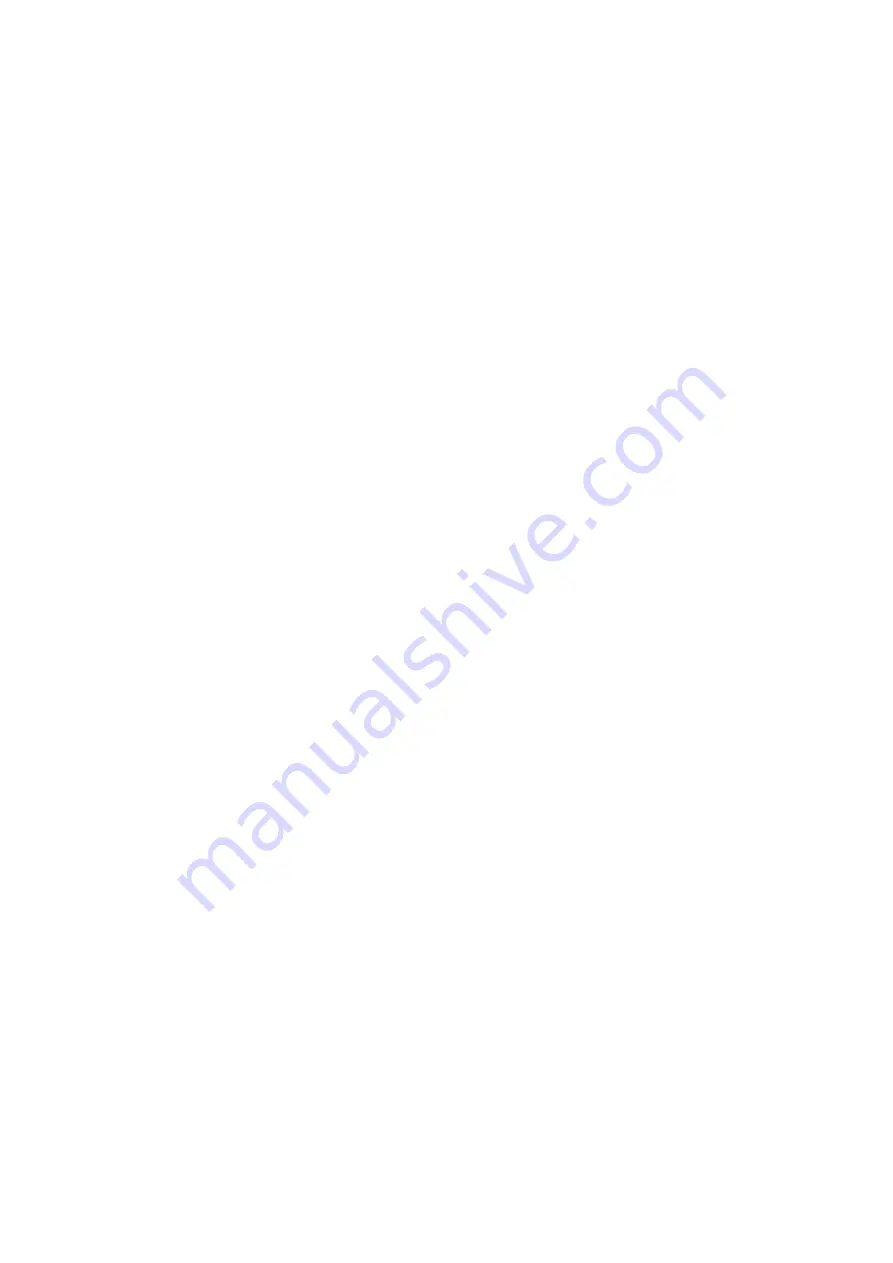
12
TD_MRI1-IU_05.04_GB
6
Relay testing and
commissioning
The test instructions following below help to verify the
protection relay performance before or during commis-
sioning of the protection system. To avoid a relay
damage and to ensure a correct relay operation, be
sure that:
•
the auxiliary power supply rating corresponds to the
auxiliary voltage on site.
•
the rated current and rated voltage of the relay cor-
respond to the plant data on site.
•
the current transformer circuits and voltage trans-
former circuits are connected to the relay correctly.
•
all signal circuits and output relay circuits are con-
nected correctly.
6.1 Power-On
NOTE!
Prior to switch on the auxiliary power supply, be sure
that the auxiliary supply voltage corresponds with the
rated data on the type plate.
Switch on the auxiliary power supply to the relay and
check that the message "ISEG" appears on the display
and the self supervision alarm relay (watchdog) is en-
ergised (Contact terminals D7 and E7 closed).
6.2 Testing the output relays and LEDs
NOTE!
Prior to commencing this test, interrupt the trip circuit to
the circuit breaker if tripping is not desired.
By pressing the push button <TRIP> once, the display
shows the first part of the software version of the relay
(e.g. „D08-“). By pressing the push button <TRIP>
twice, the display shows the second part of the soft-
ware version of the relay (e.g. „4.01“). The software
version should be quoted in all correspondence. Press-
ing the <TRIP> button once more, the display shows
"PSW?". Please enter the correct password to proceed
with the test. The message "TRI?" will follow. Confirm
this message by pressing the push button <TRIP>
again. All output relays and LEDs should then be acti-
vated and the self supervision alarm relay (watchdog)
be deactivated one after another with a time interval
of
3 second. Thereafter, reset all output relays back to their
normal positions by pressing the push button
<SELECT/RESET> (about 3 s).
6.3 Checking the set values
By repeatedly pressing the push button <SELECT>, all
relay set values may be checked. Set value modifica-
tion can be done with the push button <+><-> and
<ENTER>. For detailed information about that, please
refer to chapter 5.
For a correct relay operation, be sure that the fre-
quency set value (f=50/60) has been selected ac-
cording to your system frequency (50 or 60 Hz).
6.4 Secondary injection test
6.4.1
Test equipment
•
Voltmeter, Ammeter with class 1 or better
•
Auxiliary power supply with the voltage correspond-
ing to the rated data on the type plate
•
Single-phase current supply unit (adjustable from
0 to
≥
4 x In)
•
Three-phase voltage supply unit (adjustable from 0 to
≥
1.2 x Un)
•
Timer to measure the operating time
(Accuracy class
≤
±
10 ms)
•
Switching device
•
Test leads and tools
Summary of Contents for HighTECH Line MRI1IU
Page 21: ...TD_MRI1 IU_05 04_GB 21 ...