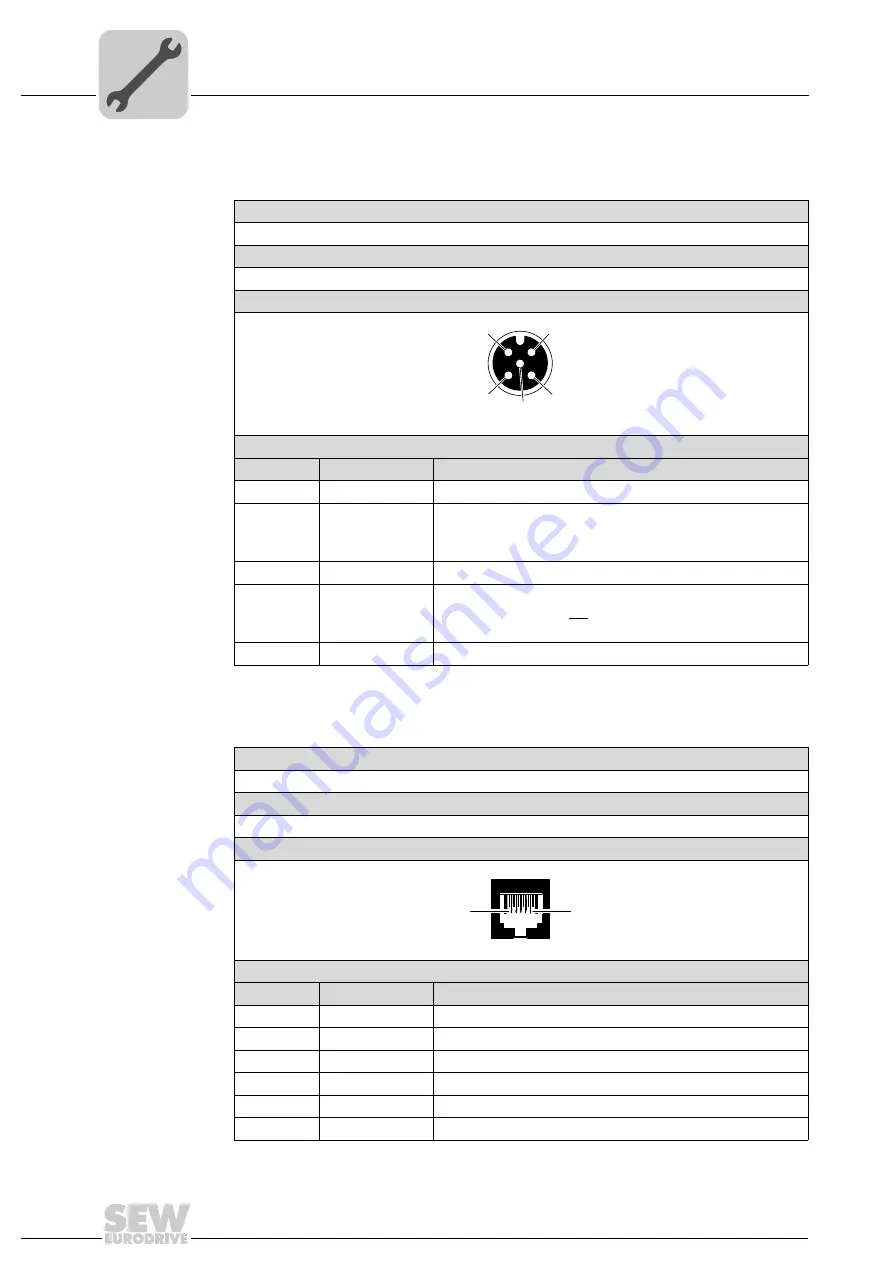
26
Compact Operating Instructions – MOVIFIT® basic
5
Connections of MOVIFIT
®
basic with binary control
Electrical Installation
5.6.3
X13: Signal outputs 0 and 1 of MOVIFIT
®
basic
The following table informs about this connection:
5.6.4
X50: Diagnostic interface
The following table informs about this connection:
Function
Binary outputs 0 and 1
Connection type
M12, 5-pole, female, A-coded
Wiring diagram
2264816267
Assignment
No.
Name
Function
1
+24 V
DC 24 V output
2
DO1
Binary output 1 (manual mode)
0: MOVIFIT
®
basic control via control signals
1: Manual control of MOVIFIT
®
basic
3
0V24
0V24 reference potential
4
DO0
Binary output 0 (ready signal)
0: MOVIFIT
®
basic is not ready
1: MOVIFIT
®
basic is ready
5
PE
Equipotential bonding/protective earth conductor
1
4
3
2
5
Function
Diagnostics and programming interface
Connection type
RJ11 (6P6C)
Wiring diagram
3163123211
Assignment
No.
Name
Function
1
n. c.
Not connected
2
RS+
RS-485 data line (+)
3
RS
−
RS-485 data cable (–)
4
+24 V
DC 24 V output for keypad
5
0V24
0V24 reference potential for keypad
6
n. c.
Not connected
1
6