if. safety. and. operational.
information. is. not. under-
stood. and. followed.. DO.
NOT. risk. your. safety. by.
not.reading!
USE.this.and.other.machinery.with.caution.
and. respect.. Always. consider. safety. first,.
as. it. applies. to. your. individual. working.
conditions.. No. list. of. safety. guidelines.
can.be.complete—every.shop.environment.
is. different.. Failure. to. follow. guidelines.
could. result. in. serious. personal. injury,.
damage.to.equipment.or.poor.work.results.
UNDERSTANDING.CONTROLS..
The mill is a
complex machine that presents severe cutting
or amputation hazards if used incorrectly. Make
sure you understand the use and operation of all
controls before you begin milling.
SPINDLE.SPEED.
To avoid tool or workpiece
breakage that could send flying debris at the
operator and bystanders, use the correct spindle
speed for the operation. Allow the spindle to
gain full speed before beginning the cut.
CHIP.CLEANUP.
Chips from the operation are
sharp and hot. Touching them can cause burns
or cuts. Using compressed air to clear chips
could cause them to fly into your eyes, and may
drive them deep into the working parts of the
machine. Use a brush or vacuum to clear away
chips and debris from machine or workpiece and
NEVER clear chips while spindle is turning.
CUTTING.TOOL.USAGE.
Cutting tools have very
sharp leading edges—handle them with care!
Using cutting tools that are in good condition
helps to ensure quality milling results and
reduces risk of personal injury from broken tool
debris. Inspect cutting tools for sharpness, chips,
or cracks before each use, and ALWAYS make
sure cutting tools are firmly held in place before
starting the machine.
STOPPING.SPINDLE.
To reduce the risk of hand
injuries or entanglement hazards, DO NOT
attempt to stop the spindle with your hand or a
tool. Allow the spindle to stop on its own or use
the spindle brake.
MACHINE.CARE.&.MAINTENANCE.
Operating
the mill with excessively worn or damaged
machine parts increases risk of machine or
workpiece breakage which could eject hazardous
debris at the operator. Operating a mill in poor
condition will also reduce the quality of the
results. To reduce this risk, maintain the mill in
proper working condition by ALWAYS promptly
performing routine inspections and maintenance.
SAFETY.ACCESSORIES.
Flying chips or debris
from the cutting operation can cause eye injury
or blindness. Always use safety glasses or a face
shield when milling.
WORK.HOLDING.
Before starting the machine,
be certain the workpiece has been properly
clamped to the table. NEVER hold the workpiece
by hand during operation. Milling a workpiece
that is not properly secured to the table or in a
vise could cause the workpiece to be ejected at
the operator with deadly force!