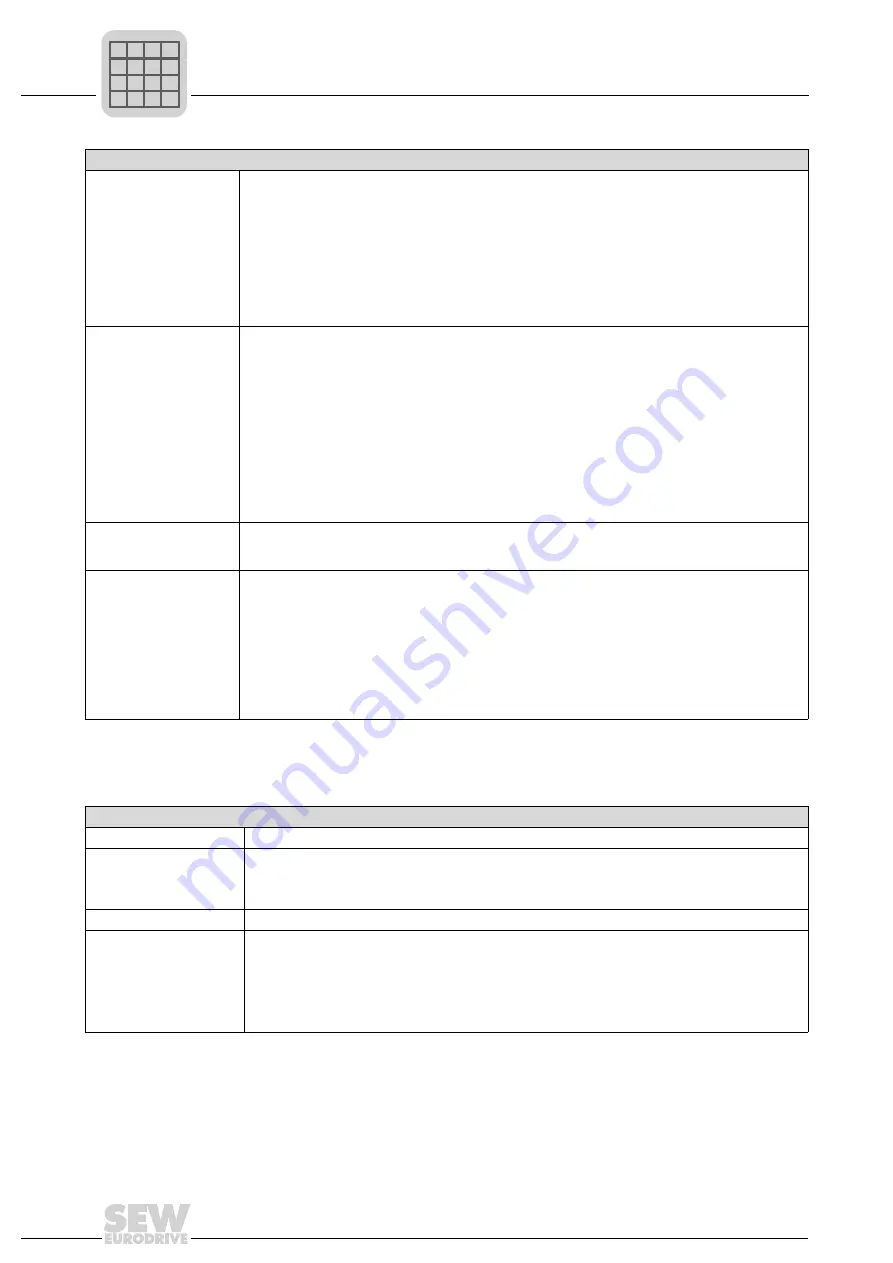
8
Technical Data and Dimension Drawings
OST11B option
80
Manual – MOVI-PLC
®
basic DHP11B.. controller
8.3
OST11B option
System bus CAN 2
X32:1 ... X32:3
•
System bus CAN 1 and CAN 2 to CAN specification 2.0, parts A and B, transmission technology to
ISO 11898, max. 64 stations,
•
The CAN 2 system bus is electrically isolated
•
Max. 64 stations per CAN system bus,
•
Max. 64 SCOM transmit objects / 32 receive objects per CAN system bus
•
Address range 0...127
•
baud rate: 125 kBaud...1 MBaud
•
If X32 or X33 is the bus terminator, you must connect a terminating resistor (120
Ê
) externally.
•
You can remove connectors X32 or X33 without interrupting the system bus.
•
The system bus can be run in layer 2 (SCOM cyclic, acyclic) or in accordance with the SEW-
MOVILINK
®
protocol.
System bus CAN 1
X33:1 ... X33:3
PROFIBUS connection
X30:1 ... X30:9
Bus
termination
Automatic baud rate
recognition
Protocol
options
GSD file
DP ident. number
Via 9-pin sub D connector, pin assignment according to IEC 61158
Not integrated. Activate bus termination with suitable PROFIBUS connector with switchable terminating
resistors
9.6 kBaud ... 12 MBaud
PROFIBUS-DP and DP-V1 to IEC 61158
SEW_6007.GSD
6007
hex
= 24583
dec
RS485 interface COM1
X34:1 ... X34:4
•
For connection of an engineering PC or a DOP11A operator terminal.
•
E/A standard, 57.6 / 9.6 kBaud, max. cable length 200 m
•
Dynamic terminating resistor with fixed installation
Engineering
Engineering takes place via one of the following interfaces:
•
RS485 interface (X34)
•
CAN 1 interface (X33)
•
CAN 2 interface (X32)
•
PROFIBUS interface (X30)
Configuration and startup of all SEW components connected to the MOVI-PLC
®
basic
DHP11B..
controller can take place on the MOVI-PLC
®
basic
DHP11B.. controller itself.
Configuration and startup of the MOVI-PLC
®
basic
DHP11B.. controller cannot be performed via
the inverters.
•
MOVITOOLS
®
MotionStudio PC software with PLC Editor
MOVI-PLC
®
basic
DHP11B.. controller
OST11B option
Part number
1 820 544 5
Electrical supply
•
Power consumption P
max
= 1.5 W (only OST11B)
•
Power consumption P
max
= 6 W (MOVI-PLC
®
basic
DHP11B.. and OST11B installed in
MOVIDRIVE
®
MDX61B)
•
The OST11B option is supplied by the MOVI-PLC
®
basic
DHP11B.. controller with DC 24 V.
Potential level
COM2 is isolated from the MOVI-PLC
®
basic
DHP11B.. controller
RS485 interface COM2
X35:1 ... X35:4
X36:1 ... X36:3
•
For connection of an engineering PC, a DOP11A operator terminal or a gearmotor with integrated
frequency inverter MOVIMOT
®
•
I/O standard, 57.6 kBaud, max. total cable length 200 m, integrated dynamic terminating resistor
permanently installed
•
X35 and X36 are connected in parallel
•
You can connect a gearmotor with integrated frequency inverter MOVIMOT
®
to X36. Do not connect
an engineering PC or DOP11A operator terminal to COM2.
P
i
f
kVA
Hz
n