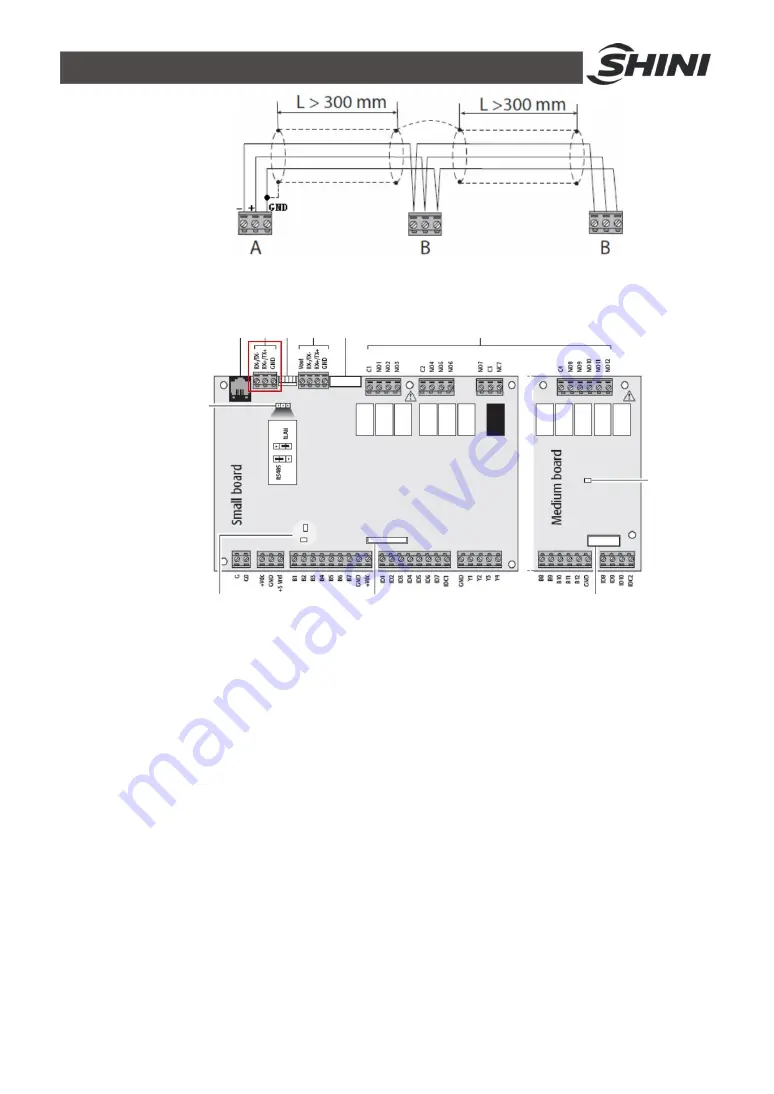
27(44)
Picture 3-8: Communication Line Connection
2) Communication Interface
Picture 3-9: Communication Interface Diagram
Note: The communication cable plug-in and plug-out must be carried
out when the controller is powered off. Otherwise, the
communication interface would be damaged easily.
Note: The communication cable must be connected according to the
specification. Otherwise the communication may be abnormal.
Summary of Contents for SICC-120A-R2
Page 2: ......
Page 6: ...6 44...
Page 43: ...43 44 Attachment Electrical Diagram...
Page 44: ...44 44...