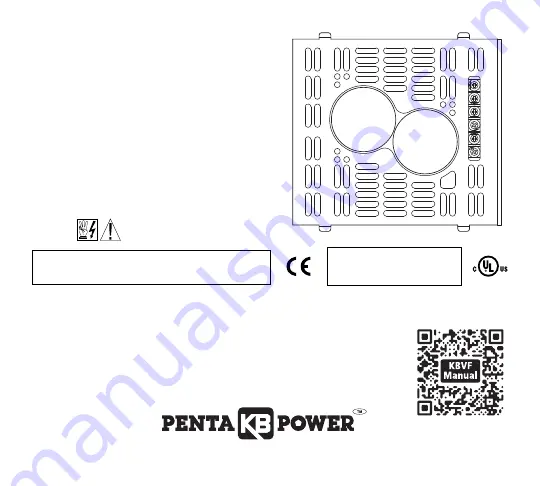
Installation & Operation Manual
KBVF SERIES
Variable Speed / Soft-Start
with Electronic Motor Overload Protection
1
Rated for 208-230 Volt 50 & 60 Hz
3-Phase & PSC
2
AC Induction Motors
from Subfractional thru 1
1
⁄
2
HP
Operates from 115 and 208/230 Volt
50/60 Hz AC Line Input
3
See Safety Warning,
on pages 8 and 9.
Note: The drive is factory set for
60 Hz motors. For 50 Hz motors,
see Section 6.2, on page 25.
The information contained in this manual is intended to be accurate. However, the manufacturer retains the right
to make changes in design which may not be included herein.
The QR code link to
this manual is also
located on the drive.
Notes 1.
UL approved as an electronic overload protector for motors.
2.
Custom software
is required for PSC motors. See PSC Motor Addendum (Part No. A42142).
3.
Do not use
this drive with GFCIs. Special software is required — Contact our Sales Department.
4.
Requires CE approved RFI /Filter. See RFI Filters & Chokes Selection Guide D-321
(Part No. A42027) for selection of filters to meet the Industrial or Residential Standard.
© 2014 KB Electronics, Inc.
(see back cover)
A Complete Line of Motor Drives
Chassis / IP-20 AC Drives
4
This Manual Covers Models
KBVF-21D, 22D, 13, 23, 23D, 23P, 14, 24, 24D, 24P, 26D