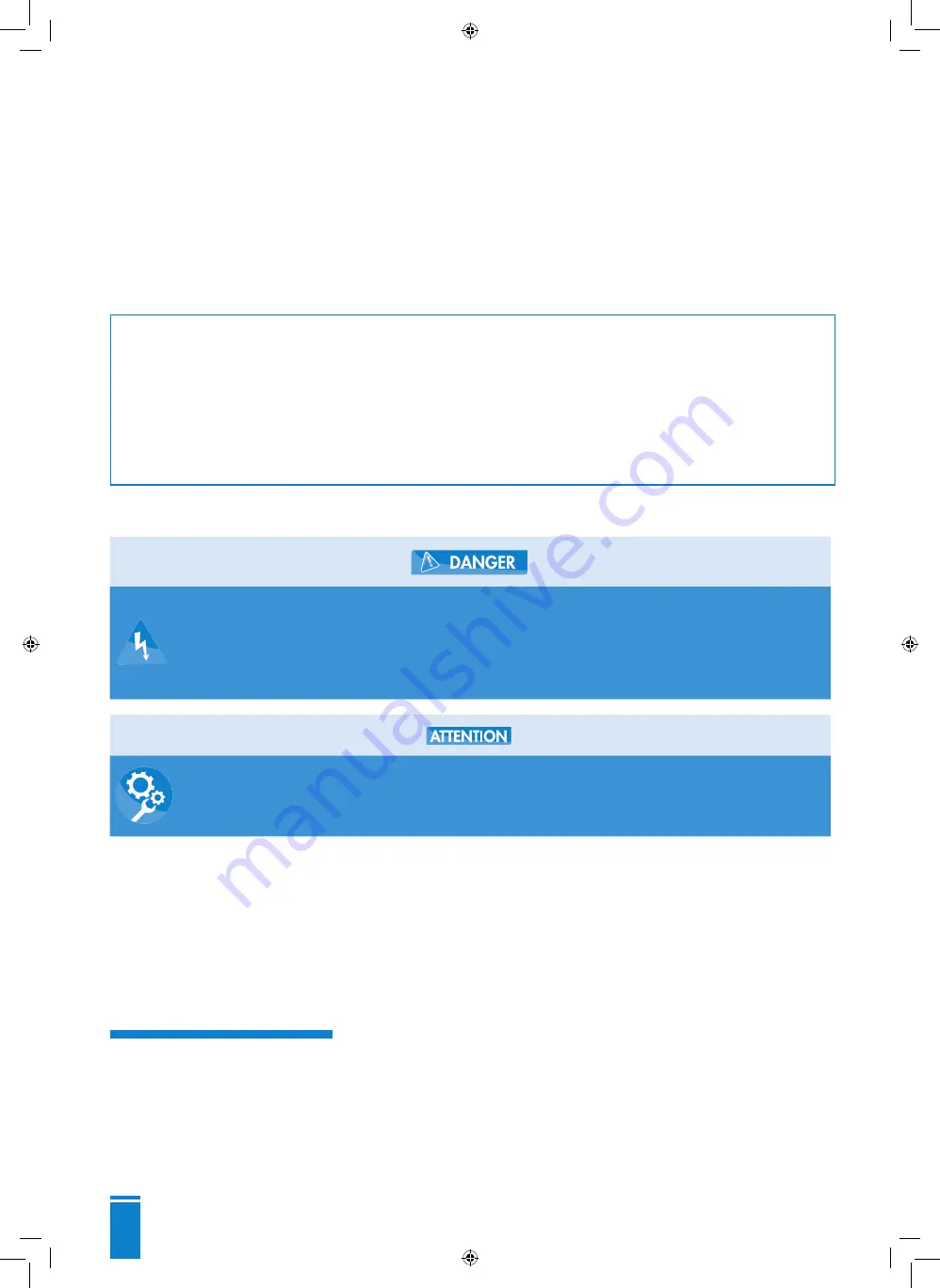
24
• The installation room is adequately lit.
• The plant room where the SANIPUMP
®
pumping station will be installed must be large enough to
allow a 600 mm clearance around and above the device to facilitate any maintenance operations.
• Stop valves must be fitted on the effluent inlet as well as on the discharge line, as close as possible
to the pumping station.
• Install a non-return valve on the pumping station outlet to prevent unintended start-up.
• The discharge line must be designed to prevent any back-flow of sewage.
• By fitting a non-return loop, located above the back-flow level, back-flow is avoided.
PLEASE NOTE:
Unless otherwise specified locally, the back-flow level is the level of the
highway (roads, pavement, etc.). Extend this line after the non-return loop through a larger
diameter pipe.
• The pumped fluid is appropriate and authorised by this documentation (paragraph 3.5).
• In case of discharge of greasy effluents, the use of a degreasing tank is essential.
Wastewater other than those mentioned above, for example, of artisanal or industrial origin,
must not be discharged into the pipes without prior treatment.
3.7 Electrical connection
Electrical connection work performed by an unqualified individual. Risk of
death by electric shock!
➜
The electrical connection must be carried out by a qualified and licensed
electrician.
➜
The electrical installation must meet the current standards in the country.
Wrong supply voltage. Damage to the pumping station!
➜
The supply voltage must not differ by more than 6% of the rated voltage
specified on the rating plate.
Only carry out the electrical connections after the final connections have been completed.
The device must be connected to an earthed junction box. The power supply circuit must be
protected by a 30 mA differential circuit breaker rated at 16 A.
The connection must be used exclusively to provide the power to the product.
If the power cord is damaged, to prevent possible danger, it must be replaced by the manufacturer,
customer service team or a similarly qualified individual.
4. ACTIVATION
4.1 Prerequisites for commissioning
Before commissioning the pumping station, make sure that the electrical connection of the pumping
station has been carried out correctly.
• The safety instructions have been followed.
Summary of Contents for SaniPump
Page 2: ......
Page 137: ...LpA A 137...
Page 138: ...138 1 8 I 30 3...
Page 139: ...139 SANIPUMP SANIPUMP SANIPUMP SANIPUMP 1 1 1 2 SANIPUMP 1 3...
Page 140: ...140 1 4 1 5 4 144 1 6 2 2 1 2 2...
Page 143: ...143 3 5 3 6 SANIPUMP SANIPUMP 5 500 SANIPUMP 600 3 5...
Page 144: ...144 3 7 6 16 30 4 4 1 4 2 40 C 50 C 70 C 5 S3 30...
Page 145: ...145 4 3 4 4 10 4 5 3 6 30 4 6 1 2 3 4 5 6...
Page 146: ...146 5...
Page 147: ...147 6 1 6 SFA SFA SFA SFA SFA SFA...
Page 161: ...ND dB A 161...
Page 162: ...162 1 30 3...
Page 163: ...163 SANIPUMP SANIPUMP SANIPUMP 1 1 1 2 SANIPUMP 1 3...
Page 164: ...164 1 4 1 5 168 4 1 6 2 2 1 2 2 SANIPUMP 10 13 kg...
Page 167: ...167 3 5 3 6 SANIPUMP SANIPUMP 5m 500mm SANIPUMP 600mm 3 5...
Page 168: ...168 3 7 6 30 mA 16A 4 4 1 4 2 40 C 70 C 5 50 C S3 30 4 3...
Page 169: ...169 4 4 10 4 5 3 6 30mA 4 6 1 2 3 4 5 6...
Page 170: ...170 5 6 1...
Page 171: ...171 6 SFA SFA SFA SFA SFA SFA...
Page 173: ...ND A LpA 173...
Page 174: ...174 1 8 I 30 3...
Page 175: ...175 SANIPUMP SANIPUMP SANIPUMP 1 1 1 2 SANIPUMP 1 3...
Page 176: ...176 1 4 1 5 180 4 1 6 2 2 1 2 2...
Page 179: ...179 3 5 SANIPUMP 3 6 5 SANIPUMP 500 SANIPUMP 600...
Page 180: ...180 3 5 3 7 6 16 30 4 4 1 4 2...
Page 181: ...181 70 40 50 5 S3 30 4 3 4 4 4 5 3 6 30 4 6 1 2 3 4 5 6...
Page 182: ...182 5 6 1...
Page 183: ...183 6 SFA SFA SFA SFA SFA SFA...