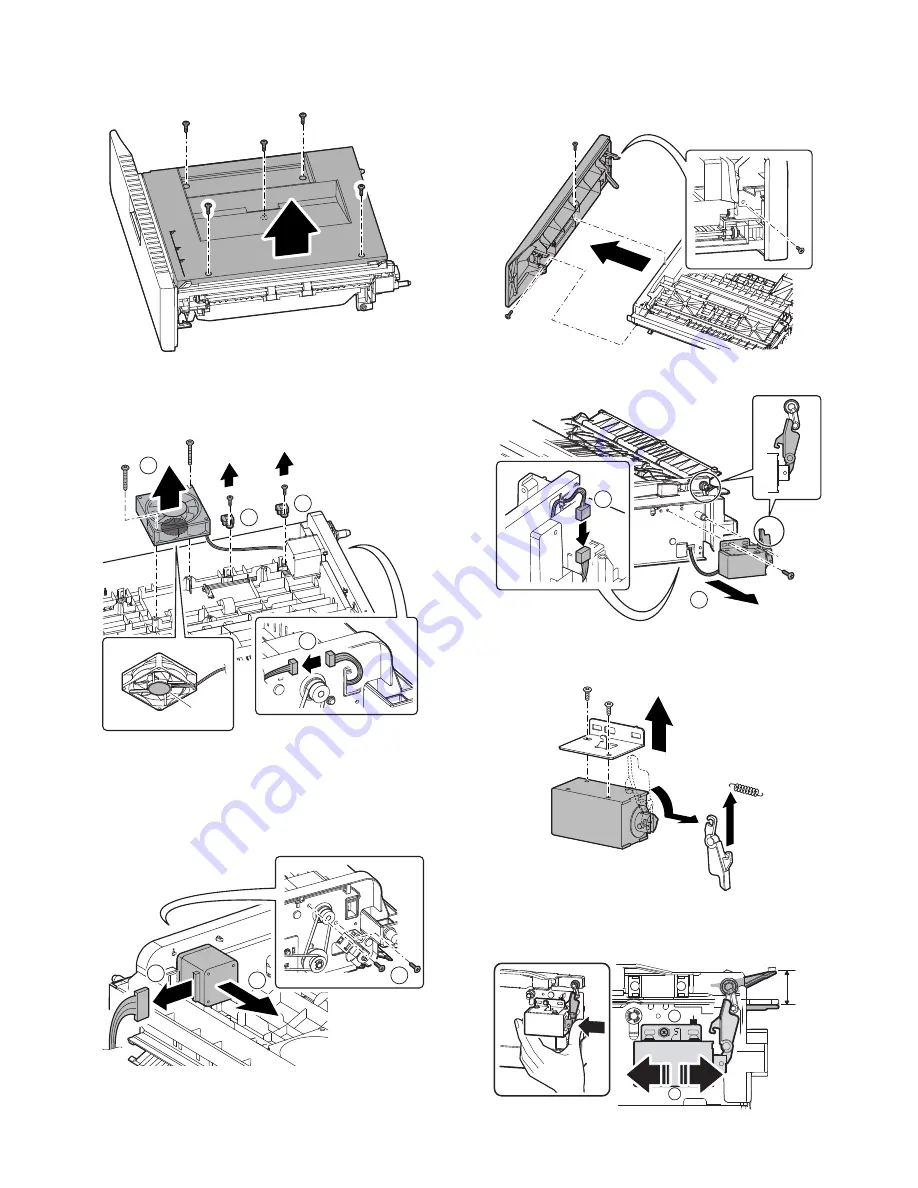
MX-FN10 DISASSEMBLY AND ASSEMBLY 6 – 8
(4) Interface Fan
1)
Remove the paper pass unit.
2)
Remove the bottom cover.
3)
Remove the clamps, and disconnect the connector then
remove the interface fan.
* Install the interface fan so as the side with the label (A)
comes to the direction illustrated.
(5) Interface Transport Motor
1)
Remove the paper pass unit.
2)
Remove the bottom cover. (See (4).)
3)
Disconnect the connector, then remove the interface transport
motor.
(6) Entry Reverse Pass Solenoid.
1)
Remove the paper pass unit.
2)
Remove the bottom cover. (See (4).)
3)
Remove the front cover.
4)
Remove the solenoid unit.
5)
Remove each parts, then remove the entry reverse pass sole-
noid.
* Adjust so that the distance between the lower guide and the
upper guide flapper is 22mm with the solenoid plunger
pushed in. Install the entry reverse pass solenoid.
1
2
2
3
A
1
2
3
1
2
22mm
Summary of Contents for MX-FN10
Page 52: ...Memo ...
Page 53: ...Memo ...