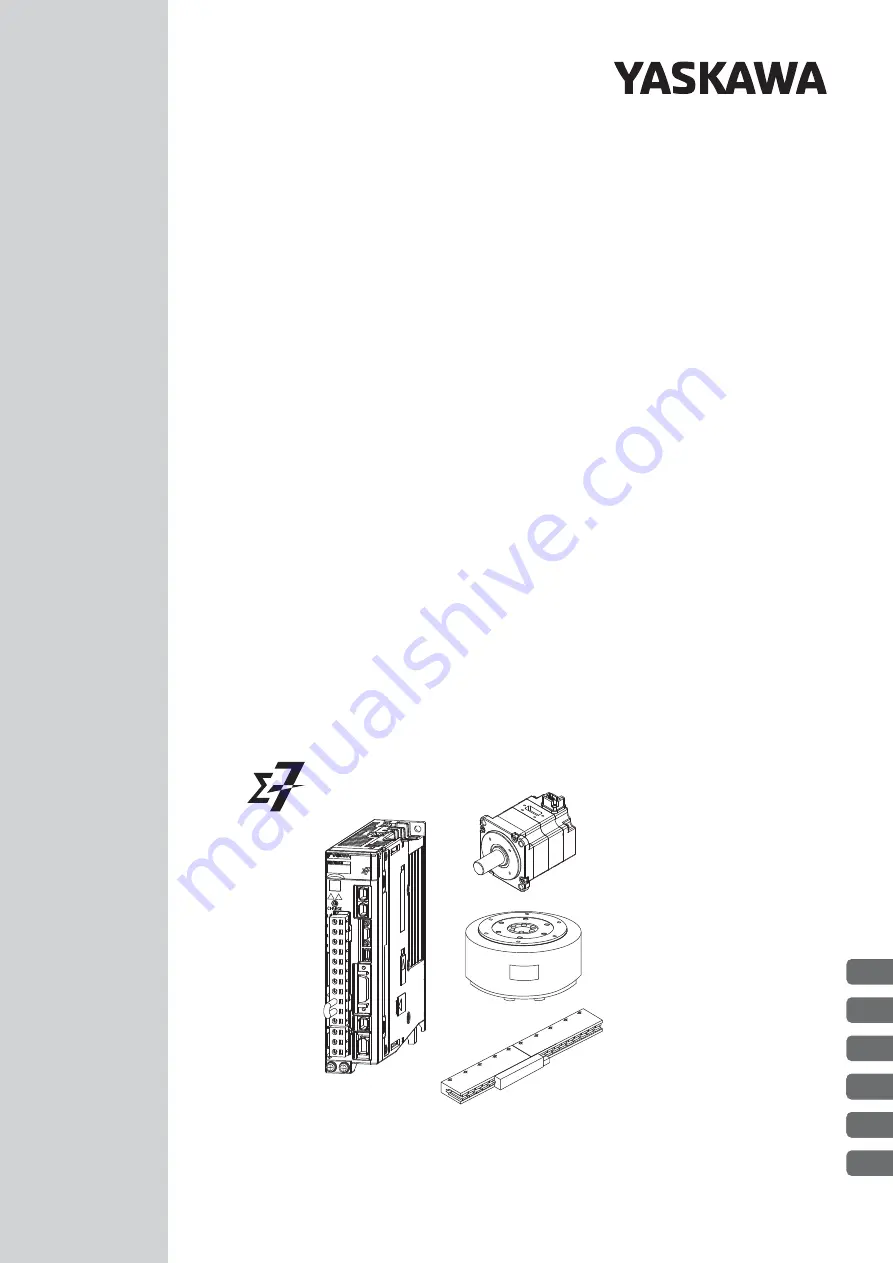
Model: SGD7S-
20
F40
, and -
20
F41
-7-Series AC Servo Drive
MANUAL NO. SIEP S800001 94C
-7S SERVOPACK with
FT/EX Specification
for Press and Injection
Molding Application
Pressure Feedback Control
Maintenance
Parameter Lists
Basic Information on
SERVOPACKs
SERVOPACK Ratings and
Specifications
1
2
3
4
5
6
Speed/Torque (Pressure)
Table Operation
Product Manual
Summary of Contents for SGD7S-R70A20A023F40B
Page 52: ...3 7 Monitoring 3 23...