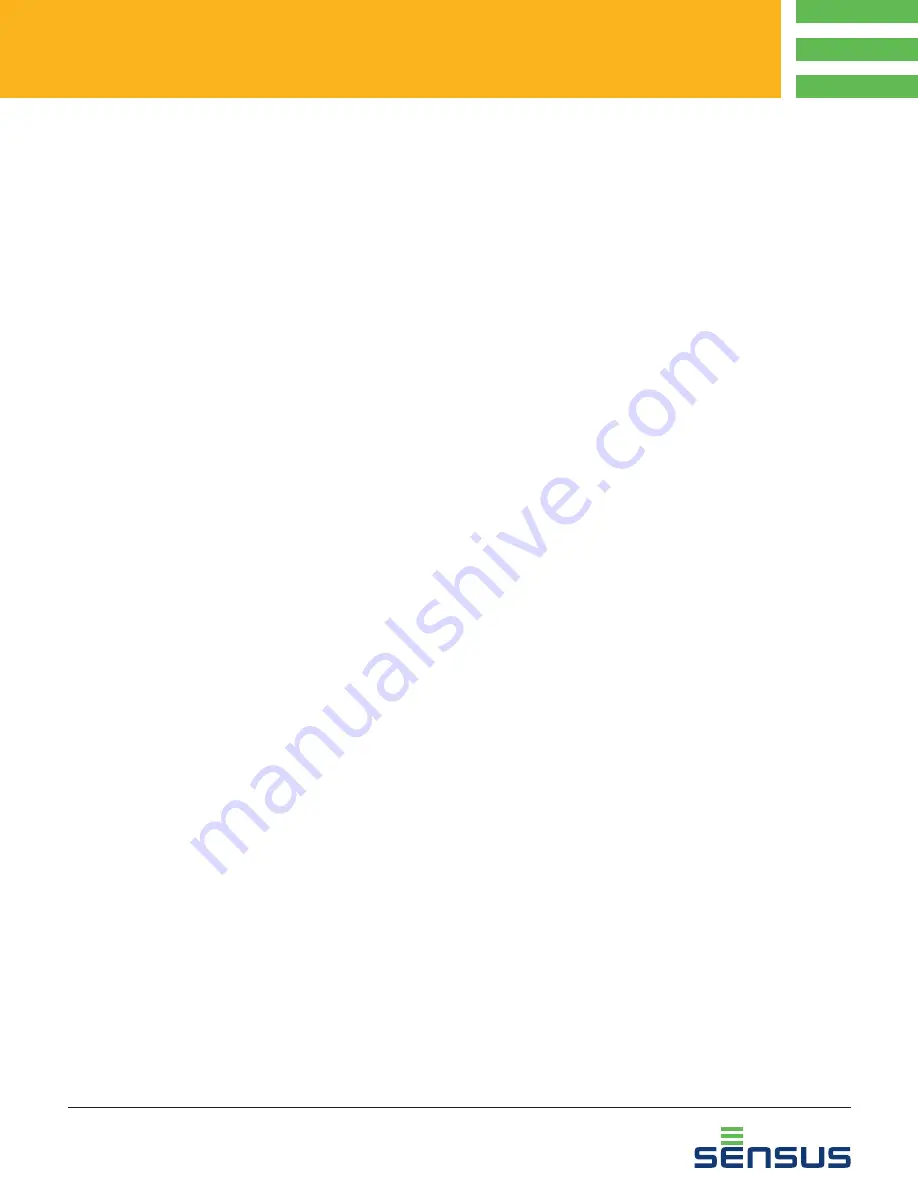
*This document replaces RM-1329-R7
IN-G-REG-13-29-0814-03-A*
Model 122 Regulators
Installation and Maintenance Instructions
Introduction
The Model 122 Regulator illustrates a combination of capacity,
performance and value. The streamline body passages provide
large capacity. Internal control is standard with external control
also available. The 122 has a fast speed of response, yet is stable
in operation. Soft seats ensure positive tight shutoff. Orifices are
replaceable. Springs are color coded.
And it is also available as a zero governor or atmospheric
regulator, a differential regulator and a relief valve or back-
pressure regulator.
Installation
1.
Examine the regulator for shipping damage.
2.
Check nameplate data. Be sure regulator conforms with what
was ordered.
3.
Inside of regulator and piping must be clean and free of dirt.
Remove all dirt and debris before installing regulator. Failure
to remove dirt/debris could result in regulator damage
or trouble.
4.
Remove all shipping screens and covers from the regulator.
Do not let dirt get inside the regulator.
5.
Install the regulator.
Make sure the inlet and outlet are correctly connected. High
pressure connects to the inlet. The flow arrow must point
downstream.
6.
Screwed connections must conform with good piping practice
free of excess thread engagement per ANSI B2.1. Apply pipe
joint compound to male threads only.
7.
The model 122 regulator is usually installed right side-up
as shown on the Typical installation drawing (See Page 3).
It may, however, be installed upside down. Although, when
inverted it may be necessary to readjust the set-point.
Caution:
Do not install sideways.
The diaphragm should be horizontal.
8.
On indoor installations requiring venting outdoors, run the vent
piping as short and indirect as possible with minimum bends
and elbows. Use the same size pipe as the vent connections
on the regulator. With natural gas, or any other hazardous
gas, vent to a safe place outdoors in case gas should
accidentally be discharged. Screen and protect the outdoor
opening to guard against water, ice, dirt, debris or insects.
This item only applies to regulators requiring a control line. It
does not apply to 122 Regulators with internal control. Install
the control line. Connect it into the outlet piping at least 5 pipe
diameters downstream from the regulator.
Caution:
a.
On backpressure regulators and relief valves with external
control, the control line connects into the
inlet
piping.
b.
Do not install any automatic shutoff device that closes
completely between the regulator and the control line
connection into the piping.
To avoid excessive turbulence, the connection should be clean
and smooth on the inside and be located in straight pipe clear
of valves and fittings. Keep the inside of the control line clean
and protect it from corrosion. Pitch it away from the regulator
and avoid moisture pockets. It must be strong (¼" or larger
steel tubing or pipe is preferred). It must be well protected
against breakage (remember, regulators open wide if the
control breaks).
9.
Make sure the regulator is correctly connected and adequately
supported and pipe joints are tight.
Start-Up
A.
The inlet and outlet shutoff valves should both be closed. If a
by-pass is used, the bypass valve should also be closed.
B.
Note the set-point (set-point is the outlet pressure the
regulator is adjusted to deliver). Regulator is factory adjusted
to the set-point specified on the order.
Caution:
This caution applies where the piping downstream of the
outlet shutoff valve is pressured. That pressure must not
exceed the regulator set-point by more than 2 psi (see
“Maximum Emergency Pressures”, Page 11).
C.
Slowly and carefully open the inlet shutoff valve just enough to
allow
inlet pressure
to build up slowly in the regulator until it
is fully pressured.
Caution:
During start-up a pressure gauge must be used on the
regulator
outlet
pressure and carefully watched. While
inlet
pressure builds up,
outlet
pressure must not exceed set-point
by more than 1 psi. If
outlet
pressure begins to exceed
set-point by more than 1 psi, close the
inlet
shutoff valve.
This indicates the regulator is not closing properly. Check and
make necessary corrections before proceeding with start-up.
If regulator
outlet
pressure exceeds set-point by more than
2 psi, refer to “Maximum Emergency Pressures”, Page 11 for
instructions.
D.
Check installation for leaks.
E.
Slowly open the outlet shutoff valve to allow a small flow
(approximately 250 SCFH). Make sure the flow of gas does
not create a hazard.
NOTE:
If piping downstream of outlet shutoff valve is
pressurized, see “Caution” under B.
F.
With gas flowing, check for correct inlet and outlet pressures.
It may be necessary to further open the inlet shutoff valve to
maintain full inlet pressure.
G.
Make sure the regulator closes tight (tight lock-up). To do this,
reduce flow to zero by slowly closing the outlet shutoff valve.
Outlet pressure should not exceed set-point by more than
3" w.c.
H.
Fully open inlet and outlet shutoff valves slowly and carefully.
Watch pressure gauges.
I.
Complete start-up by making sure there are no leaks.